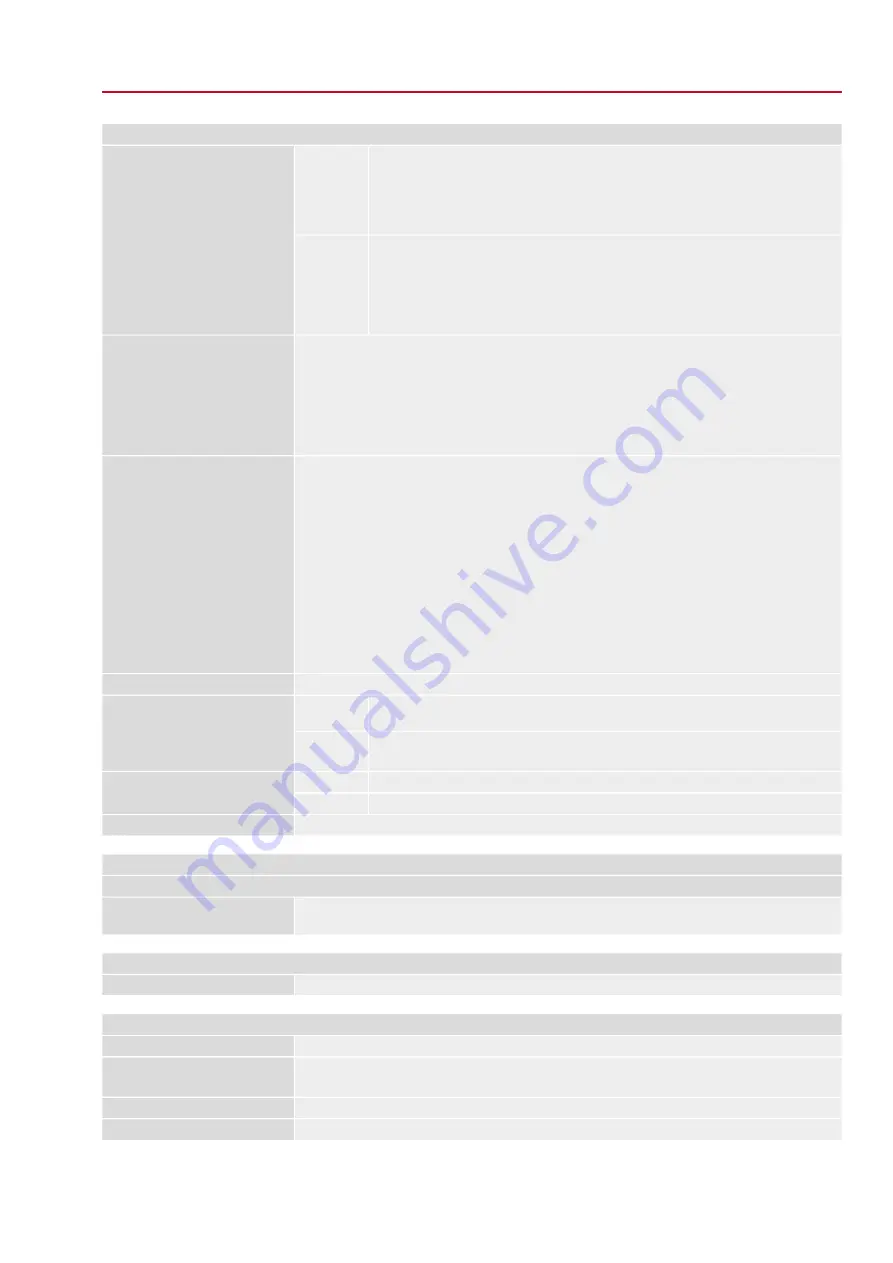
Features and functions
●
EMERGENCY operation (programmable behaviour)
-
Via additional input (option, low active) or via fieldbus interface
-
Reaction can be selected: STOP, run to end position (OPEN, CLOSED) position
at defined speed
-
Torque monitoring can be by-passed during EMERGENCY operation
Standard:
Safety functions
●
Enabling local controls via Enable LOCAL digital input: Thus, actuator operation can
be enabled or disabled via push buttons on local controls.
●
Interlock for main/by-pass valve: Enabling the operation commands OPEN or CLOSE
via two digital inputs
●
PVST (Partial Valve Stroke Test): programmable to check the function of both actuator
and actuator controls: Direction, stroke, operation time, reversing time
Options:
●
Valve overload protection: adjustable, results in switching off and generates fault signal
●
Motor temperature monitoring (thermal monitoring): results in switching off and generates fault indic-
ation
●
Monitoring the heater within actuator: generates warning signal
●
Monitoring of permissible on-time and number of starts: adjustable, generates warning signal
●
Operation time monitoring: adjustable, generates warning signal
●
Phase failure monitoring: results in switching off and generates fault signal
Monitoring function
●
Electronic device ID with order and product data
●
Logging of operating data: A resettable counter and a lifetime counter each for:
-
Motor running time, number of starts, torque switch trippings in end position CLOSED, limit
switch trippings in end position CLOSED, torque switch trippings in end position OPEN, limit
switch trippings in end position OPEN, torque faults CLOSE, torque faults OPEN, motor protection
trippings
●
Time-stamped event report with history for setting, operation and faults:
-
Status signals according to NAMUR recommendation NE 107: "Failure", "Function check", "Out
of specification", "Maintenance required"
●
Torque characteristics (for version with MWG in actuator):
-
3 torque characteristics (torque-travel characteristic) for opening and closing directions can be
saved separately.
-
Torque characteristics stored can be shown on the display.
Diagnostic functions
PTC tripping device (TMS module) in combination with PTC thermistors within actuator motor
Motor protection evaluation
AUMA Ex plug/socket connector (KT); screw-type motor terminals; push-in type control
terminals
Standard:
Electrical connection
●
AUMA Ex plug/socket connector with terminal blocks (KES)
●
AUMA Ex plug/socket connector with screw-type terminals (KP)
Options:
Metric threads
Standard:
Threads for cable entries
Pg-threads, NPT-threads, G-threads
Options:
Refer to name plate
Wiring diagram
For version with MWG within actuator
Setting of limit and torque switching via local controls
Via fieldbus interface
Galvanically isolated analogue output 0/4 – 20 mA (load max. 500
Ω
).
Torque feedback signal
Settings/programming the Modbus RTU interface
Baud rate, parity and Modbus address are set via the display of actuator controls
Setting the Modbus RTU interface
General data of the Modbus RTU interface
Modbus RTU according to IEC 61158 and IEC 61784
Communication protocol
●
Line (fieldbus) structure. When using repeaters, tree structures can also be implemented.
●
Coupling and uncoupling of devices during operation without affecting other devices is possible.
Network topology
Twisted, screened copper cable according to IEC 61158
Transmission medium
EIA-485 (RS-485)
Fieldbus interface
93
SQVEx 05.2 – SQVEx 14.2/ SQRVEx 05.2 – SQRVEx 14.2 Control unit: electronic (MWG)
ACVExC 01.2 Modbus RTU
Technical data