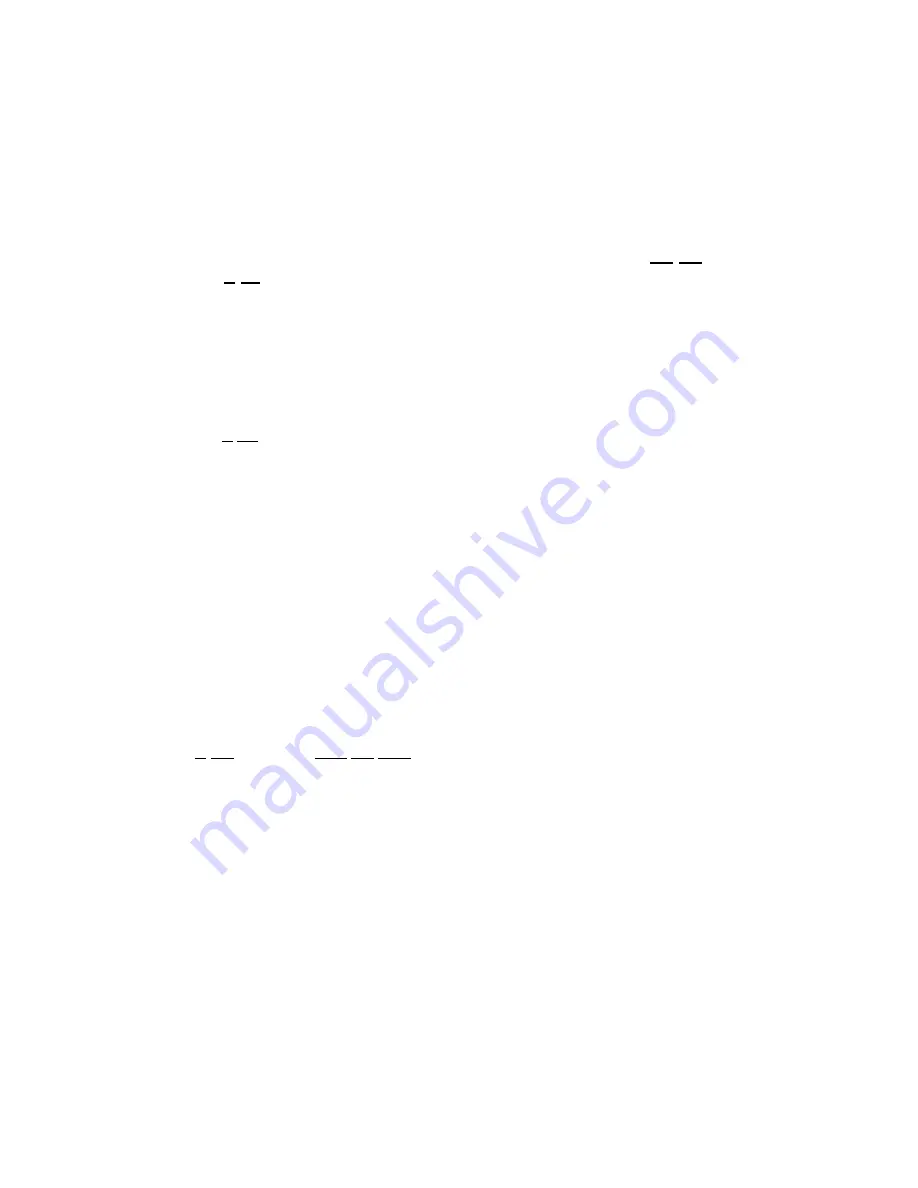
64
7. V-belts too tight or too loose.
8. Tumbler bearing set screws are loose.
9. Failed motor bearing.
TIMER MODELS
A
. Dryer will not start...both drive motor and blower (impellor/fan) motor are
not operating and
indicator light
is
off
...
1. Service panel fuse blown or tripped breaker.
2. Dryer control circuit L1 or L2 1/2-amp (Slo Blo) fuse is blown.
3. Open in main door switch ...
a. Main door is not closed all the way.
b. Main door switch is out of proper adjustment.
c. Failed main door switch.
d. Broken connection/wire somewhere in the main door switch circuit.
4. Failed push-to-start relay.
5. Failed 24 VAC step down transformer or a fault in the wiring.
6. Failed heat timer.
7. Failed control step down transformer
(for 380 volts or higher models ONLY)
.
B. Drive motor is
not operating (does
not
start)...
1. Failed drive motor contactor (relay).
2. Failed reversing timer
(for Reversing Models ONLY)
.
3. Failed drive motor.
C. Drive motor
(Reversing Models ONLY)
operates in one direction only...stops and restarts in the
same direction...
1. Failed reversing contactor (relay).
2. Failed reversing timer.
Содержание Gas/Electric/Steam AD-75HS
Страница 21: ...17 ...
Страница 76: ...ADC113039 1 09 01 98 253 ...