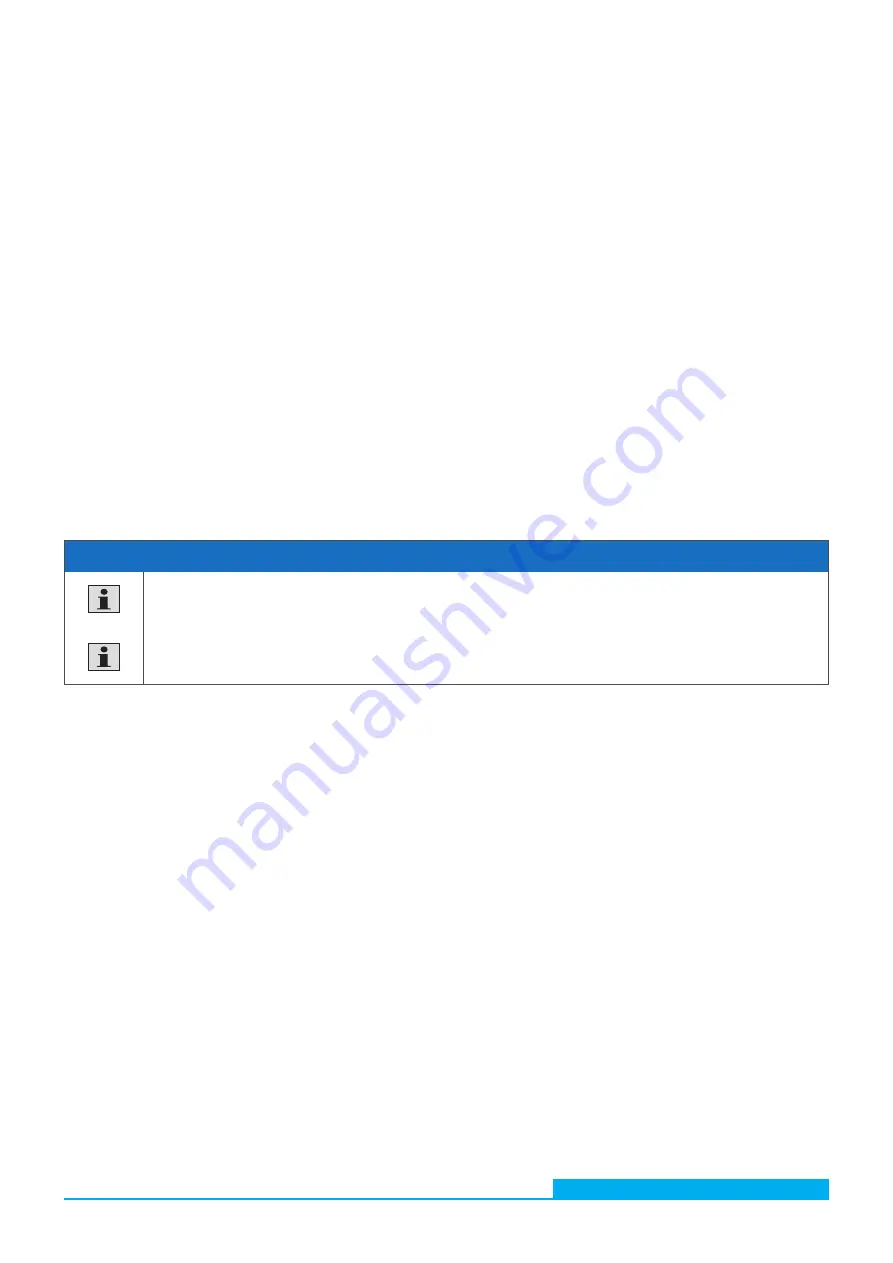
Subject to change · UM 045_14264401
· 0916 · EN
Page 11
www.argo-hytos.com
4.2 Filtering of hydraulic fluids while filling machinery and plant
›
When refilling, make sure that there is no waste oil left in the machine or plant.
›
Connect the filter unit as described under point 2 (with 3 phase motors please observe the rotating direction).
›
Immerse the suction pipe into the oil tank (fresh oil).
›
Immerse the delivery pipe into the hydraulic tank of the machine or plant.
›
Switch rotary valve to position II (filtering).
›
Switch on the filter unit by using the on-off switch.
›
Check the oil flow (the suction pipe may not be immersed to a sufficient depth in the oil tank).
Note: When starting filtration, filling of the filter unit may take a few seconds.
›
Check the element for clogging, using the clogging indicator.
›
Monitor the filling level of the machine or plant and once the desired filling quantity has been reached, switch off the filter unit by
using the on-off switch.
4.3 Pumping of hydraulic fluids (e. g. waste oil, filter is by passed)
›
Connect the filter unit as described under point 2 (with 3-phase motors observe rotating direction).
›
Immerse the suction pipe into the hydraulic tank of the machine or plant.
›
Immerse the delivery pipe into an empty container (oil tank).
›
Switch the rotary valve to position I (pumping) (see illustration 6).
›
Switch on the filter unit by using the on-off switch.
›
Check the oil flow (the suction pipe may not be immersed to a sufficient depth in the oil tank).
Note:
When starting filtration, filling of the filter unit may take a few seconds.
›
Monitor the procedure. As soon as the machine / plant has completely been pumped empty, switch off the unit.
›
With UMP 045:
Monitor the cleanliness and switch off the filter unit as soon as the defined oil cleanliness has been reached.
NOTE
›
The unit must be completely de-aerated.
›
Air bubbles can adulterate the measuring values.
›
The specified media temperatures must be adhered to (see page13).
›
Incorrect viscosities can adulterate the measure values.
›
Connect and fix the filter unit as described under point 2 (with 3 phase motors please observe the rotating direction).
›
Immerse the suction pipe and the delivery pipe into the hydraulic tank of the machine or plant.
Note:
The distance between intake side and delivery side should be kept apart as far as possible to avoid short-circuit of the oil
flow.
›
Switch the rotary valve to position II (filtering), switch off the particle counter.
›
Switch on the filter unit by using the on-off switch. Let the unit operate for 3 to 5 minutes to de-aerate the system.
Then switch off the UMP 045 again.
›
Program the particle counter to the desired oil cleanliness (see user manual PODS).
›
Consider the switching on sequence by all means (disregarding can lead to mal-functioning):
1. Start the counting process by pressing the start-button at the particle counter.
2. Switch on the UMP 045 by using the on-off switch.
3. Make sure that the rotary valve is turned to position II (filtering).
4. Control on the display of the particle counter (counting begins after ca. 3 – 5 sec.).
›
The filter unit UMP 045 automatically turns off once the pre-set cleanliness class has been reached.
4.4 To achieve the maximum cleaning performance
›
The hydraulic or lubricating system should be operated (recirculation of fluid, low viscosity).
›
The distance between intake side and delivery side should be kept apart as far as possible to avoid short-circuit of the oil flow.
›
Adhere to the appropriate filtration time (recommended level: 20 minutes per 100 l tank volume).