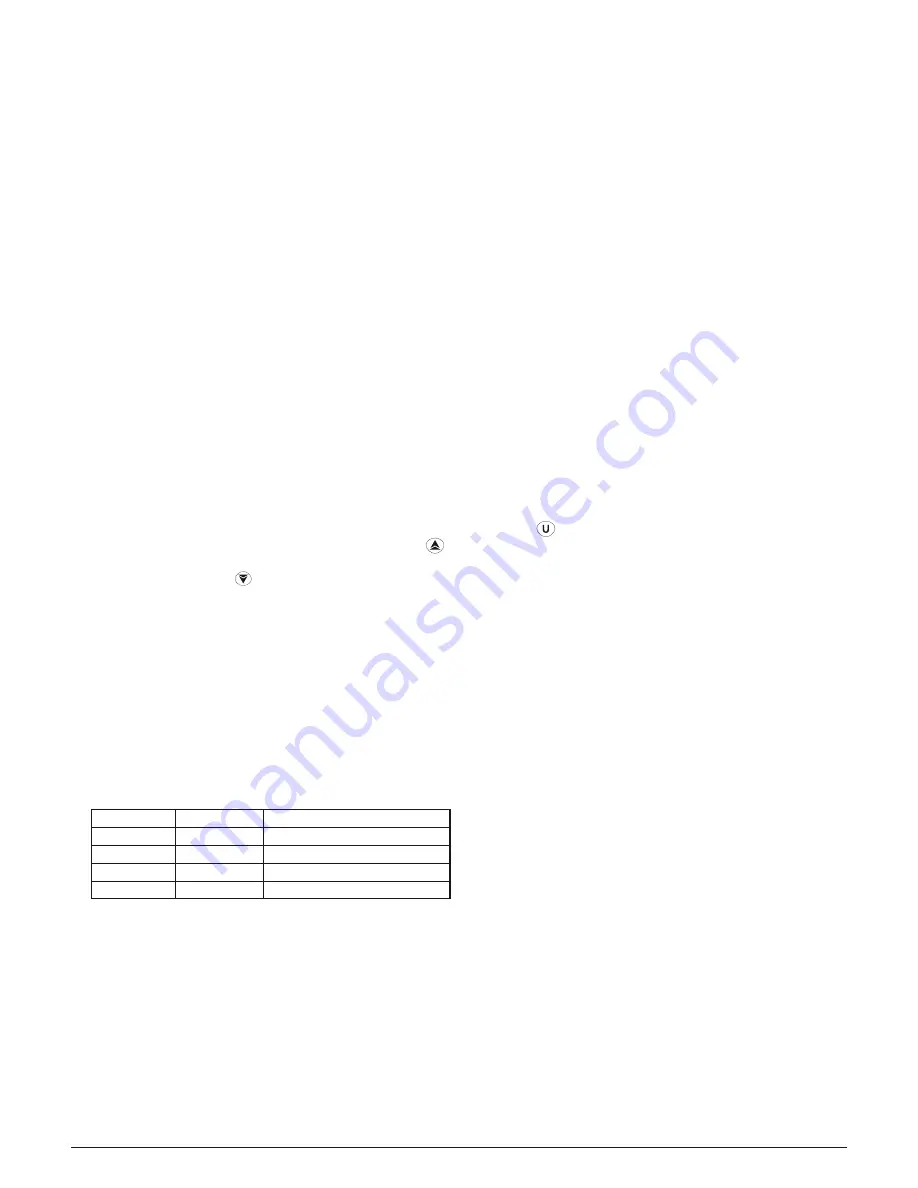
Ascon Tecnologic - K Series - ENGINEERING MANUAL - Vr. 9.0
PAG. 8
7 =
Timer Run [transition] a short closure al-
lows to start timer execution;
8 =
Timer reset [transition] a short closure
allows to reset timer count;
9 =
Timer run/hold [Status].
- Contact closed = timer RUN;
- Contact open = timer Hold,
10 =
Program Run [transition].
The first closure allows to start program
execution but a second closure restart the
program execution from the beginning.
11 =
Program Reset [transition]. A contact clo-
sure allows to reset program execution.
