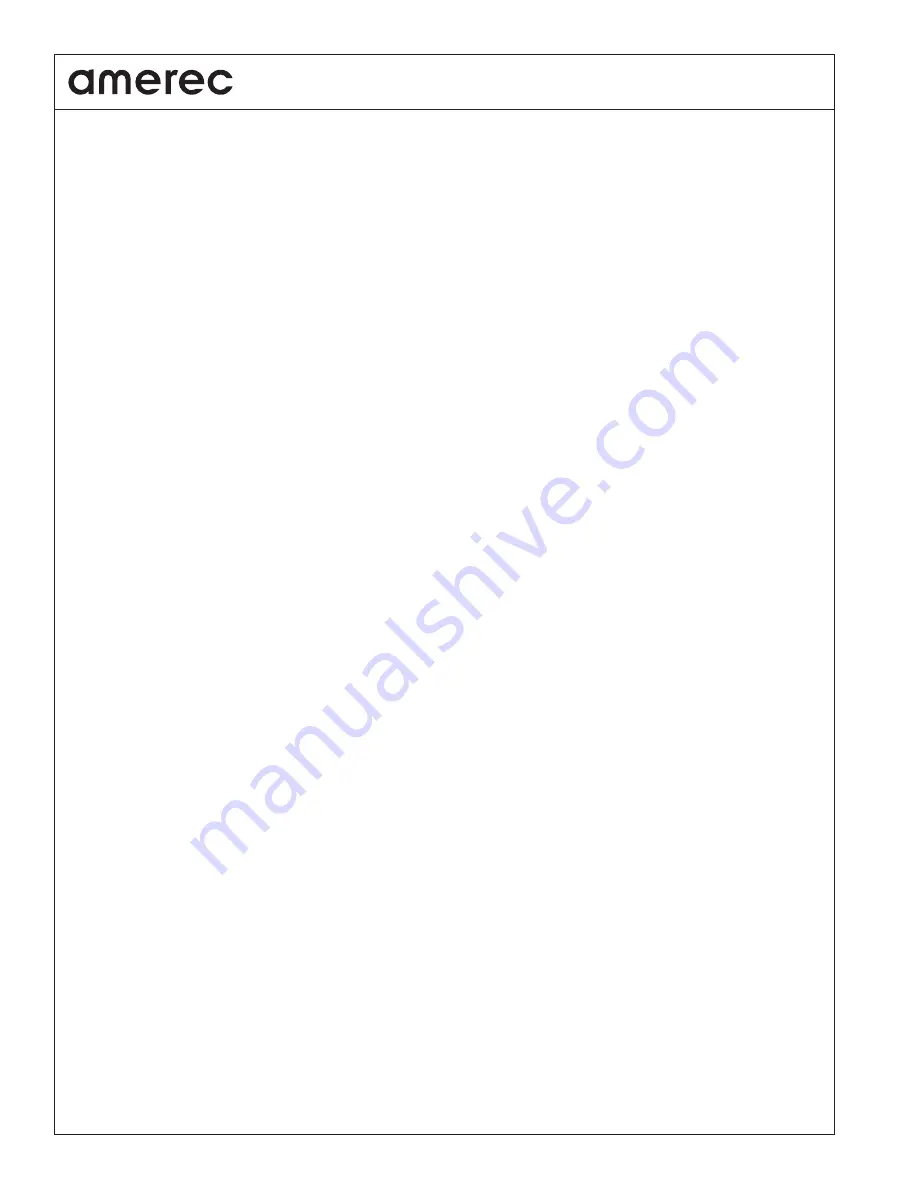
4211-195 05-22-12
Page 6
AI
SERIES STEAM BOILER WITH T100 CONTROL
INSTALLATION INSTRUCTIONS
GENERAL INFORMATION
: The AI Commercial Steam Boiler is a low pressure boiler, UL/CUL Listed, built to NEC requirements and us-
ing an ASME certi
fi
ed H stamped pressure vessel.
The boiler has all steel construction with powder coated
fi
nish on visible surfaces and stainless steel mounting feet to minimize the risk
of corrosion. The mounting feet hold the boiler one inch (25 mm)above the
fl
oor to allow cleaning the
fl
oor below it and to further prevent
corrosion. This also allows the boiler to sit directly on a combustible surface without additional protection. The feet extend beyond the
sides of the boiler chassis and have clearance holes to allow securing the boiler in place using ¼” (6.4 mm) bolts.
AI Commercial Steam Boilers are factory assembled and tested and ready to install. All boilers are plumbed for a ½” potable water feed
inlet, a ¾” drain discharge and a ¾” pressure relief valve discharge. Boilers are available for connection to 208VAC or 240VAC single or
three phase, or 415V~ or 480VAC in three phase only. All models require the appropriate full power electrical service plus ground. Models
in 208V, 240V and 415V also require a 14 gage minimum Neutral for the control circuit and 480V models require a separate N
service for the control circuit. Use 75° minimum copper wire for all service connections. A ¾”-1”-1½”-2” combination knockout is provided
in the boiler’s electrical box for the main service conduit and an additional ½”-¾” knockout is provided for the control service if needed.
The boiler’s control circuit is protected by a 250VAC 3A non-time-delay fuse installed in the front panel of the boiler’s electrical box. A
100mA time-delay fuse mounted on the boiler’s circuit board protects the board’s low voltage circuitry. No other fusing is installed in the
steam boiler.
The T100 control’s interface box is connected to the boiler’s low voltage Class 2 control circuit during installation using a factory supplied
cable. An access hole and knockouts, ½” trade size, are provided for room control wiring. The T100 may be mounted inside or outside the
steam room and its temperature sensor must be mounted inside the steam room. Temperature sensors require factory supplied 25 foot
(4.6 m) long cables for connection to the T100’s adapter box and a 25 foot (4.6 m) long shielded cable is supplied for connecting the T100
to it’s adapter box..
Standard equipment:
• Manual operation (boiler mounted RUN switch and manual ball valve drain) and single steam room (one steam valve, one
temperature sensor, one T100, two steam heads). Switches allowing manual heat and water control during routine service, lights
indicating heat and valve operating status and self-check fault codes.
Optional equipment:
• Second steam room (second steam valve, T100 and temperature sensor, two steam heads)
factory installed only
!
• RUN CLOCK (7-day or 24 hour clock for boiler ON/OFF scheduling).
• AUTODRAIN (24 hour clock plus electronic drain valve).
Water Quality Requirements:
The nature of a boiler or steambath steam generator requires testing of the feedwater to avoid potential high concentrations of impurities
which can cause a deposit or scale to form on the internal surfaces. This deposit or scale can interfere with the equipment’s proper opera-
tion and even cause premature steam generator failure. Concentration of impurities is generally controlled by treating the feedwater and/
or “blowing down” the steam generator when it is not heating. The steam generator “blow down” process involves draining and rinsing the
tank and re
fi
lling replacing it with makeup water.
To insure proper operation, the water supply should be tested prior to operating the equipment. There are several treatment processes
which can be used if you have a problem with hard water. A local reliable water treatment company can recommend the appropriate treat-
ment if required. The recommended feedwater minimum quality is listed below.
Feedwater Quality
Hardness
5.5 – 85 ppm (0.3 – 5.0 gpg)
T-Alkalinity
20 – 200 ppm (1.2 – 11.7 gpg)
TDS <100 ppm
Silica
<12 ppm
PH (strength of alkalinity)
7.0 – 9.0
Chlorine <0.1 ppm
Conductivity min 20
μ
S/cm