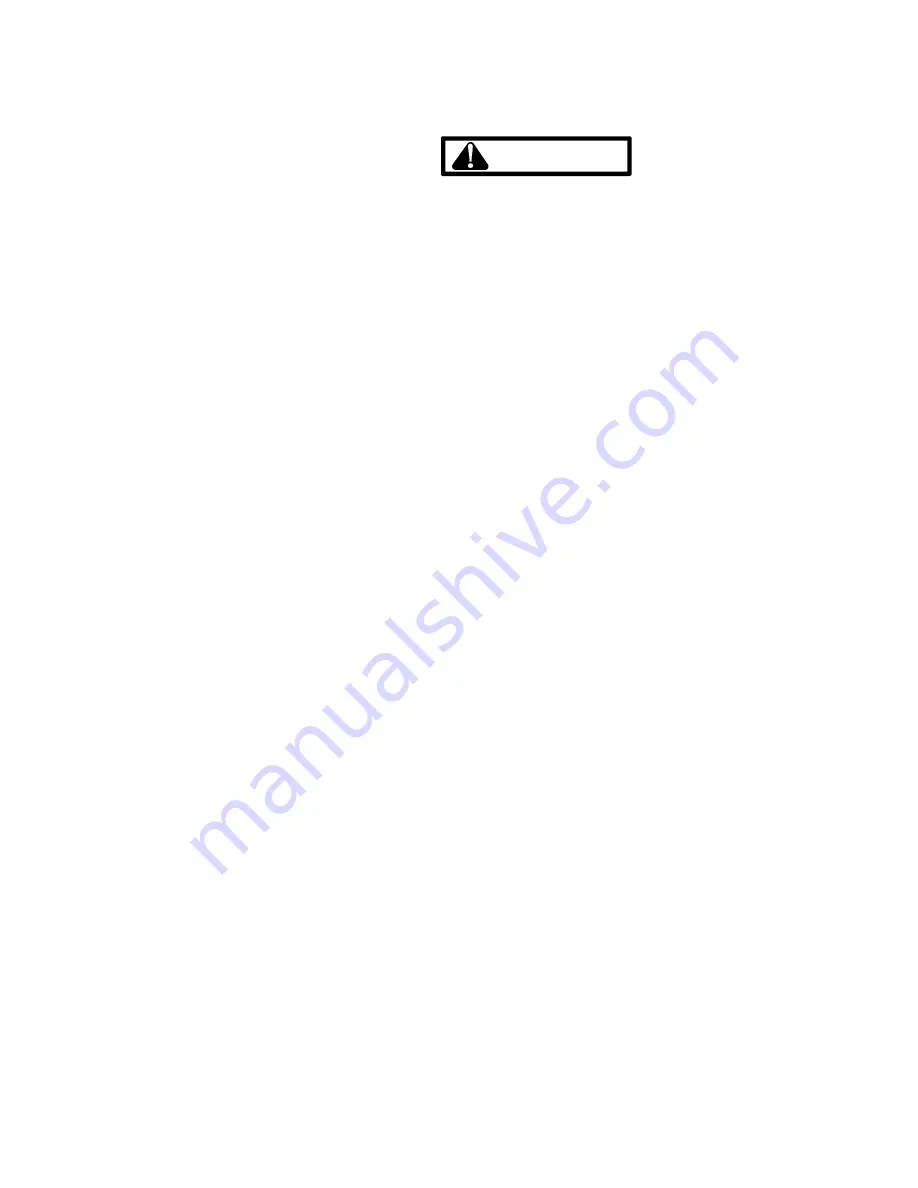
SERVICING
194 Rev. 3
S-113 OVERCHARGE OF REFRIGERANT
An overcharge of refrigerant is normally indicated by an ex-
cessively high head pressure.
An evaporator coil, using an expansion valve metering de-
vice, will basically modulate and control a flooded evaporator
and prevent liquid return to the compressor.
