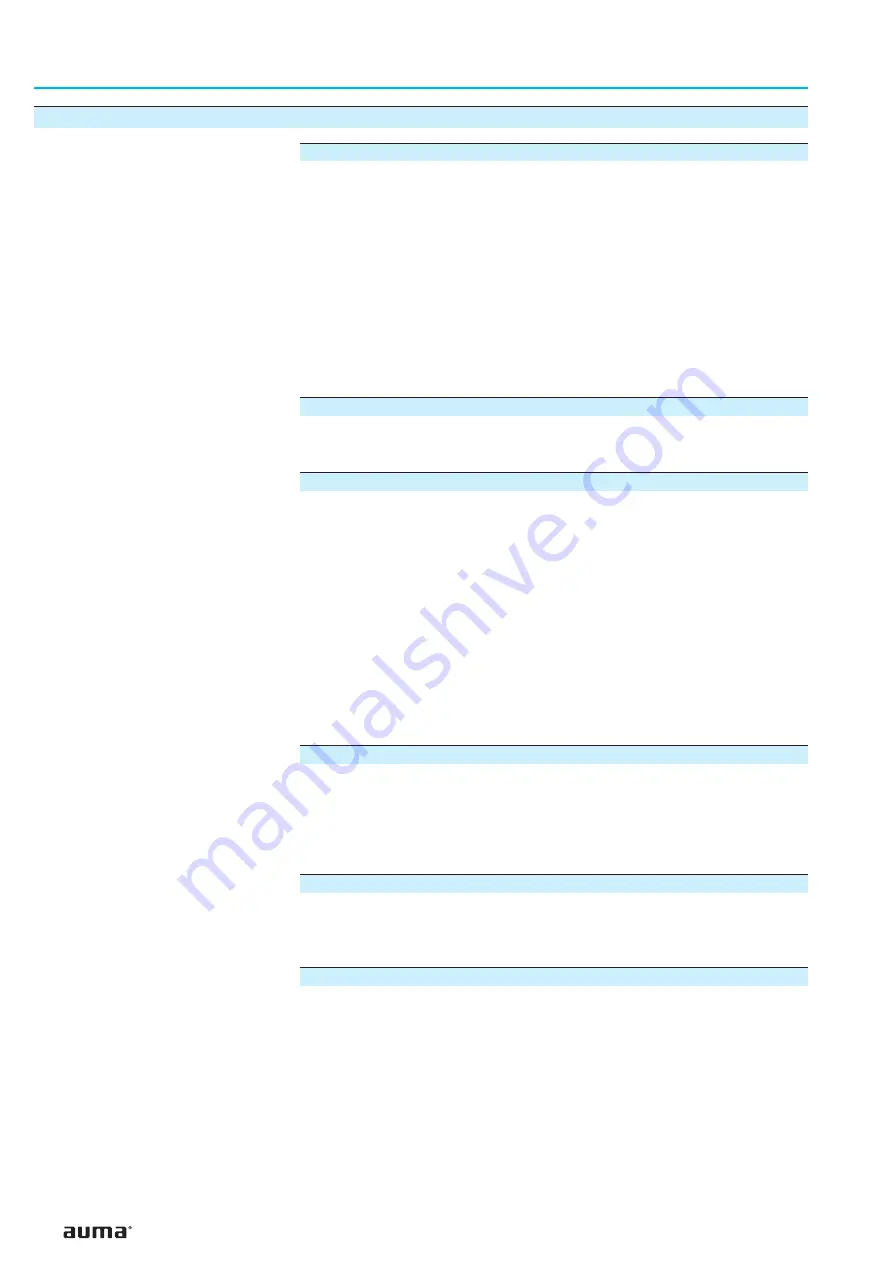
24.
Enclosure protection IP 68 (option)
Definition
According to EN 60 529, the conditions for meeting the requirements of
enclosure protection IP 68 are to be agreed between manufacturer and
user.
AUMA actuators and controls in enclosure protection IP 68 meet the follow-
ing requirements according to AUMA:
.
Duration of submersion in water max. 72 hours
.
Head of water max. 6 m
.
Up to 10 operations during submersion
.
Modulating duty is not possible during submersion
Enclosure protection IP 68 refers to the interior of the actuators (motor,
gearing, switch compartment, controls, and terminal compartment).
Inspection
AUMA actuators and controls in enclosure protection IP 68 undergo a rou-
tine testing for tightness in the factory.
Cable glands
.
For the entries of the motor and control cables, appropriate cable glands
in enclosure protection IP 68 must be used. The size of the cable glands
must be suitable for the outside diameter of the cables, refer to recommen-
dations of the cable gland manufacturers.
.
As standard, actuators and controls are delivered without cable glands.
For delivery, the threads are sealed with plugs in the factory.
.
When ordered, cable glands can also be supplied by AUMA at an addi-
tional charge. For this, it is necessary to state the outside diameter of the
cables.
.
The cable glands must be sealed against the housing at the thread with an
O-ring.
.
It is recommended to additionally apply a liquid sealing material
(Loctite or similar).
Commissioning
When commissioning, the following should be observed:
.
Sealing faces of housing and covers must be clean.
.
O-rings of the covers must not be damaged.
.
A thin film of non-acidic grease should be applied to sealing faces.
.
Covers should be tightened evenly and firmly.
After submersion
.
Check actuator.
.
In case of ingress of water, dry actuator correctly and check for proper
function.
Further notes
When using output drive types A and AF (stem nut), it cannot be prevented
that water enters the hollow shaft along the valve stem during submersion.
This leads to corrosion. The water also enters the axial bearings of output
drive type A, causing corrosion and damage to the bearings. The output
drive types A and AF should therefore not be used during submersion.
50
Multi-turn actuators SA 07.1 – SA 30.1/SAR 07.1 – SAR 30.1
with actuator controls AUMA MATIC AM 01.1/AM 02.1
Operation instructions