12 =
Program Hold [transition]. The first closure
allows to hold program execution and a
second closure continue program execution.
13 =
Program Run/Hold [status]. When the con-
tact is closed the program is running.
14 =
Program Run/Reset [status].
- Contact closed = Program run;
- Contact open = Program reset;
15 =
Instrument in Manual mode (Open Loop)
[status];
16 =
Sequential set point selection [transition]
(see “Note about digital inputs”);
17 =
SP1/SP2 selection [status];
18 =
Binary selection of the set point made by
digital input 1 (less significant bit) and digi-
tal input 2 (most significant bit) [status];
19 =
Digital input 1 will work in parallel to the
button while digital input 2 will work in paral-
lel to the
button;
20 =
Timer Run/Reset.
Notes about digital inputs:
1.
When
diF1
or
diF2
is equal to 5 the instrument
operates as follows:
•
When the contact is open, the control action is an hea-
ting action and the active set point is SP1.
•
When the contact is closed, the control action is a coo-
ling action and the active set point is SP2.
2.
When
diF1
= 18,
diF2
setting is forced to 18.
diF2
can not be associated with any other function.
3.
When
diF1
=
diF2
= 18 the set point selection will be
in accordance with the following table:
Dig In1
Dig. In2
Operative set point
Off
Off
Set point 1
On
Off
Set point 2
Off
On
Set point 3
On
On
Set point 4
4.
When
diF1
= 19,
diF2
setting is forced to 19.
diF2
can not be associated with any other function.
5.
When a “Sequential set point selection” is used, every
closure of of the logic input increases the value of
SPAT
(active set point) of one step.
The selection is cyclic -> SP1 -> SP2 -> SP3 -> SP4.
]
out Group - Output parameters
[12] o1F - Out 1 function
Available:
Always.
Range:
nonE = Output not used. With this setting, Out 1
status can be driven directly from serial link;
H.rEG = Heating output;
c.rEG = Cooling output;
AL =
Alarm output;
t.out = Timer output;
t.HoF = Timer out - OFF in Hold;
P.End = Program end indicator;
P.HLd = Program hold indicator;
P. uit = Program wait indicator;
P.run = Program run indicator;
P.Et1 = Program Event 1;
P.Et2 = Program Event 2.
or.bo = Out-of-range or burn out indicator;
P.FAL = Power failure indicator;
bo.PF = Out-of-range, burn out and Power Failure
indicator;
diF1 = The output repeates the digital input 1 status;
diF2 = The output repeates the digital input 2 status;
St.By = Stand By status indicator;
on =
Out 1 forced to ON.
Notes: 1.
When two or more outputs are programmed in the
same way, these outputs will be driven in parallel.
2.
The power failure indicator will be reset when the
instrument detects an alarm reset command by
button, digital input or serial link.
3.
When no control output is programmed, all the
relative alarm (when present) will be forced to
nonE
(not used).
[13] o1.AL - Alarms linked up with Out 1
Available:
When [12] o1F = AL.
Range:
0... 31 with the following rule:
+1 =
Alarm 1;
+2 =
Alarm 2;
+4 =
Alarm 3;
+8 =
Loop break alarm;
+16 = Sensor break (burn out).
Example 1:
Setting 3 (2 + 1) the output will be driven by the
alarm 1 and 2 (OR condition).
Example 2:
Setting 13 (8 + 4 + 1) the output will be driven by
alarm 1 + alarm 3 + loop break alarm.
[14] o1Ac - Out 1 action
Available:
When [12] o1F is different from
nonE
.
Range:
dir =
Direct action;
rEU = Reverse action;
dir.r =
Direct action with reversed LED indication;
rEU.r = Reverse action with reversed LED indication.
Notes: 1.
Direct action:
The output repeats the status of
the driven element.
Example:
The output is an alarm output with direct
action. When the alarm is ON, the relay will be
energized (logic output 1).
2.
Reverse action:
The output status is the opposite
of the status of the driven element.
Example:
The output is an alarm output with
reverse action. When the alarm is
OFF
, the relay
will be energized (logic output 1). This setting is
usually named “fail-safe” and it is generally used
in dangerous process in order to generate an
alarm when the instrument power supply goes
OFF or the internal watchdog starts.