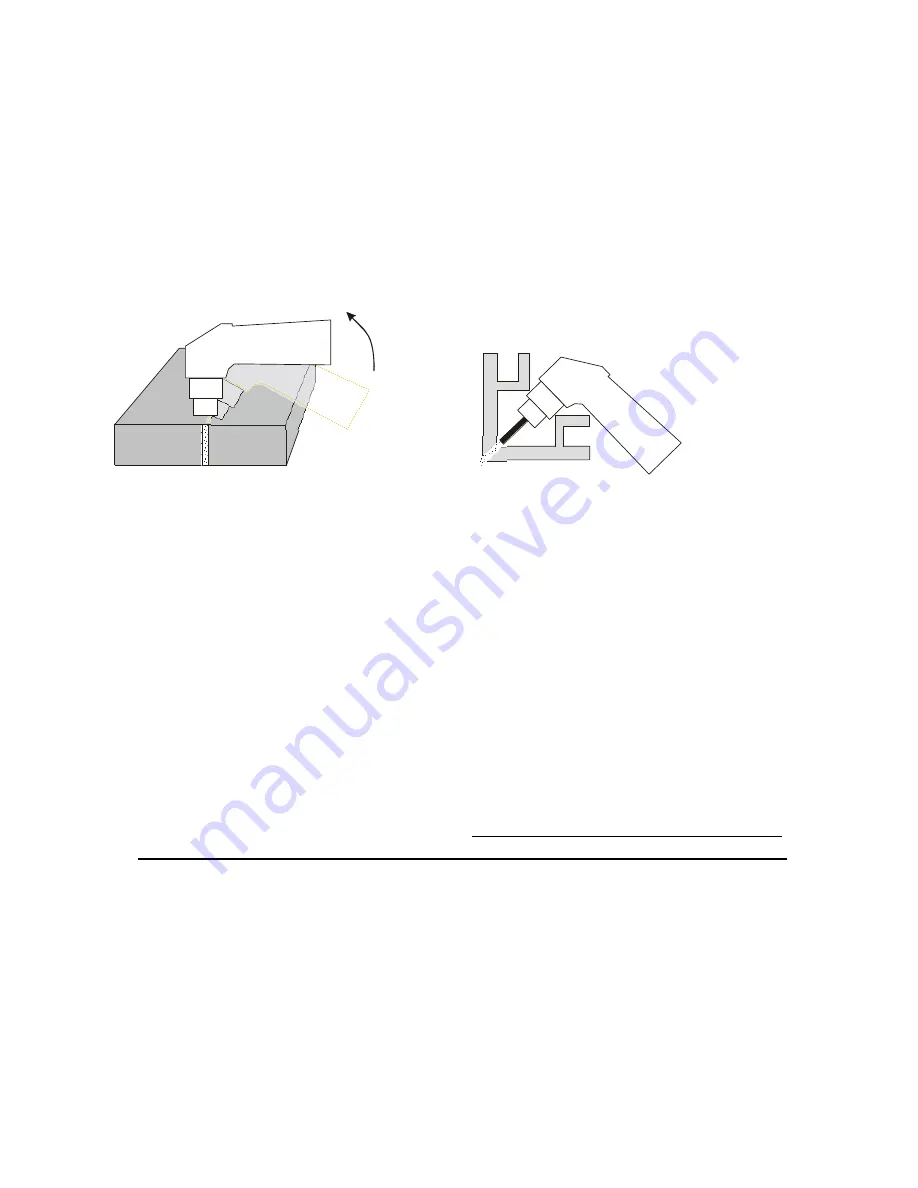
17/21
ALFA IN a.s
©
www.alfain.eu
3
6. We recommend starting cutting at the edge of the material. If needed to
start from the centre of the material, or to cut hole into the material, slightly
tilt the torch head and gradually it straighten into a vertical position so the
spraying material would not damage the cutting tip (see Figure 5). This
workflow must always be followed, if the thickness of material is above
above 3 mm.
7. In case of cutting in the corner or around the corner (see Figure 6), use the
long electrode and cutting tip. The cutting power while using the Long
cutting tip is decreased.
Fig. 5
Fig. 6
7.6 IMPORTANT RULES
1. The pilot arc burning time should be limited only to the time necessary. It
lowers the wear of the cutting tips and electrodes.
2. Never turn off the main switch immediately after finishing cutting but always
leave time to run cooling cycle to cool down the torch. Immediate turn-off
only in case of emergency.
3. The biggest influence on the cut quality, durability of the nozzles, electrodes
and the whole torch has compressed air. Ensure correct setting of pressure:
The pressure during cutting must not fall below 3.5 bar. The air must not
contain mechanical impurities, oil and water condensate. These
contaminants reduce the quality of the cut, causing instability and
extinguishing the arc, and can damage the torch. A source of pressurized
air must therefore be provided with an effective and reliable filtration, oil
separator and water condensate trap. Using filters and separators built on
PEGAS 160 PLASMA as the sole treatment stage air is totally inadequate.
In cases where the compressor sucks air of high humidity, resulting in the
need for frequent draining of the pressure tank, it is necessary to include in
the inlet one more effective as a dirt separator third stage. The captured
condensate must be discharged every day, and all tailing and pressure
vessels compressor.
Ensure a good el. contact of the work lead clamps
and cutting material.
4. Check and timely exchange cutting tips and the electrodes. Lifetime of these
parts is only a few hours of cutting time and is highly dependent on
compliance with the principles of good cutting.