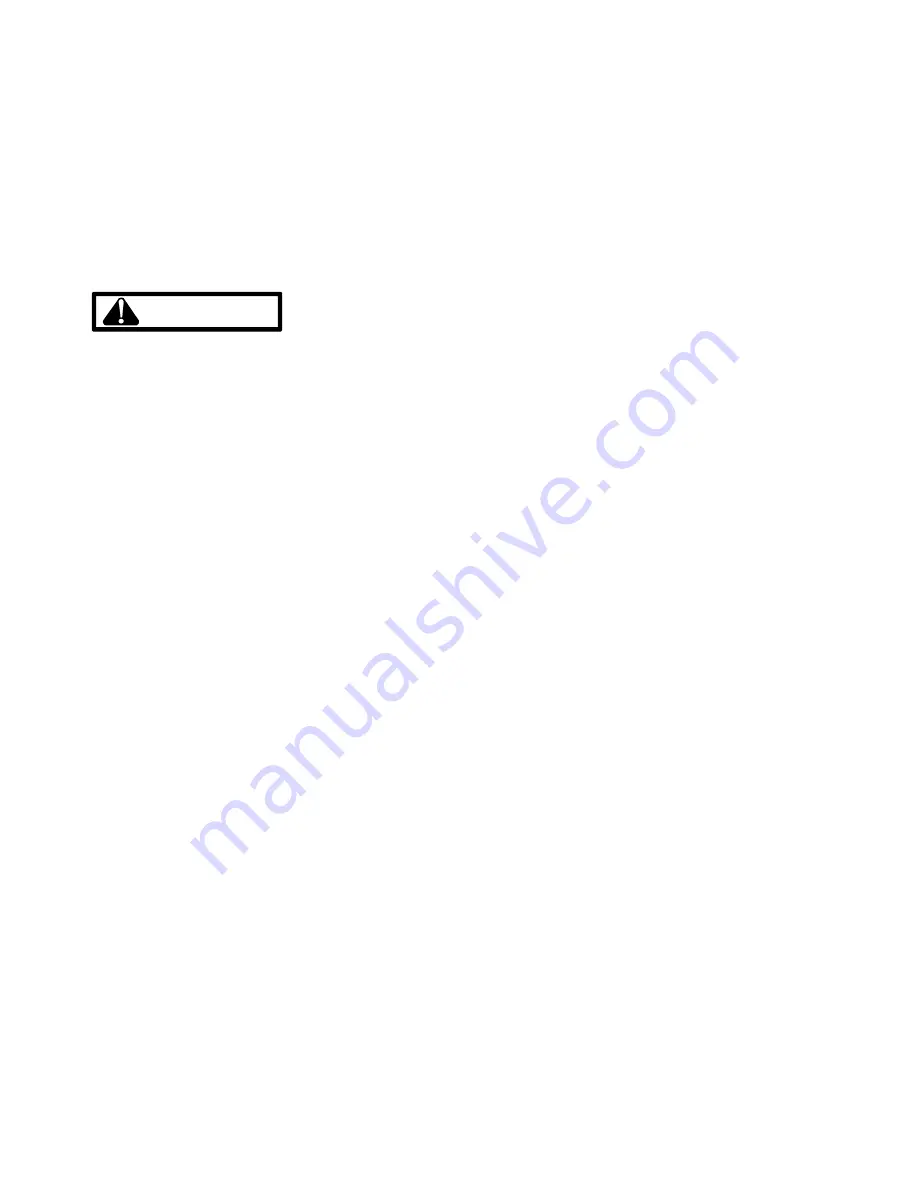
177 Rev. 3
COOLING PERFORMANCE DATA
SCHEDULED MAINTENANCE
The owner should be made aware of the fact that, as with any
mechanical equipment the remote air conditioner requires
regularly scheduled maintenance to preserve high perfor-
mance standards, prolong the service life of the equipment,
and lessen the chances of costly failure.
In many instances the owner may be able to perform some of
the maintenance, however, the advantage of a service con-
tract, which places all maintenance in the hands of a trained
serviceman, should be pointed out to the owner.
WARNING
DISCONNECT POWER SUPPLY BEFORE SERVICING
ONCE A MONTH
1.
Inspect the return filters of the evaporator unit and clean
or change if necessary. NOTE: Depending on operation
conditions, it may be necessary to clean the filters more
often. If permanent type filters are used, they should be
washed with warm water, dried and sprayed with an
adhesive according to manufacturers recommendations.
2.
When operating on the cooling cycle, inspect the con-
densate line piping from the evaporator coil. Make sure
the piping is clear for proper condensate flow.
ONCE A YEAR
Qualified Service Personnel Only
1.
Clean the indoor and outdoor coils.
2.
Clean the casing of the outdoor unit inside and out.
3.
The indoor and outdoor motors covered by this manual
are equipped with permanently lubricated bearings, no oil
is required.
4.
Manually rotate the outdoor fan and indoor blower to be
sure they run freely.
5.
Inspect the control panel wiring, compressor connec-
tions, and all other component wiring to be sure all
connections are tight. Inspect wire insulation to be
certain that it is good.
6.
Check the contacts of the compressor contactor. If they
are burned or pitted, replace the contactor.
7.
Using a halide or electronic leak detector, check all
piping and etc. for refrigerant leaks.
8.
Start the system and run a Cooling Performance Test. If
the results of the test are not satisfactory, see the
"Service Problem Analysis" Chart for the possible cause.