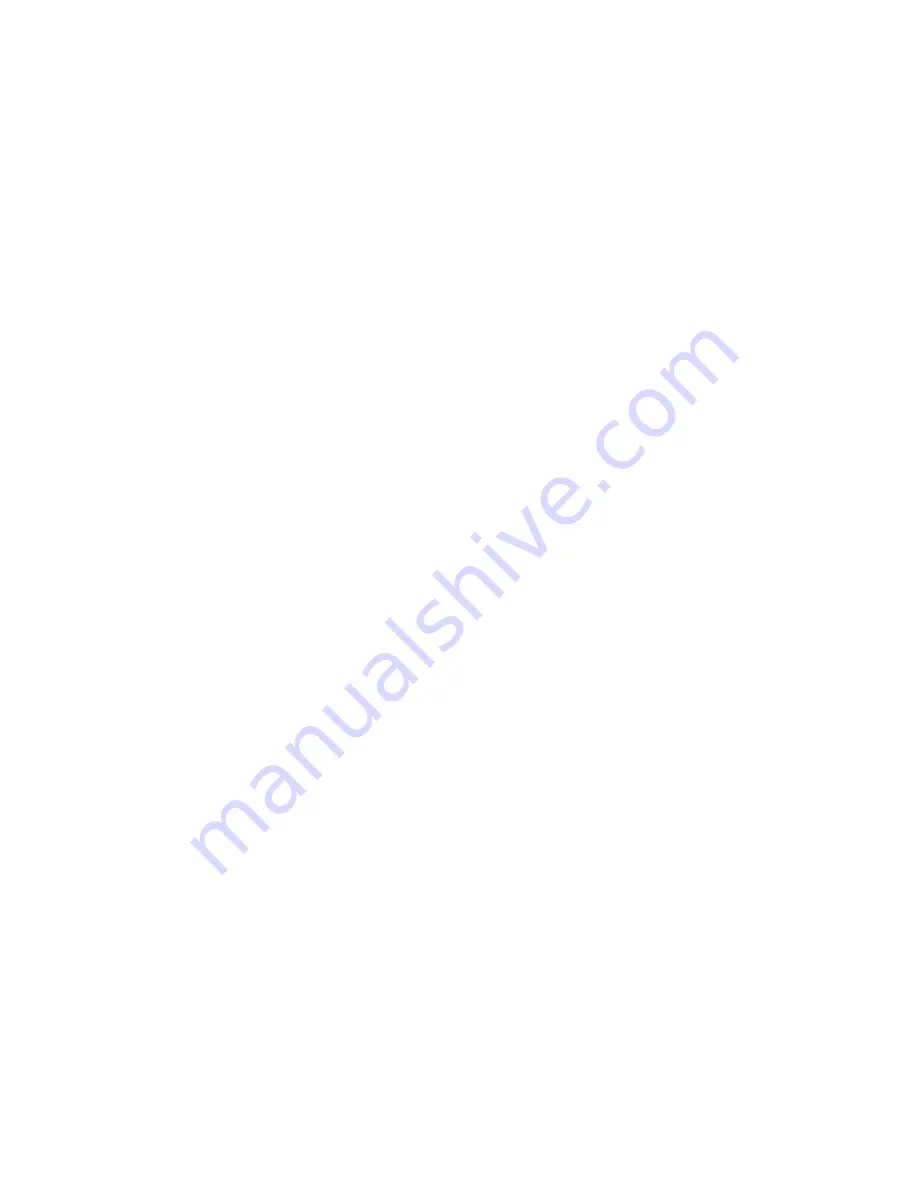
7
4 When working in a confined space always have trained
support personnel nearby.
Welding fumes and gases can displace air and lower the oxygen level causing injury or
death. Be sure the breathing air is safe.
5 Do not weld in locations near degreasing, cleaning, or spraying operations. The heat and
rays of the arcs can react with vapors to form highly toxic and irritating gases.
6 Do not weld on coated metals, such as galvanized, lead, or cadmium plated steel. The
coating must be removed from the area to be welded. Coatings and metals containing
above elements can generate toxic fumes
when heated to welding temperature
.
1.4 WELDING SPARKS
Heat from flames and arcs can start fires. Hot slag or sparks can also cause fires and
explosions.
1. Remove all combustible materials from the work area or cover these materials with a
protective non-flammable tarp. Combustible materials include wood, fabrics, sawdust,
liquid and gas fuels, solvents, paints and coatings, paper, etc.
2. Hot sparks or hot metal can fall through cracks or crevices in floors or wall openings and
cause a hidden smoldering fire. Make certain that such openings are protected from hot
sparks and metal.
3. Do not weld, cut or perform other hot work until the work piece has been completely
cleaned so that there are no substances on the work piece, which might produce
flammable or toxic vapors. Do not weld on closed containers. They may explode.
4. Have fire-extinguishing equipment handy for instant use.
5. Do not use equipment beyond its ratings. For example, overloaded welding cable can
overheat and create a fire hazard.
6. After the welding is completed, inspect the work area to make certain there are no hot
sparks or hot metal, which could cause a fire. Use fire watches when necessary.
7.
For additional information, refer to NFPA Standard 51B, “Fire Prevention in Use of
Cutting and Welding Processes”, available from the National Fire Protection Association.
1.5 ELECTRIC AND MAGNETIC FIELDS
Electric current flowing through any conductor causes localized Electro-Magnetic Fields (EMF).
Welding and cutting current creates EMF around welding cables and welding machines.
1. Operators having pacemakers should consult their physician before welding. EMF may
interfere with some type of pacemakers.
2. Exposure to EMF may have other health effects, which are unknown.
3.
Operators should use the following procedures to minimize exposure to EMF:
a. Route the work cables together. Secure them with electrical tape when possible.
b. Never coil the work cable around any part of your body.
c. Do not place your body between the work cables. Route cables on the same side
of your body.
d. Connect the work cable to the work piece as close as possible to the area being
welded.
e. Keep welding power source and cables as far away from your body as possible.
Содержание IRONHORSE 300S
Страница 18: ...5 3 Main Circuit Diagram ...
Страница 19: ...5 4 Front Panel 19 ...
Страница 20: ...5 5 Rear Panel 20 ...
Страница 21: ...5 6 1 Bottom Chassis Drawing with Part Number Reference ...
Страница 22: ...5 6 2 Top Chassis Drawing with Part Number Reference 22 ...
Страница 23: ...5 6 3 Inductor Plate Drawing with Part Number Reference 23 ...