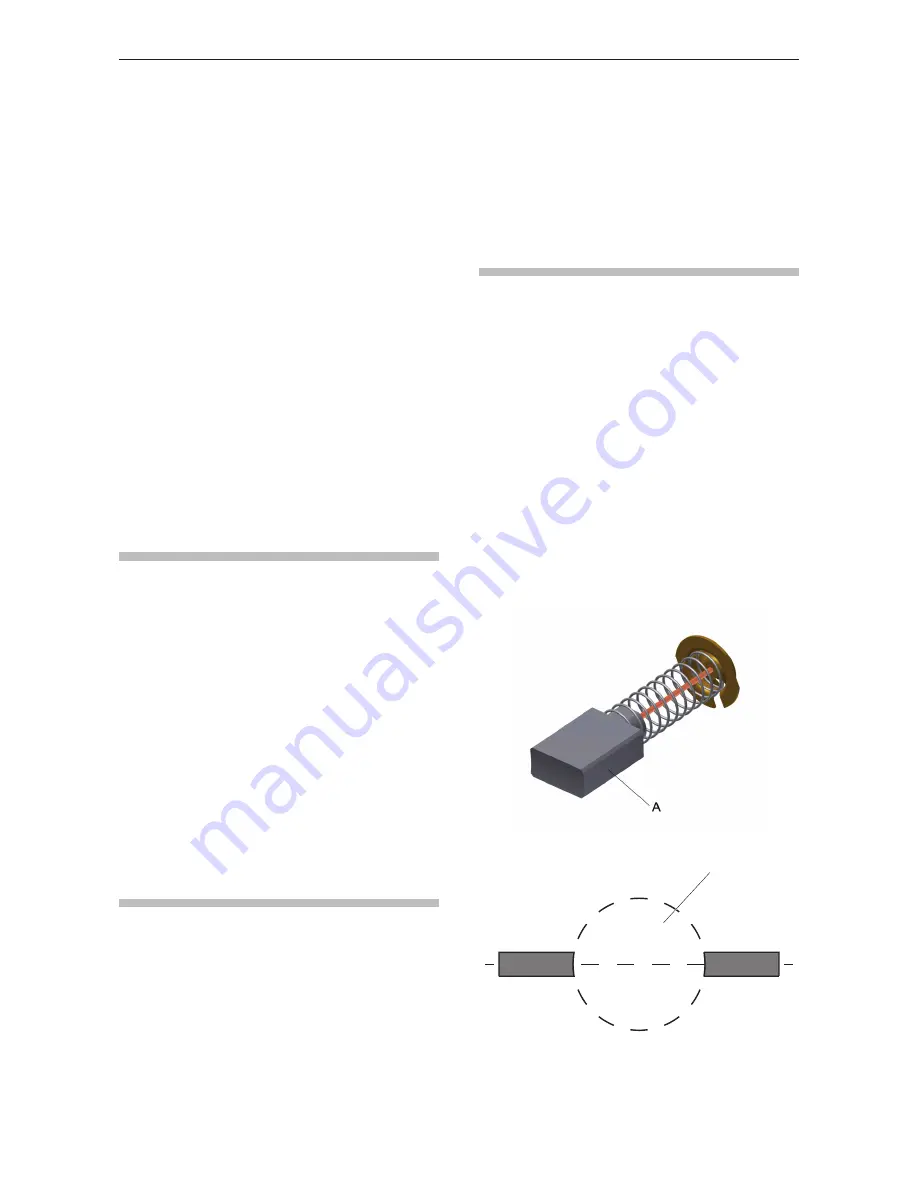
12
© 2015 Construction tools PC AB | No. 9800 1713 0
1
| 2015-04-07
Original instructions
Safety and operating instructions
AME 1600
Maintenance
Regular maintenance is a basic requirement for the
continued safe and ef
fi
cient use of the machine.
Follow the maintenance instructions carefully.
♦
Before starting maintenance on the machine,
remove it from supply and clean it.
♦
Use only authorised parts. Any damage or
malfunction caused by the use of unauthorised
parts is not covered by warranty or product
liability.
♦
When cleaning mechanical parts with solvent,
comply with appropriate health and safety
regulations and ensure there is satisfactory
ventilation.
♦
For major service of the machine, contact the
nearest authorised workshop.
♦
After each service, check that the machine’s
vibration level is normal. If not, contact the
nearest authorised workshop.
Every 10 hours of operation
(daily)
Maintenance routines:
♦
Check and clean the motor’s cooling
fl
anges.
Sand and stones could clog the air inlet and
reduce the cooling of the drive unit.
♦
Clean the machine. After every working shift
concrete splashes must be removed from the
surfaces while it is still fresh.
♦
Check that the controls are not damaged and
do not jam. Replace if necessary.
NOTICE
Never use high-pressure water to clean
the drive unit.
Every 75 hours of operation
(or bi-weekly)
Maintenance routines:
♦
Disconnect the
fl
exible shaft from the drive
unit by lifting the locking mechanism. Unscrew
the shaft from the poker which is a left-handed
thread.
♦
Pull out and lubricate the inner shaft with
KLUBER GBU Y131 grease or equivalent.
About 15 grams of grease is required per meter
of the shaft.
NOTICE
Do not grease the inner shafts too
extensively. Greasing too much can cause
overload of the electric drive unit and trip the circuit
breaker. Run the unit for two minutes continuously
to distribute the grease in the
fl
exible shaft before
immersion in the concrete.
Every 100 hours of operation
(or monthly)
Maintenance routines:
♦
Inspect the carbon brushes on a monthly basis
or every 100 hours. At normal duty the carbon
brushes would last for approximately 150 hours
but premature wear can occur depending on
the working conditions or intensive use.
♦
Inspect the commutator and the carbon
brushes.
♦
Inspect the
fi
lter.
Changing the brushes
♦
The machine is equipped with two carbon
brushes that are placed on each side. The
carbon brushes (A) are machined to ensure a
good contact between the commutator (C) and
the carbon brush.
C