An evaporator coil, using a capillary tube metering device,
could allow refrigerant to return to the compressor under ex-
treme overcharge conditions. Also with a capillary tube me-
tering device, extreme cases of insufficient indoor air can
cause icing of the indoor coil and liquid return to the com-
pressor, but the head pressure would be lower.
There are other causes for high head pressure which may be
found in the "Service Problem Analysis Guide."
If other causes check out normal, an overcharge or a system
containing non-condensables would be indicated.
If this system is observed:
1. Start the system.
2. Remove and capture small quantities of gas from the suc-
tion line dill valve until the head pressure is reduced to
normal.
3. Observe the system while running a cooling performance
test, if a shortage of refrigerant is indicated, then the sys-
tem contains non-condensables.
S-114 NON-CONDENSABLES
If non-condensables are suspected shut down the system
and allow the pressures to equalize. Wait at least 15 min-
utes. Compare the pressure to the temperature of the cold-
est coil sense this is where most of the refrigerant will be. If
the pressure indicates a higher temperature than that of the
coil temperature, non-condensables are present.
Non-condensables are removed from the system by first re-
moving the refrigerant charge, replacing and/or installing liq-
uid line drier, evacuating and recharging.
S-115 COMPRESSOR BURNOUT
When a compressor burns out, high temperature develops
causing the refrigerant, oil and motor insulation to decom-
pose forming acids and sludge.
If a compressor is suspected of being burned-out, attach a
refrigerant hose to the liquid line dill valve and properly re-
move and dispose of the refrigerant.
Now determine if a burn out has actually occurred. Confirm
by analyzing an oil sample using a Sporlan Acid Test Kit,
AK-3 or its equivalent.
Remove the compressor and obtain an oil sample from the
suction stub. If the oil is not acidic, either a burnout has not
occurred or the burnout is so mild that a complete cleanup is
not necessary.
If the acid level is unacceptable, the system must be cleaned
by using the cleanup drier method.
CAUTION
DO NOT ALLOW THE SLUDGE OR OIL TO CONTACT THE
SKIN, SEVERE BURNS MAY RESULT.
NOTE: The Flushing Method using R-11 refrigerant is no
longer approved by Amana Refrigeration, Inc.
Suction Line Drier Clean-Up Method
Use AMANA part number R0157057 Suction Line Drier Clean-
Up Kit (41 cubic inches). This drier should be installed as
close to the compressor as possible, either in a vertical or
horizontal position. It may be necessary to use new tubing
and form as required.
In all applications, the drier inlet must be above the drier out-
let to provide proper oil return to the compressor.
NOTE: At least twelve (12) inches of the suction line imme-
diately out of the compressor stub must be discarded due to
burned residue and contaminates.
1. On a capillary tube evaporator coil, remove the strainer
and capillary tubes.
2. On an expansion valve coil, remove the liquid line drier
and expansion valve.
3. Purge all remaining components with dry nitrogen or car-
bon dioxide until clean.
4. Install new components including liquid liner drier.
5. Install suction line drier.
6. Braze all joints, leak test, evacuate, and recharge sys-
tem.
7. Start up the unit and record the pressure drop across the
cleanup drier.
8. Continue to run the system for a minimum of twelve (12)
hours and recheck the pressure drop across the drier.
Pressure drop should not exceed 6 - 8 PSIG.
9. Continue to run the system for several days repeatedly
checking pressure drop across the suction line drier. If
the pressure drop never exceeds the 6 - 8 PSIG, the drier
must be adequate and is trapping the contaminants and
it is permissible to leave it in the system.
10. If the pressure drop becomes greater, then it must be
replaced and steps 5 through 9 repeated until it does not
exceed 6 - 8 PSIG.
NOTICE: Regardless, the cause for burnout must be deter-
mined and corrected before the new compressor is started.
S-120 REFRIGERANT PIPING
The piping of a refrigeration system is very important in rela-
tion to system capacity, proper oil return to compressor,
pumping rate of compressor and cooling performance of the
evaporator.