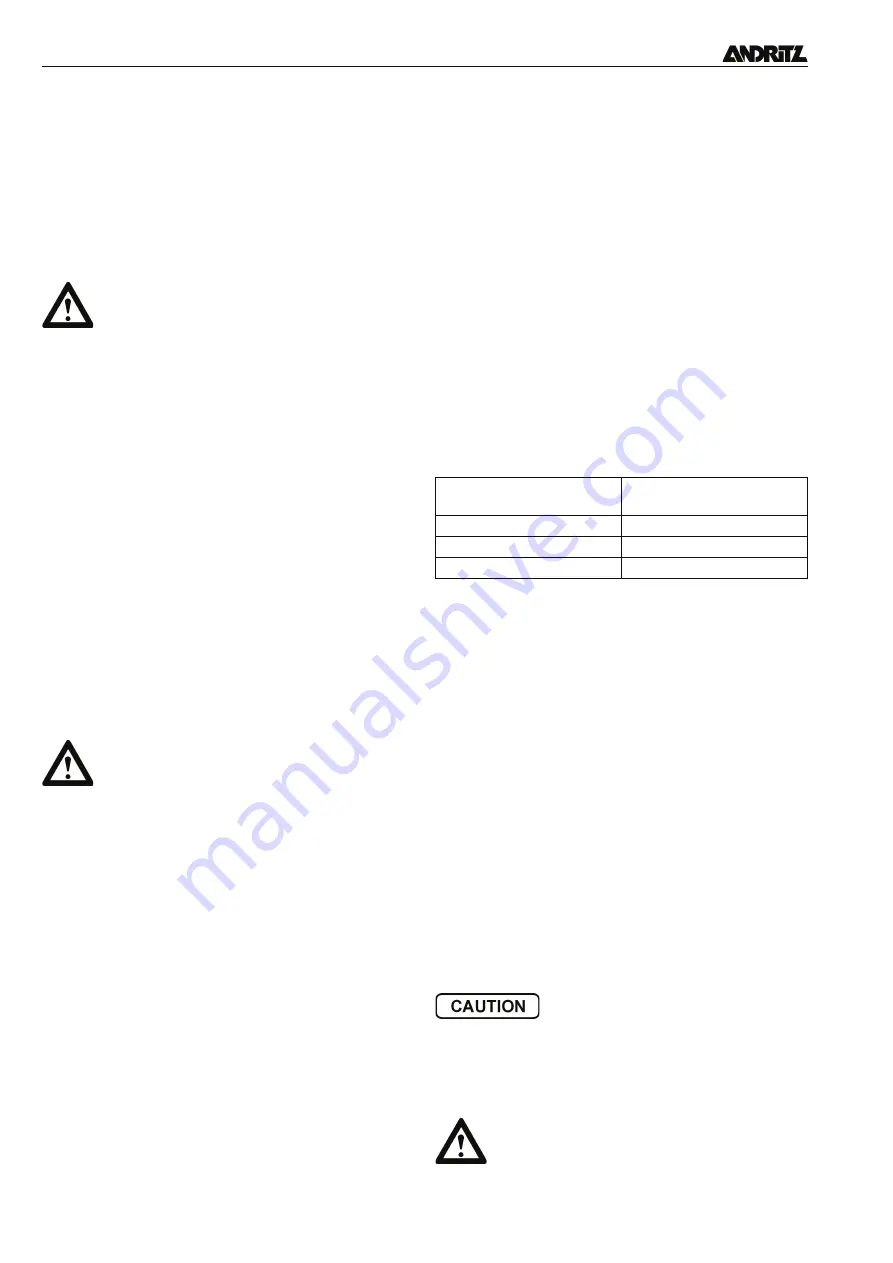
Series SD 35
24
• Check the operating data at all operating states possible in
the system (parallel operation of pumps, other delivery pur-
poses, etc.)
• Record readings for future reference.
• Check the bearing temperature. A temperature of 50°C above
the ambient temperature is acceptable.
4.3.3
Closed valve operation
4.4
Shut-down
4.4.1
Switching off
• Close the isolating valve in the discharge pipe.
• Switch off the pump.
• A non-return valve above which a corresponding pressure is
built by the liquid column makes the actuation of a discharge
side valve unnecessary.
• Close the additional valves.
4.4.2
Draining
• If frost is anticipated, drain any pumps or pipework not in use,
or take other precautions to prevent damage from frost.
