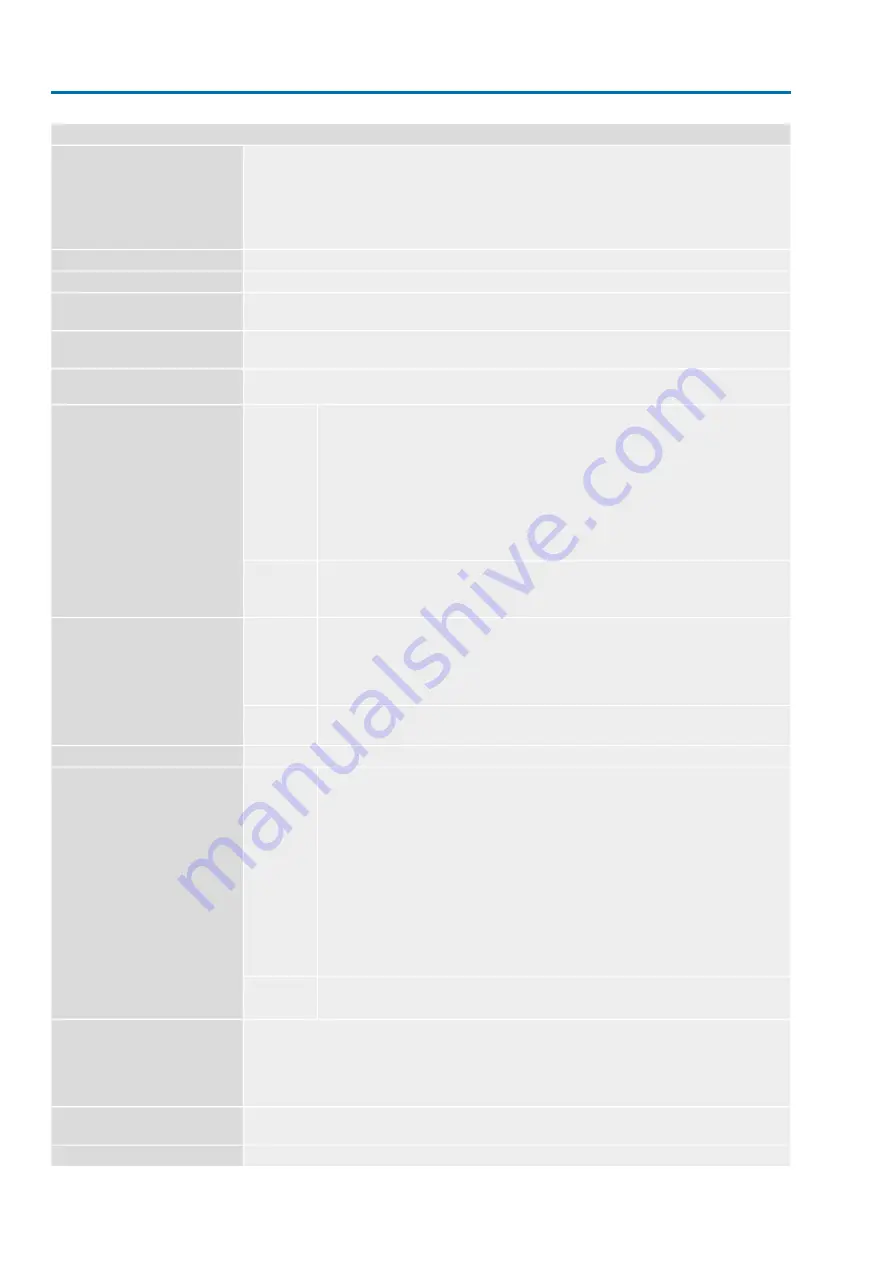
Features and functions
Standard voltages:
1-phase AC current:
100 – 240 V / 50 – 60 Hz
Permissible variation of mains voltage: ±10 %
Permissible variation of mains frequency: ±5 %
For current consumption, refer to Electrical data for PROFOX Part-turn actuators
Power supply
Category III according to IEC 60364-4-443
Overvoltage category
With integral motor controller (current consumption in standby mode 3 W)
Power electronics
Operation commands and setpoint via Profibus DP interface interface
Control
(input signals)
Via Profibus DP interface
Status signals
(output signals)
Access to parameters, the electronic name plate and the operating and diagnostic services with acyclic
write/read services
Profibus DP-V1 (option)
●
Via opto-isolator, with on common
●
Control voltage 24 V DC, current consumption: approx. 15 mA per input
●
Minimum pulse duration for shortest operation pulse: 100 ms
●
All digital inputs must be supplied with the same potential
●
All inputs can be configured as required
●
Standard assignment:
OPEN, CLOSE, I/O interface
I/O interface: Selection of control type (fieldbus interface or I/O input signals).
Factory setting: Fieldbus interface to active.
3 digital
Inputs:
I/O control
(input signals)
●
0/4 – 20 mA or 0 – 10 V
●
No galvanic isolation
●
Use as input, e.g. For a sensor signal which can be forwarded via Profibus.
Analogue in-
put
(option)
●
Freely configurable semi-conductor output contacts, per contact max. 24 V DC, 100
mA (resistive load)
●
Outputs can be configured as required
●
Standard assignment:
End position OPEN, end position CLOSED, collective fault signal
3 digital
Outputs:
Status signals via I/O
(Input signals)
●
Position feedback 0/4 – 20 mA (load 500
Ω
) or 0 – 10 V
●
No galvanic isolation
Analogue
output:
Auxiliary voltage 24 V DC, max. 40 mA for supply of control inputs, without galvanic isolation.
Voltage output (option)
●
Switch-off mode adjustable:
Limit or torque seating for end positions OPEN and CLOSED
●
Torque monitoring across the whole travel
●
Torque by-pass
●
Programmable EMERGENCY behaviour:
-
Digital input low active,
-
Reaction can be selected: Stop, run to end position CLOSED, run to end position
OPEN
●
Speed control
-
Ramps
-
Program operation profiles
-
Program either specific speed for OPEN and CLOSE operations or one digital input
Standard:
Functions
●
Positioner (always included for fieldbus versions)
-
Automatic adaptation of dead band (adaptive behaviour selectable)
Option:
Bluetooth class II chip, with a range min. 3 m in industrial environments, supports the SSP Bluetooth
profile (Serial Port Profile).
Required accessories:
●
AUMA CDT (Commissioning and Diagnostic Tool for Windows-based PC)
●
AUMA Assistant App (Commissioning and Diagnostic Tool for Android devices)
Bluetooth
Communication interface
Cable entry: 3 x M20 threads for cable glands.
Inside rail with spring clamp terminals for wire connection.
Electrical connection
Refer to name plate
Wiring diagram (basic version)
38
PROFOX / PF-M25 – PF-M100
Technical data
Profibus DP