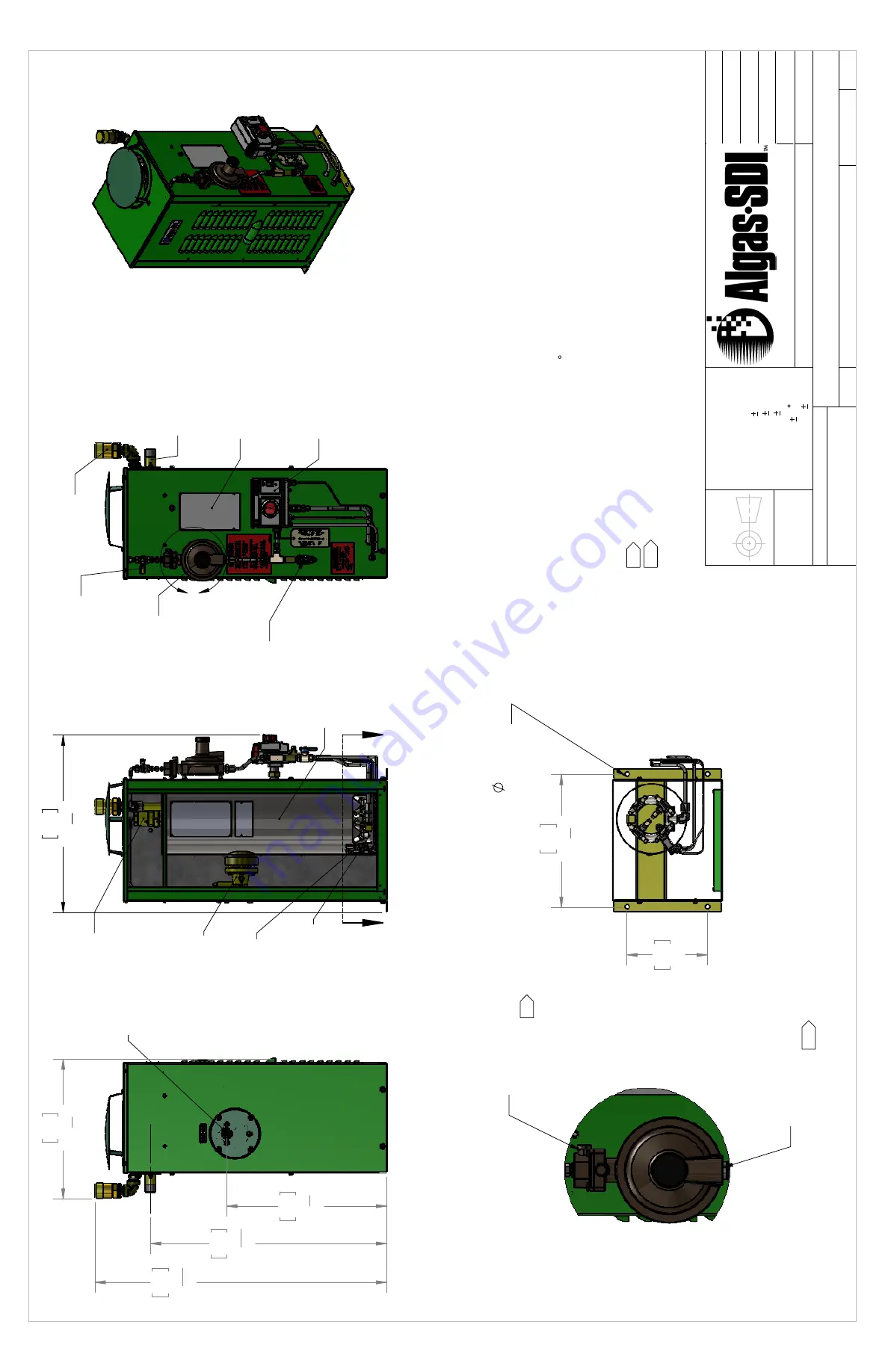
562
22
1 8
"
A
A
LIQUID
INLET
VALVE
CAPACITY CONTROL
VALVE
PILOT
BURNER
HEAT EXCHANGER
FRONT VIEW
DOOR REMOVED
FOR CLARITY
504
19
7 8
"
918
36
3 16
"
744
29
5 16
"
442
17
3 8
"
3/4" FNPT LIQUID INLET
LEFT VIEW
B
BURNER
REGULATOR
PRESSURE RELIEF VALVE
1" MNPT VAPOR OUTLET
START/SHUTDOWN INSTRUCTIONS
THERMOSTAT AND REIGNITOR ASSEMBLY
DRIP LEG DRAIN VALVE
ISOLATION
VALVE
RIGHT VIEW
NOTES:
ALL DIMENSIONS ARE IN INCHES [mm].
1.
VAPORIZER PRESSURE VESSEL RATED AT 290 PSIG [20 BAR] MAWP.
2.
VAPORIZER RELIEF VALVE SETTING 250 PSIG [17.2 BAR].
3.
cULus APPROVED.
4.
CE MARKED (PED).
5.
VAPORIZER CAPACITY AT 0
F AND 100 PSIG PROPANE INLET CONDITION
6. 40 GPH [80 KG/HR].
VAPORIZER TO BE SECURED THROUGH THE FOUR MOUNTING HOLES ON
7. ABOVE GROUND, LEVEL, SOLID, NON-COMBUSTIBLE BASE.
HEAT INPUT 51,360 BTU/HR [54,185 KJ/HR].
8. 9.
USE THE 1/8" FNPT PORT TO PIPE AWAY 1ST STAGE VENT IF REQUIRED.
10.
USE THE 3/4" FNPT PORT TO PIPE AWAY 2ND STAGE VENT IF REQUIRED.
11. APPROXIMATE SHIPPING WEIGHT 155 LBS [70 KG].
ISOMETRIC VIEW
NO SCALE
254 10"
419
16
1 2
"
SECTION A-A
4 X 1/2"
[13mm]
MOUNTING HOLES
DETAIL B SCALE 1 : 4
1ST STAGE VENT (1/8" FNPT)
9.
2ND STAGE VENT (3/4" FNPT)
10.
151 S. Michigan St., Seattle, Washington. USA 98108
Tel: (206) 789-5410 Fax: (206) 789-5414
Drawn By:
Checked By:
Approved By:
Date:
Scale:
Job #
Part #
Title:
Dwg. #
Size:
Sht. No.:
Rev.:
TOLERANCES
UNLESS OTHERWISE
SPECIFIED
B
DO NOT SCALE DRAWING
RWP
A.S.D.I. STD.
1of
1
1502-6001
D
5/22/12
1:10 AND NOTED
INTERPRET THIS DRAWING IN ACCORDANCE
WITH ANSI/ASME Y14.5-2009
DN
THIS DRAWING SHALL NOT BE REPRODUCED OR
USED IN ANY MANNER DETRIMENTAL TO IT'S
INTERESTS. ALL RIGHTS RESERVED.
© COPYRIGHT ALGAS-SDI
.X
.XX .XXX
ANGLE
0
30'
FRACTIONS
1/4"
THIRD ANGLE PROJECTION
SMALL DF VAPORIZER 40/40H EQUIPMENT DRAWING
Содержание Direct Fired 120/60H
Страница 4: ...This page left intentionally blank...
Страница 6: ...This page left intentionally blank...
Страница 9: ...This page left intentionally blank...
Страница 42: ...APPENDIX A TECHNICAL INFORMATION...
Страница 43: ...Figure 13 40 40H Vaporizer Replacement Parts 1 2 3 4 5 6 10 8 9 11 12 13 14 15 16 24...
Страница 55: ......