• After pumping polluted media and to prevent corrosion when
not in use the pumps should be drained and, if necessary,
flushed.
5. Maintenance/servicing
5.1
Safety Notices
5.2
Maintenance and inspection
5.2.1
Lubricants, oil capacities and lubricating intervals
5.2.1.1
Pump with lubricated bearings greased for life
(standard execution)
The pumps are fitted with lubricated bearings greased for life in
the factory before delivery and this should last for approx.
15,000 working hours or two years. Under unfavourable work-
ing conditions such as a hot climate, dampness or overheating,
the bearings need to be checked and changed before this peri-
od.
5.2.1.2
Pump with grease lubricated bearings for
regreasing with grease nipples (special
execution)
The bearings are filled with grease in the factory before delivery
• Need to be re-greased with approx. 20 to 30 g per point every
six months.
•
Grade of grease:
Lithium-based grease according to DIN
51825, non-ageing, non-acidic, non-corroding, water-resist-
ant with a working temperature of -30 to +130°C, penetration
rate of 2 to 3, working penetration of 265 to 295 and a dripping
temperature of approx. 190°C.
• Recommended commercially-available grades of grease:
-UNIREX N2, (ESSO)
-OPTIMOL OLISTA LONGTIME or OLIT 2, (OPTIMOL)
-GLISSANTO 20, (DEA)
-ENERGREASE MSLS-EP2, (BP)
• Avoid over-greasing as this can lead to damages caused by
overheating.
• After regreasing several times or if overheating occurs (50°C
above ambient) open the bearing cover and remove surplus
or used grease.
• Do not pack new bearings more than half full with clean
grease.
5.2.2
Monitoring the pump during operation
For satisfactory operation carry out the following checks as rou-
tine:
• Monitor the smooth running of the pump. In case of unusual
strong vibrations immediately switch off the unit and check for
reason (impeller damage, foreign matters, clogging, etc.)
•
For pumps with gland packing rings
confirm the leakage
rate of the shaft seal as 5 to 10 l/hr. If gland sealing water is
supplied check the flow rate.
•
Pumps with mechanical seals:
If leakage occurs at shaft
clean, inspect and if necessary replace the mechanical seal.
A leakage of between 0.2 and 5 ml/h is possible depending
on running smoothness, pressure, rotational speed and shaft
diameter (mechanical seals are wearing parts for which no
guarantee can be given).
•
V-Belt driven pumps:
Check belt tension.
• Regularely check local readings, the best each working day,
and immediately react to any large deviations.
• At regular intervals, the best once a week, check all meas-
ured and recorded operating values and note down in a unit
casebook. Determine the maintenance interval on the basis
of the trend (data development).
•
Pressure gauge with three way cock:
Only open the three-
way cock in order to obtain a gauge reading and close it im-
mediately afterwards.
•
If pumping highly corrosive and/or abrasive media,
the
components containing pressure should be inspected regu-
larly to avoid unexpected failure. The interval between in-
spections should be short initially and may be extended as
experience is gained.
5.3
Disassembly and assembly instructions
Stripping and assembly should only be carried out by qual-
ified personnel and with reference to the relevant sectional
drawings (see para. 7.4). The stripping sequence will be
clear from the drawing.
Never run the pump with the suction and discharge
isolating valves closed or with the discharge valve
closed at non-return valve installed at suction side.
Under such conditions the pump contents will be
rapidly vaporised and very high pressures generat-
ed. These may exceed the bursting pressure of the
pump casing, creating a serious hazard to personnel
and property.
• Never work on the set until the electricity supply
has been disconnected completely. It must be im-
possible for the set to be started inadvertently.
• Always wear safety gloves when assembling/strip-
ping the pumps or when adjusting glands.
Nominal diameter
discharge branch
Sealing water required
[m³/h] at
Δ
p 0,5 bar
100
0.15
125 - 200
0.20
250
0.25
Table 2: Sealing water required
•
When disassembling the impeller:
The pump
casing remains connected to the pipework.
•
When disassembling the pump casing:
secure
the pump casing and pipework against falling
down.
Содержание SD 35 Series
Страница 15: ...Baureihe SD 35 16 F r Ihre Notizen...
Страница 29: ...Series SD 35 30 For your notes...
Страница 43: ...S rie SD 35 44 Pour vos notes...
Страница 44: ...S rie SD 35 45 FRAN AIS Pour vos notes...
Страница 45: ...S rie SD 35 46 Pour vos notes...