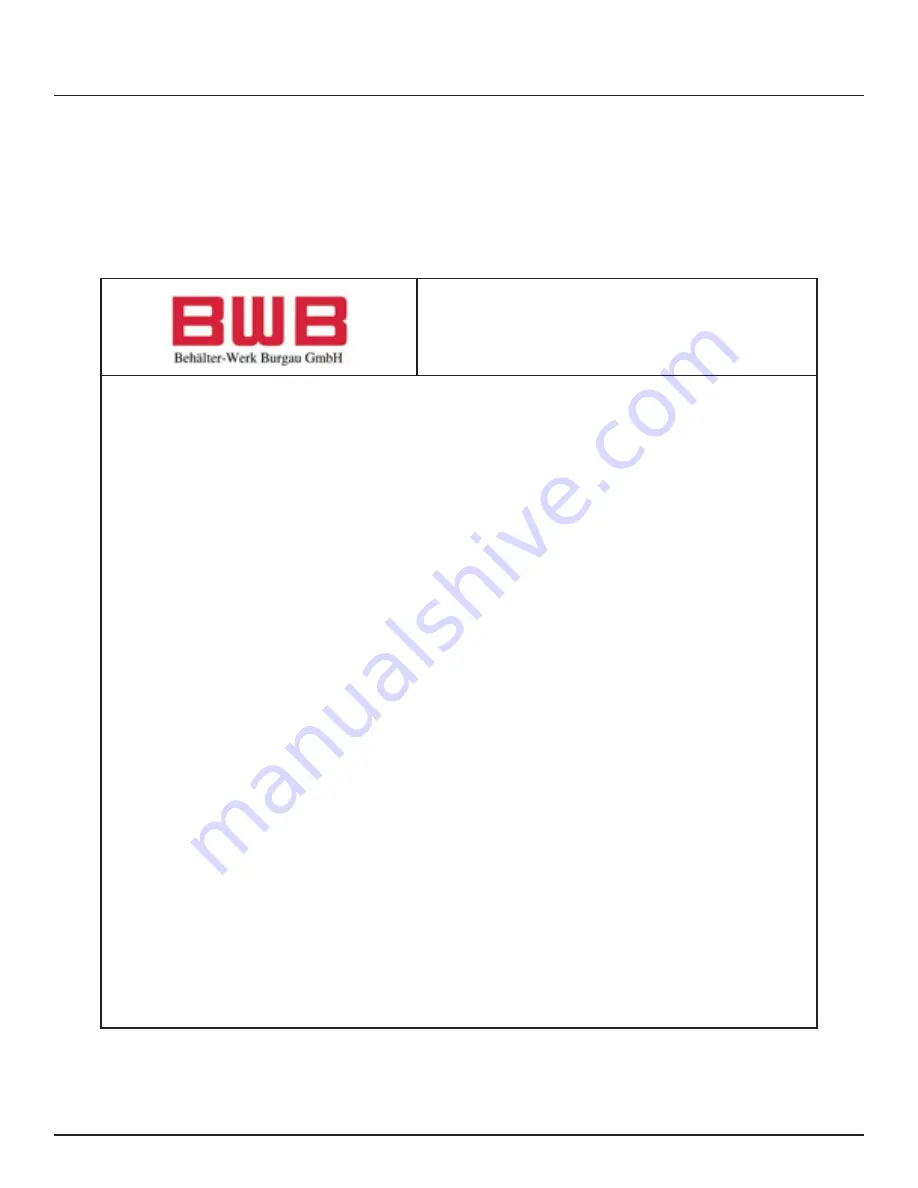
Air Techniques, Inc.
Page 16
6
Vessel Operations Instructions
Pressure receivers from company Behälter-Werk Burgau GmbH are used in these products.
Type 316034 / 5430-200-51
PS 8 bar
V 25l
CE 0036
T
max
100°C T
min
-10°C Ph 12 bar
EN 286-1:19 F
Serial number and year of fabrication (look at the nameplate)
Application: Pressure vessel for stationary installations
Medium: Air / Nitrogen
Corrosion allowance: c=0 mm
The pressure vessel is only to be used for the application specified above in accordance with the
technical specifications. Safety reasons prohibit any other applications.
The pressure vessel has been manufactured according to the EEC regulation 87/404 as a single
component without safety equipment for the above mentioned application. The layout was mainly
effected for a permanent load by internal pressure.
Before commissioning, the vessel is to be provided with the required safety equipment such as
manometer, overpressure control devices, and safety valve, etc. These components are not part
of our supply. No welding or heat treatment of any kind is permitted to those vessel walls which are
exposed to pressure.
It must be ensured that the internal pressure will not permanently exceed the maxi-mum working
pressure PS stipulated on the vessel nameplate; however, it may momentarily do so by up to 10%.
Suitable measures are to be taken to prevent both vibrating stress and corrosion.
The pressure vessel is to be installed in a way that guarantees its safety in use (e.g. no rigid connection
with the floor, the machine frame or oscillation damper).
Taking into consideration all components of the equipment , the instructions, issued by the supplier of
the pressure vessel, must include:
a) instructions for discharging the condensate
b) information referring to the maintenance of the pressure vessel in order to guarantee is safety in use.
The supplier must also decide whether the pressure vessel, once equipped and ready for operation,
is to be subjected to an acceptance test before operation. The supplier/operator is obliged to observe
the laws and decrees regarding the operation of the pressure vessel valid in the respective country.
The vessel is resistant to fatigue strength at a pressure variation range of 2 bar
(10% PS)
Remarks:
The condensation drain must be performed under interior pressure according to the
operating instruction of Air Techniques.
Vessel Operating Instructions