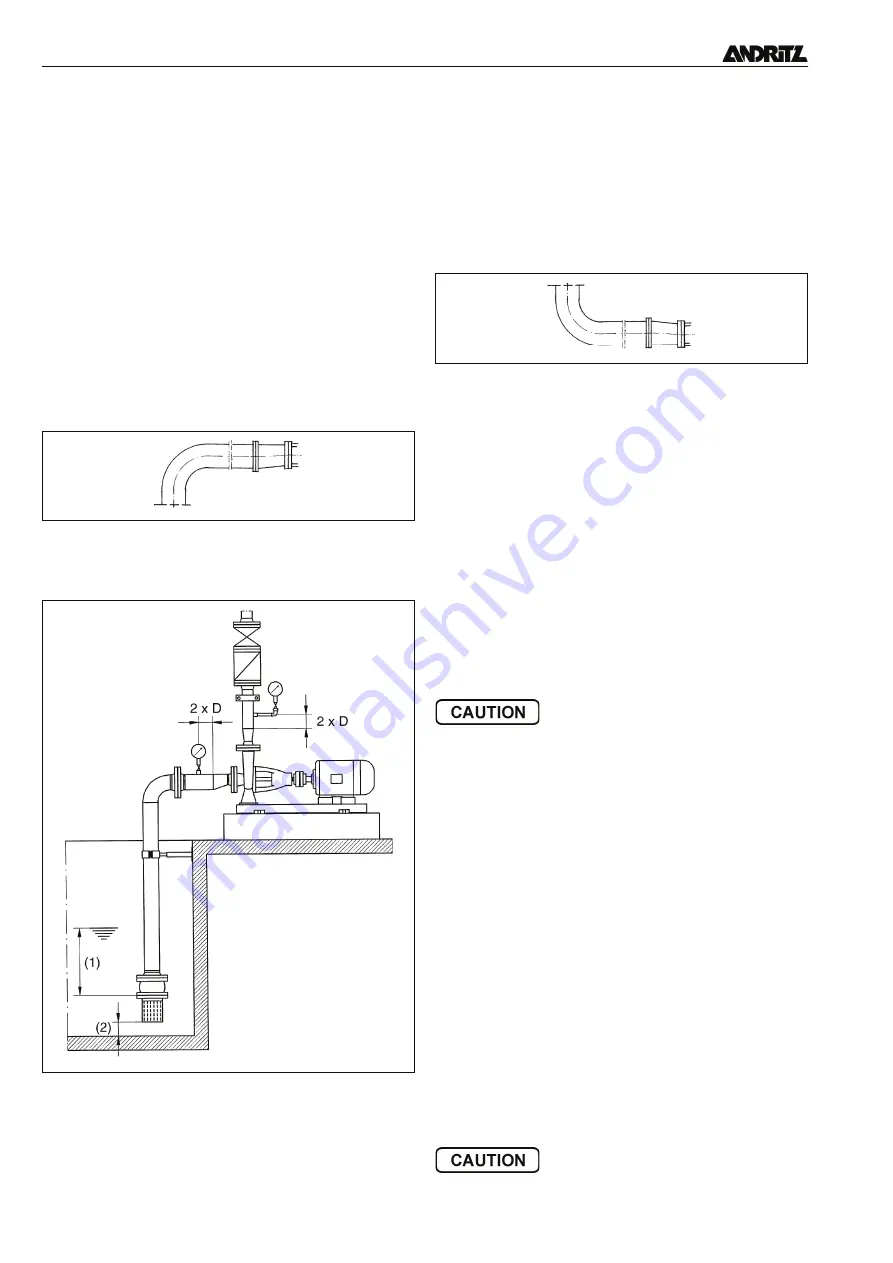
Series SD 35
22
3.4
Piping
Non-binding suggestions for proper design and installation of
the pipework (the exact design of the pipework must remain the
responsibility of the project manager!).
3.4.1
General
• Provide support for the piping on both sides of the pump and
attach it unstressed onto the pump. Please observe the max.
permissible branch loads (refer to para. 7.2).
• After the piping has been connected, check the running of the
pump and alignment of coupling.
• Use bellow expansion joints with linear reducers.
• Alterations in the length of the piping caused by harsh tem-
peratures and other strains can be prevented by the use of
anchorages on both sides of the pump.
• The pipework should be short and direct and changes of di-
rection should be avoided where possible.
3.4.2
Suction Pipe
• The maximum flow rate is 2 m/s (at max. permissible capaci-
ty).
• Do not fit a row of quarter bends on different levels.
• The pipe should be laid at an inclined angle to the pump (at
least 1 %).
• The pipework must be completely vented and sealed.
• Provide a separate suction pipe for each pump.
• When operating the pump in suction mode without a foot
valve, provide a vacuum installation.
• Ensure that no gas can accumulate in the suction pipe.
• Minimum submergence (1):
Hm = v²/2g+0.1
Hm = minimum submergence
v
= flow rate when pumping maximum capacity
g
= local gravitational constant = 9.81 m/s²
• The distance from the floor of the container (2) must be at
least half the diameter of the pipe.
3.4.3
Inlet pipe
• Should be laid as the suction pipe but with the pipe at an an-
gle sloping away from the pump (at least 1 %).
• Fit a return flow stop before the pump.
3.4.4
Discharge pipe
• Lay piping at an angle sloping upwards.
• Maximum flow rate 3 m/s (note the fall in meters).
• Ensure that the piping is free of tight spots.
• The pipes must be laid so that the danger of solids blocking
other pumps is avoided.
• Flange and piping must be designed in accordance with the
maximum pressure.
• Avoid gas accumulation and vent high points if necessary.
• Differing pipe diameters cause variations in flow rate and
therefore need to be avoided.
• Install a sluice valve and return flow stop.
3.4.5
Pressure tests
• Observe the relevant directives.
• Adhere to permitted nominal pressure levels for individual
components.
• Consider the overlapping of pump pressures at pumps in-
stalled in series.
3.4.6
Auxiliary pipe connections
Sealing and flushing media:
• Connect the pipes.
• Install a regulating valve and a magnet valve (closed without
current).
• Blocking and flushing pressure must be at least 0.5 bar above
the maximum pressure of the pump.
• Set the amounts of blocking and flushing media with the reg-
ulating valve.
Quench media:
• Discharge media without pressure into the quench chamber.
• When using pumps which are fitted with a dual-action me-
chanical seal in tandem arrangement then fit the quench con-
tainer approx. 1.5 m above the mechanical seal.
4. Commissioning / shut down
4.1
Commissioning
Before switching on the pump ensure that the following points
have been checked and carried out:
suction pipe
Instructions for laying the suction branch
inlet pipe
Содержание SD 35 Series
Страница 15: ...Baureihe SD 35 16 F r Ihre Notizen...
Страница 29: ...Series SD 35 30 For your notes...
Страница 43: ...S rie SD 35 44 Pour vos notes...
Страница 44: ...S rie SD 35 45 FRAN AIS Pour vos notes...
Страница 45: ...S rie SD 35 46 Pour vos notes...