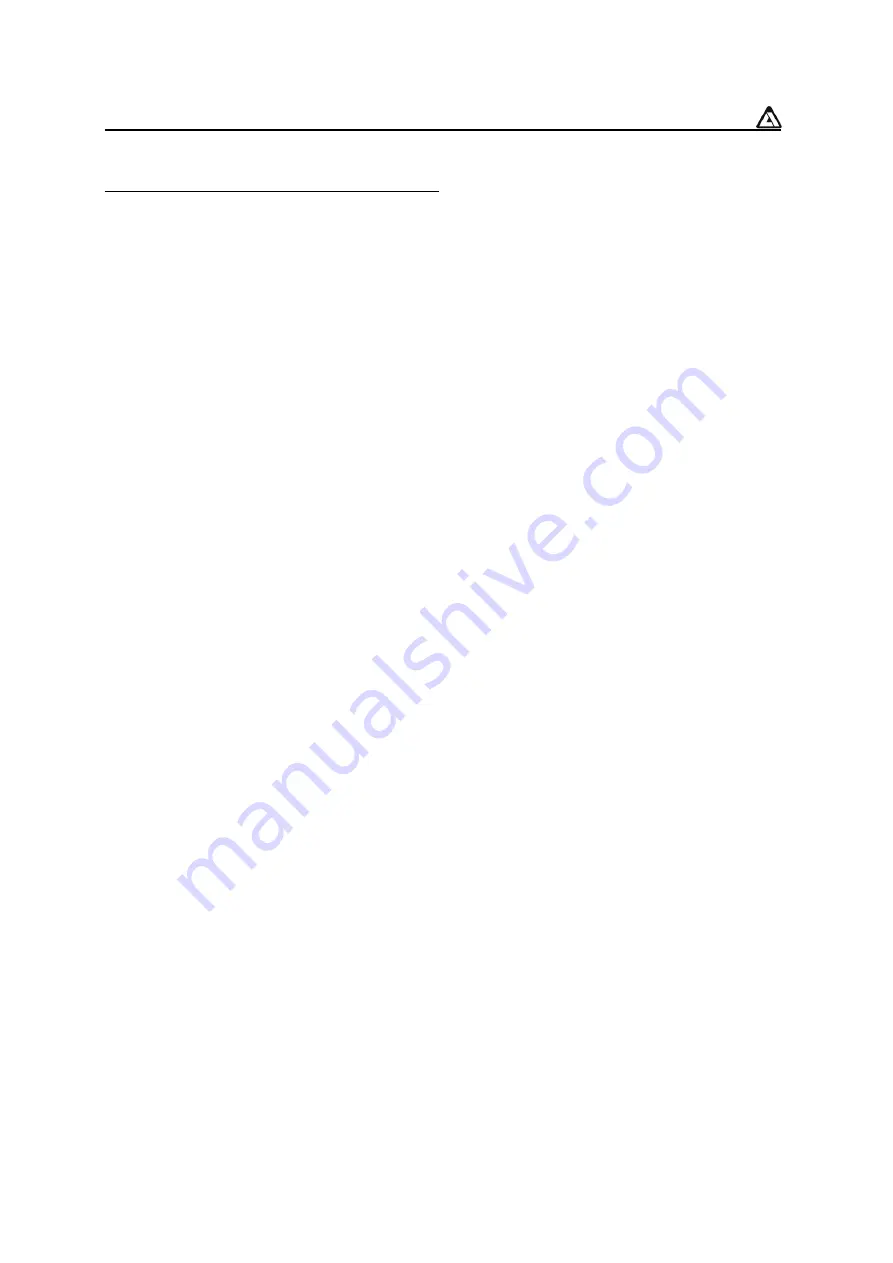
MAINTENANCE
5-3
MECHANICAL REFRIGERATION SYSTEM
PRELIMINARY – As a means of determining the general nature of the difficulty, the following
procedures should be followed prior to using the trouble analysis and service chart.
1.
Check voltage:
a.
With compressor idle
b.
With compressor operating
The voltage must be as follows:
A.
60 cycles – 220 to 230 Volts AC or
B.
50 cycles – 190 to 210 Volts AC or
C.
208 Volts 60 Hz or
D.
110/120 Volts 60 Hz or
E.
95/105 Volts 50 Hz
2.
Disconnect power and allow the unit to stand for one half hour. With chamber empty, close
any ports or openings, wipe out any moisture, and close the door.
3.
Check condenser fin tubes in rear for possible restriction to airflow. Clean with vacuum or
compressed air, if necessary or if water cooled, check water flow to water cooled condenser.
4.
Set dry bulb control point at a temperature below ambient and turn on cool (mechanical
refrigeration) switch. Chamber temperature should pull down to the set temperature and
control at that point.
Be sure to have a minimum of 18” to 24” clearance space at the rear of the chamber. If operation is
not described above, refer to “trouble analysis and service chart” on the next pages.
Содержание SD-302
Страница 3: ......
Страница 7: ......
Страница 11: ......
Страница 27: ...OPERATION 4 12 Sample Profile ...
Страница 31: ......
Страница 32: ...MAINTENANCE 5 1 GENERAL MAINTENANCE TROUBLE ANALYSIS AND SERVICE GUIDE ...
Страница 43: ......