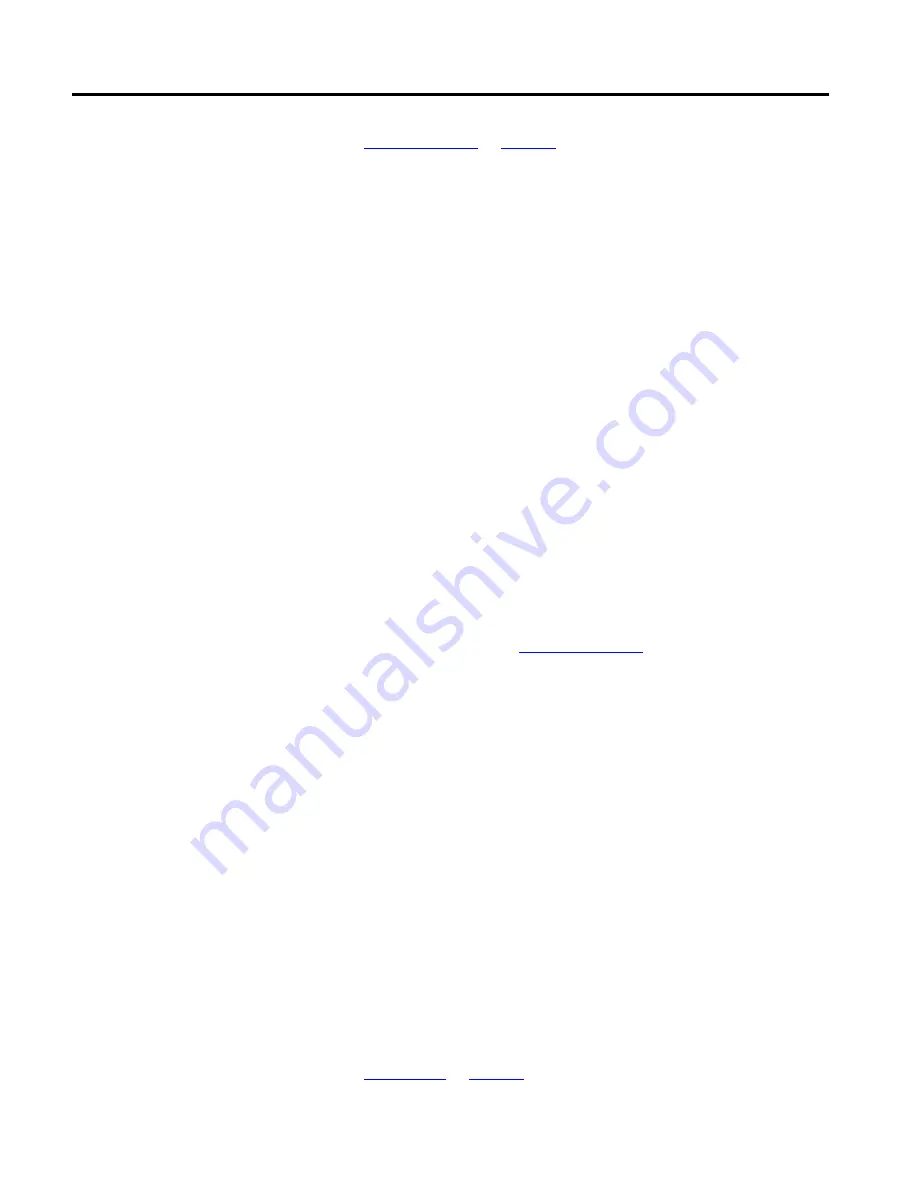
Configure Camming
Chapter 5
Rockwell Automation Publication MOTION-UM002F-EN-P - February 2018
217
Position-lock cams provide the capability of implementing non-linear electronic
gearing relationships between two axes based on a Cam Profile. Upon execution of
this instruction, the axis specified as the slave is synchronized with the axis
designated as the master. A position cam profile is defined by using a table of
points that contains the following information:
•
An array of master axis position values
•
An array of slave axis position values
The master axis position values correspond to the slave axis position values. In
other words, when the master axis reaches a specific position, the slave axis moves
to its specific corresponding point, as defined in the cam profile’s table of points.
Additionally, a position cam profile does the following:
•
Provides the capability of implementing non-linear electronic gearing
relationships between two axes
•
Does not use maximum velocity, acceleration, or deceleration limits
Position cam profiles are used with Motion Axis Position Cam (MAPC)
instructions. Upon execution of this instruction, the slave axis is synchronized
with the master axis. See the Logix 5000 Controllers Motion Instructions
Reference Manual, publication
to configure the position cam profile in an MAPC instruction.
Linear and Cubic Interpolation
The resultant calculated cam profiles are fully interpolated. This means that if the
current master position or time does not correspond exactly with a point in the
cam array used to generate the cam profile, the slave axis position is determined by
linear or cubic interpolation between adjacent points. In this way, the smoothest
possible slave motion is provided. The MCCP instruction accomplishes this by
calculating coefficients to a polynomial equation that determines slave position as
a function of master position or time.
Each point in the cam array used to generate the position cam profile can be
configured for linear or cubic interpolation. Electronic camming remains active
through any subsequent execution of jog, or move processes for the slave axis. This
allows electronic camming motions to be superimposed with jog, or move profiles
to create complex motion and synchronization.
See also
Position Cam Profile