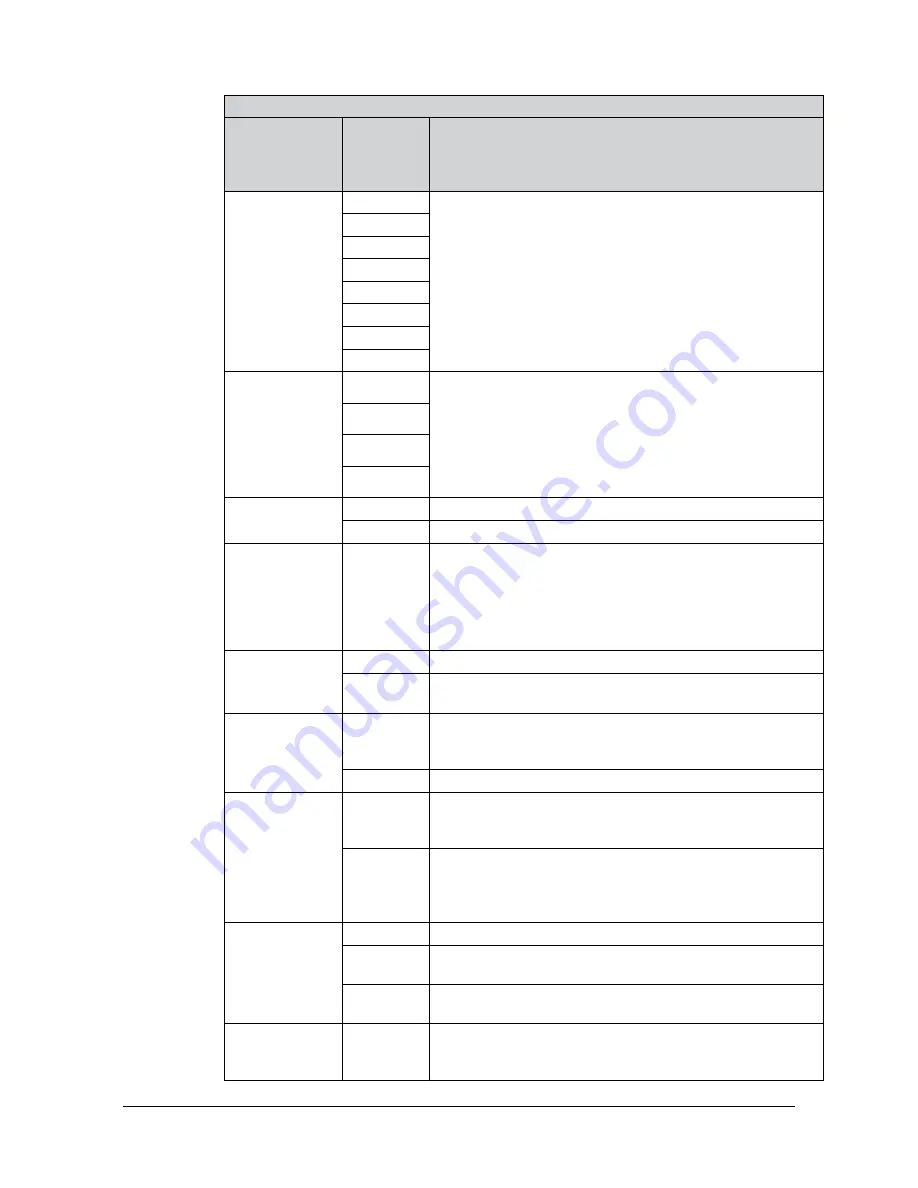
Manual, F/T Sensor, Serial Axia
Document #9610-05-Serial Axia-05
Pinnacle Park • 1031 Goodworth Drive • Apex, NC 27539 • Tel:+1 919.772.0115 • Fax:+1 919.772.8259 •
45
Table 5.1—Secondary “c” or “s” Commands
Category
Secondary
Command
or
Specifier
Notes
Gage
number(s).
0
Gage values are printed in counts only.
As many as all gage numbers can be reported or as few as
a single gage number.
1
2
3
4
5
6
7
Axis.
x
The user can choose to view force and torque data in the x,
y, z axis. The output value can be displayed in F/T counts
or engineering units. Counts are converted to units by
scaling or dividing the count value by the cpf or cpt. Refer to
Section 5.3.1—Converting Counts Per Force/Torque to FT
Values
y
z
m
Force and/or
Torque.
f
The XYZM force data is displayed.
t
The XYZM torque data is displayed.
Magnitude
m
Force or torque data is displayed as the magnitude of the
vector components in the x, y, and z axis. The output value
can be displayed in F/T counts or engineering units. Counts
are converted to units by scaling or dividing the count value
by the cpf or cpt. Refer to
Section 5.3.1—Converting Counts
.
Counts or Units.
c
The XYZM data is displayed in counts.
u
The XYZM data is displayed with the selected user units, for
example: N or Nm. Units are the default setting.
Numeric
System.
h
The data is displayed as a hexadecimal number. Except
any data printed in units is always displayed as a decimal
number by default.
d
The data is displayed as a decimal number.
Format.
>
The data is displayed in a formatted human-readable
output,for example: lined-up columns. “>” is the default
setting.
<
The data is displayed in a compressed output that has no
leading zeros, trailing zeros, or unnecessary blanks. This
output is intended for high-speed applications that are used
in an automated setting.
Additional inputs
to aid in the
development
of a software
program.
s
This command specifies a CRC.
#
This command specifies a sample counter that is
incremented each time that a “c” or “s” line is printed.
@
This command specifies an ADC read counter that is
incremented each time that the ADC is read.
Troubleshooting
!
This command specifies the 32-bit status code. Refer
to
Section 5.3.4—How to Interpret the Output from “!”
.