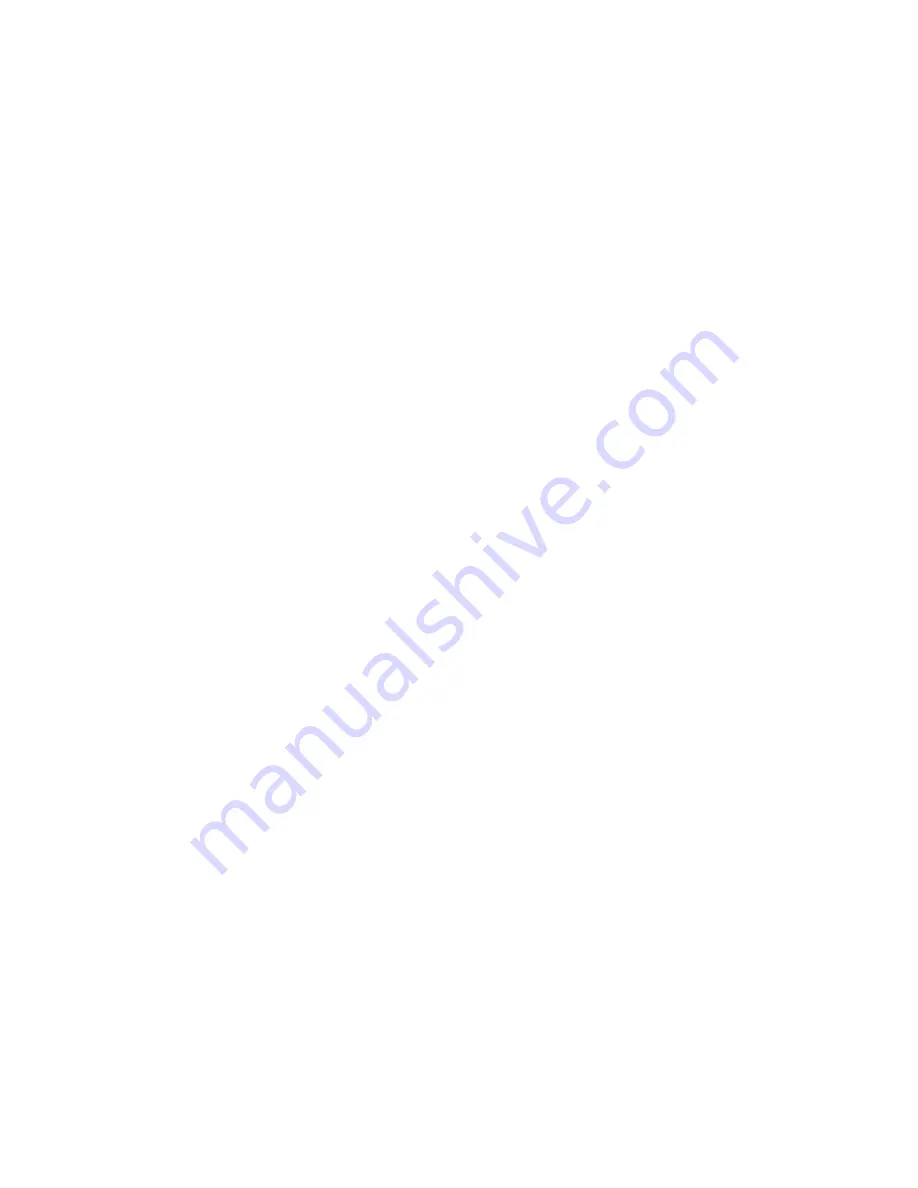
– 29 –
After the burner has been in operation for at least 10
minutes, this allows the combustion chamber and
heat exchanger to reach an equilibrium temperature;
a fl ue gas analysis can now be performed. There is
a test plug in the stand off box where the induced
draft fan airfl ow switch tube is located.
The following readings should be taken but not limited
to:
CO
2
%
Net
Stack
Temperature
O
2
%
Combustion
Effi
ciency
CO %
If necessary, make adjustments on burner air shutter.
DO NOT
change the fuel input rate.
The following list covers general combustion problems
and some of the possible cures. Conditions may vary in
the fi eld. Refer to combustion chart for effi ciency.
CAUTION: Check local codes for maximum
allowable percentages and amounts of emissions.
Low Carbon Dioxide (CO
2
)
•
Fuel input too low
•
Excess burner air
•
Wrong draft setting
Detectable Carbon Monoxide (CO)
•
Fuel input too high
•
Not enough burner air
• Restricted
draft
• Flame
impingement
Excessive Stack Temperature (480°F Above Ambient)
•
Draft setting too high
•
Excess burner air
•
Fuel input too high
•
Blocked and/or restricted secondary tubes
Low Oxygen (O
2
)
• Oxygen reading must always be a positive
percentage
Make sure there is a minimum of –0.02" W.C. at relief
door when burner is in high fi re with a warm stack.
Cycle burner several times to ensure smooth light
off and proper operation. Visually observe the fl ame
pattern. There must be no fl ame impingement or hot
spots on the combustion chamber that could cause
scaling.
Check voltage and amperage on all motors.
Check all dampers, linkages, and locking quadrants to
make sure they are secure and operating correctly.
Check all gas piping for leaks.
FINAL CHECKS AND ADJUSTMENTS
Flame Safeguard
– Close the last manual gas valve
before burner. Operate unit in heat mode. After pilot
fl ame has been established, quickly close manual
pilot gas valve. The fl ame safeguard must trip out in
approximately 15 seconds.
Gas Pressure Switches
– The low gas pressure switch
will trip out and must be reset before resuming operation
when the inlet gas shut off valve is turned off, or inlet
gas pressure is lower than the trip point. The high gas
pressure switch can be checked by reducing the setting
of its trip point lower than the burner operating pressure.
The switch should trip out and shut off the burner.
Return the adjustment to its original setting and reset to
resume operation.
Temperature Controls
– The temperature controls are
checked by adjusting control to a higher temperature
to allow burner to cycle on. Adjust control to a lower
temperature to allow burner to cycle off. Return the
adjustment to its original setting.
Air Pressure Switches
– The air pressure switches
can be checked by turning the adjusting screw to call for
a higher pressure than is normally used on the system.
Recycle is automatic when the switch returned to its
original setting. If the burner or draft proving switches
open, this could cause the fl ame safeguard to go into
standby mode.
Limit Controls
– The limit controls are checked by
adjusting control to a lower temperature setting while
the unit is operating on high fi re and observe cut-off.
Return the adjustment to its original setting. Manual
reset may be required on some controls.
Make sure all the safeties and controls
are working properly.
SAFETY AND CONTROLS CHECKOUT
Содержание GAS-FIRED HEATERS
Страница 6: ... 6 ...
Страница 7: ... 7 ...
Страница 8: ... 8 ...
Страница 9: ... 9 ...
Страница 13: ... 13 ...
Страница 24: ... 24 TYPICAL SEQUENCE FOR MODULATING THERMOSTAT WITH 135 OHM CONTROLS ...
Страница 25: ... 25 TYPICAL SEQUENCE FOR MODULATING THERMOSTAT WITH 4 20 mA CONTROLS ...
Страница 64: ...4830 Transport Drive Dallas TX 75247 Phone 214 638 6010 Fax 214 905 0806 www appliedair com ...