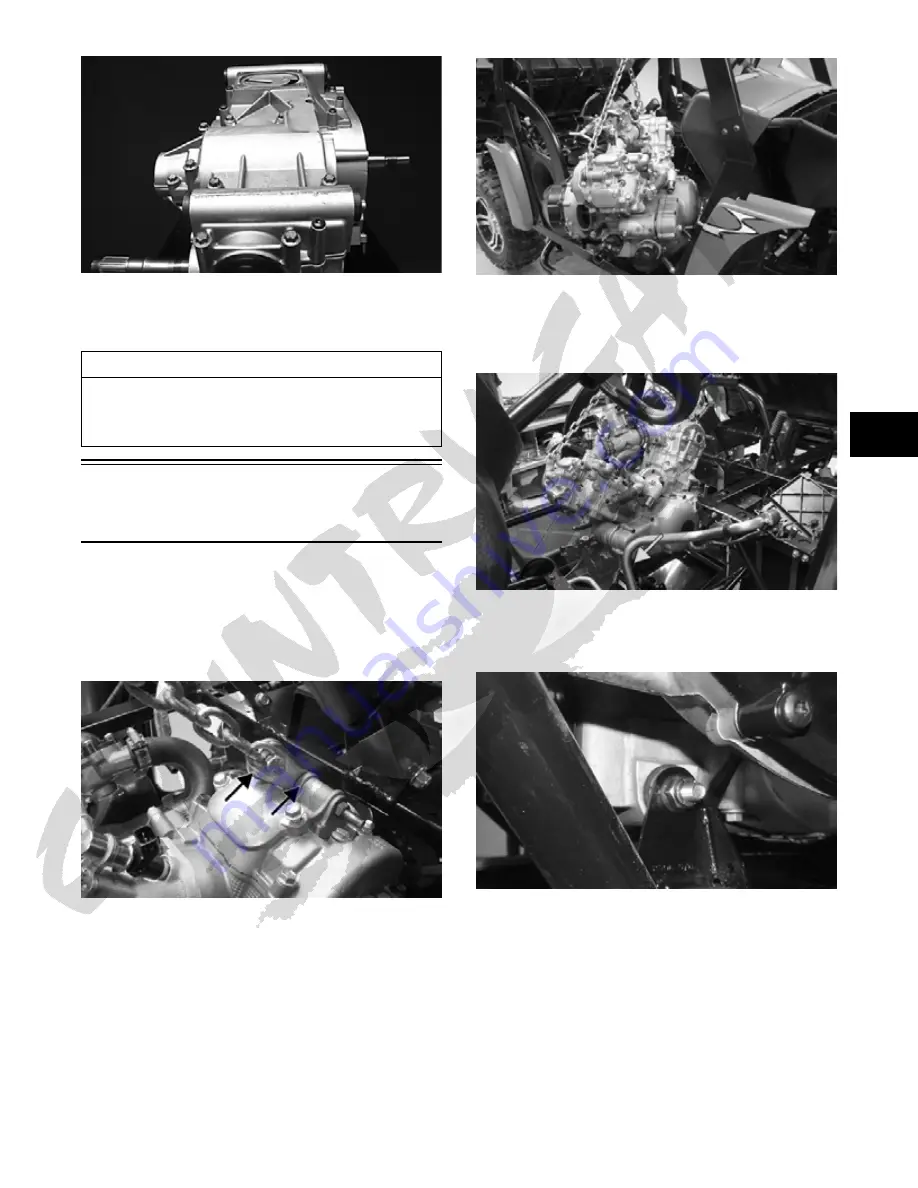
3-101
3
GZ447
10. Install the oil screen; then apply a thin bead of sili-
cone sealant to the oil strainer cap and secure with
the cap screws. Tighten to 8 ft-lb.
Installing
Engine/Transmission
NOTE: Arctic Cat recommends new gaskets and
O-rings be installed whenever servicing the vehicle.
1. Attach a suitable lifting chain to the engine; then
using an engine hoist, lift the engine/transmission
into the vehicle from the right side.
PR632A
PR633
2. Carefully lower the engine/transmission into position
between the engine mounting tabs being careful to
keep all cables, wires, and hoses clear; then install
the longer, front through-bolt with a flat washer.
PR634A
3. Install the rear through-bolts with flat washer; then
secure both with new lock nuts and tighten to 40
ft-lb.
PR629
AT THIS POINT
After completing center crankcase components, pro-
ceed to Installing Right-Side Components, to Installing
Left-Side Components, and to Installing Top-Side Com-
ponents.
Содержание 2013 Prowler XT
Страница 1: ...Prowler XT XTX XTZ ...
Страница 3: ......
Страница 5: ......
Страница 149: ...4 16 NOTES ...
Страница 211: ...7 8 NOTES ...
Страница 232: ...8 21 8 NOTES ...
Страница 233: ... Printed in U S A Trademarks of Arctic Cat Inc Thief River Falls MN 56701 p n 2259 530 ...