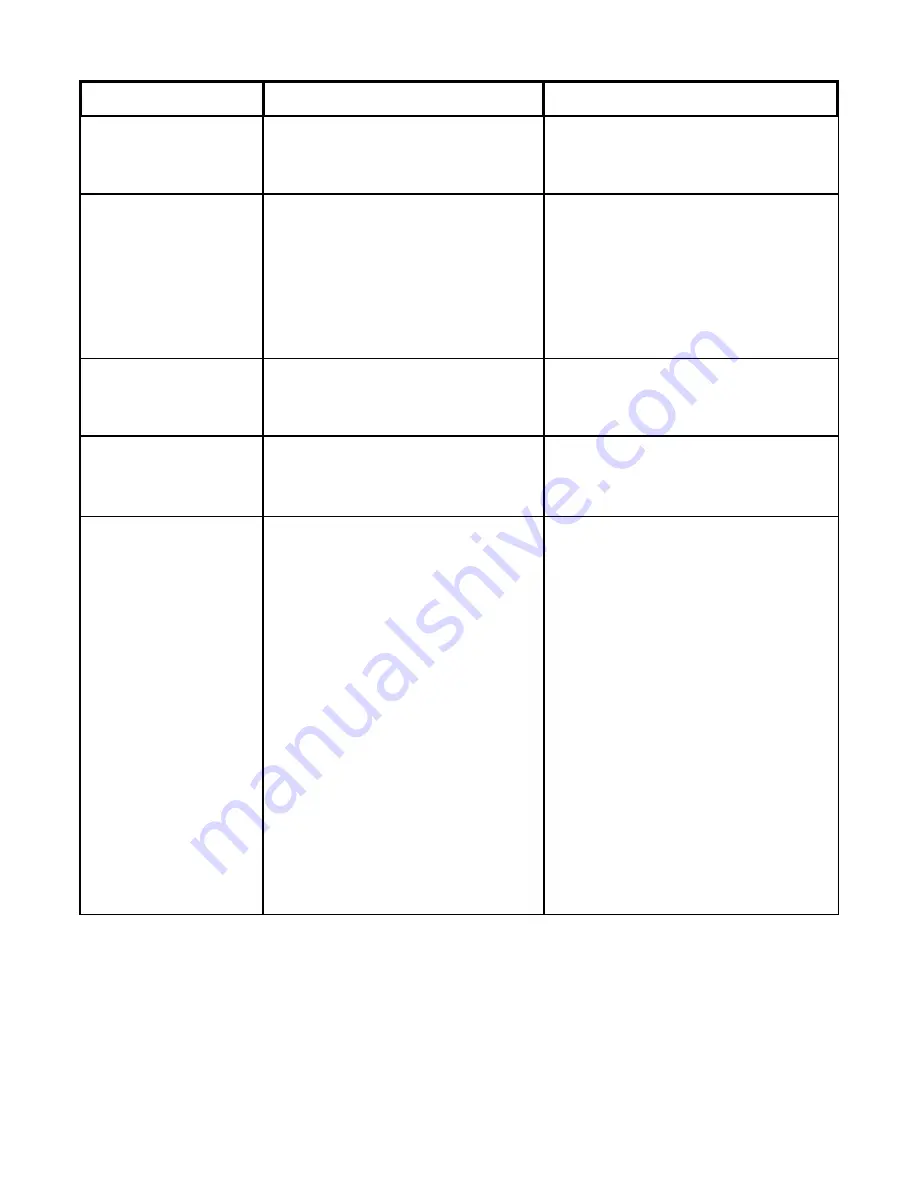
161 MF— 161 MTM
Ultima modifica/Last Update: 18/03/2008 Rev0 pagina 12 di 17
PROBLEM
CASE
SOLUTION
When welding the pro-
tection devices of the
line set off.
Make sure the welding current does not re-
quire greater power than the one supplied
by the line.
Decrease the welding current.
The welding is non opti-
mal.
Spattering occurs during welding.
Porosity in the deposit.
Too narrow welding seam (“dry arc”).
Too wide welding seam (“too hot weld
pool”).
!
Make sure welding polarity is correct, the
earth clamp is fixed correctly.
!
Decrease the set voltage value and check
the gas emission from the torch.
!
Increase the electronic inductance pa-
rameter and/or voltage.
!
Decrease the electronic inductance pa-
rameter and/or voltage.
The machine stops
welding and emits an
acoustic signal.
The maximum current that can be supplied
by the machine has been exceeded.
Decrease the value of the welding parame-
ters.
Non optimal MIG weld-
ing start.
Spattering occurs on starting and crackling. Increase post-gas to decrease the oxidation
status of the welding wire.
Gas does not come out
from solenoid valve.
Excessive gas pressure.
Damage solenoid valve wiring.
The solenoid valve control relay on the
front panel is damaged.
Solenoid valve is damaged.
!
Remove the gas connection. Carry out a
gas test on the front panel in the MIG/TIG
procedure and check opening of the sole-
noid valve. Reduce gas pressure. Restore
connections and carry out a gas test.
!
Switch off the machine and disconnect the
plug:
Should there be no continuity, single out
the disconnection and repair it;
Make sure that the wiring contacts are
correctly inserted in the connectors.
!
The front panel must be replaced.
!
Should the operations carried out not have
a positive outcome, replace the solenoid
valve.
Should the operations carried out not have a
positive outcome, try to replace the Toroidal
Transformer.