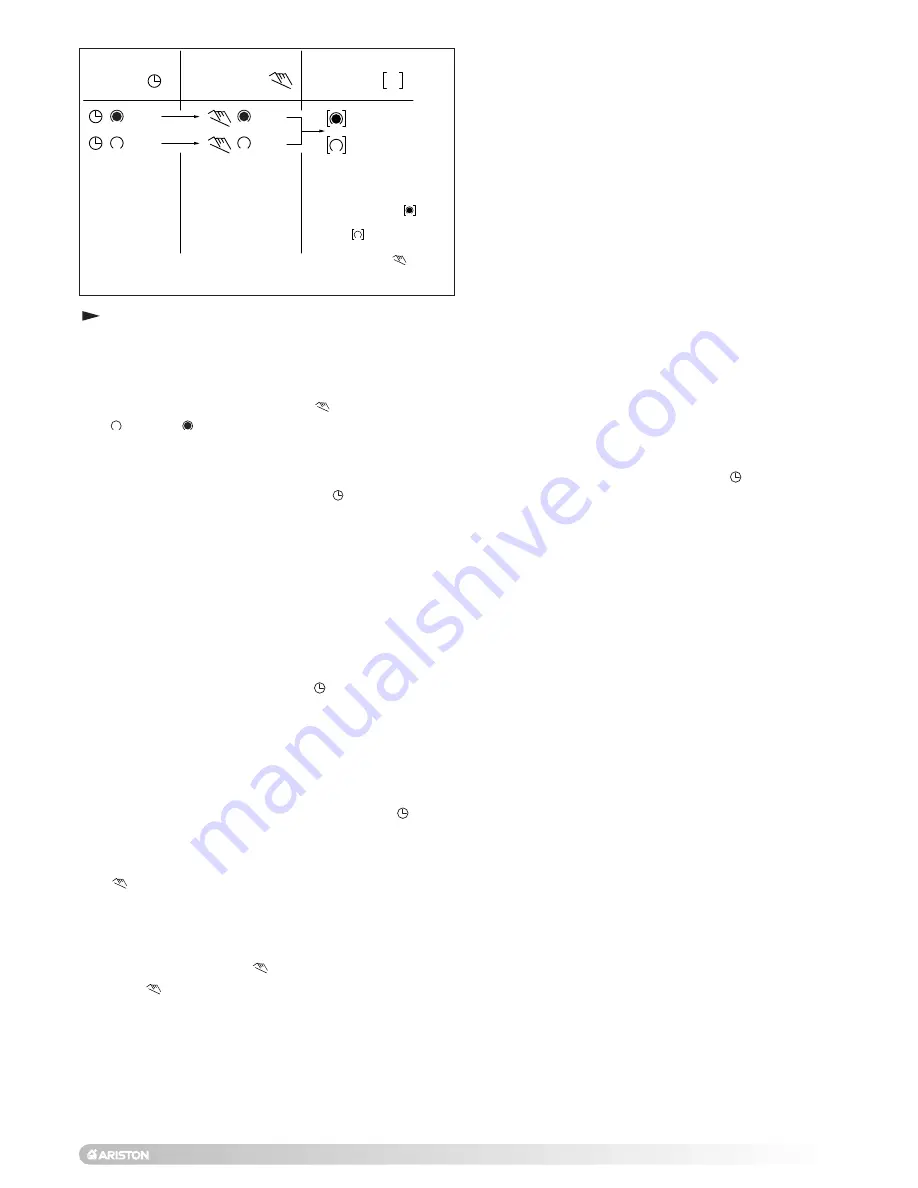
25
Automatic
Manual
Continuous
Operation
Operation
Operation
The switching
If the current
You can only
times corres-
switching mode is
return to automatic
pond to the
changed manually,
mode from the
program
the next switching
continuously-ON
entered.
time will be
and continuously-
carried out auto-
OFF switching
matically again
modes by
according to the
pressing the " "
entered switching
key.
program.
= ON
= ON
= Continuously ON
= OFF
= OFF
= Continuously OFF
Entering the switching times
You have 20 memor y Iocations available. Each
switching time takes up one memory location.
Keep pressing the “Prog” key until a free memory
location is shown in the display “– –:– –”.
Programme ON or OFF with the “
” key:
“
”= OFF; “
”= ON
Enter the hour using “h”
Enter the minutes using “m”
If a switching command is to be carried out every day
(1 2 3 4 5 6 7) then store using the “
” key, otherwise
select the day(s) it is to be carried out by using the
“Day” key.
When the day seIection is left bIank, the programmed
switching instruction operates at the same time every
day
1 2 3 4 5 6 = Monday – Saturday
1 2 3 4 5
= Monday – Friday
6 7
=Saturday – Sunday
Selection of single days: 1 = Mon. .............. 2 =Tues.
Save the switching time with the “
” key.
The time switch enters the automatic operating mode
and displays the current time of day.
Begin any further entry of a switching time with the
“Prog” switch. If your entr y is incomplete, the
segments not yet selected will blink in the display.
After programming is completed, and you return the
time clock to the current time display with the “
” key,
the time clock will not activate any switching
instruction required for the current time. You may need
to manually select the desired switching state with the
“
” key. Thereafter, as the unit encounters further
switching instructions in the memory in real time, it will
correctly activate all subsequent switching
instructions.
Manual Override Switch “
”
With the “
” you can change the current setting at any
time. The switching program already entered is not
altered.
Reading the programmed switching times
Pressing the “Prog” key displays the programmed
switching times until the first free memory location
appears in the display “– – : – –”.
If you now press the “Prog” key once again, the number of
free memory Iocations will be displayed, e.g. “18”. If all
memory locations are occupied, the display “00” appears.
Changing the programmed switching times
Press the “Prog” key repeatedly until the switching time
you want to change is displayed. You can now enter the
new data. See point “Entering the switching times”.
Notes on storing switching times:
If you end your entry of the switching times by pressing
the “Prog” key, then the switching time you have entered
will be stored and the next memory location displayed.
In addition, a complete switching command is stored
automatically after around 90 seconds provided no
other key is pressed. The time switch then enters the
automatic operating mode and displays the current time
again.
Deleting individual switching times
Press the “Prog” key repeatedly until the switching time
you wish to delete is shown in the display. Then set to “–
–” using the “h” or “m” key and keep the “
” key pressed
down for around 3 seconds. The switching time is now
erased and the current time is displayed.
AM / PM time display
If you press the “+/-1h” and “h” keys at the same time, the
time display switches into the AM/PM mode.
Содержание microGENUS HE 24 MFFI
Страница 20: ...20 Fig 2 22 NOTE DRAWINGS ARE INDICATIVE OF FLUEING OPTIONS ONLY TYPE 1 TYPE 5 TYPE 4 TYPE 3 TYPE 2 FIG 2 21...
Страница 68: ...68 10 BENCHMARK COMMISSIONING CHECKLIST...
Страница 69: ...69 11 SERVICE INTERVAL RECORD...
Страница 70: ...70...
Страница 71: ...71...