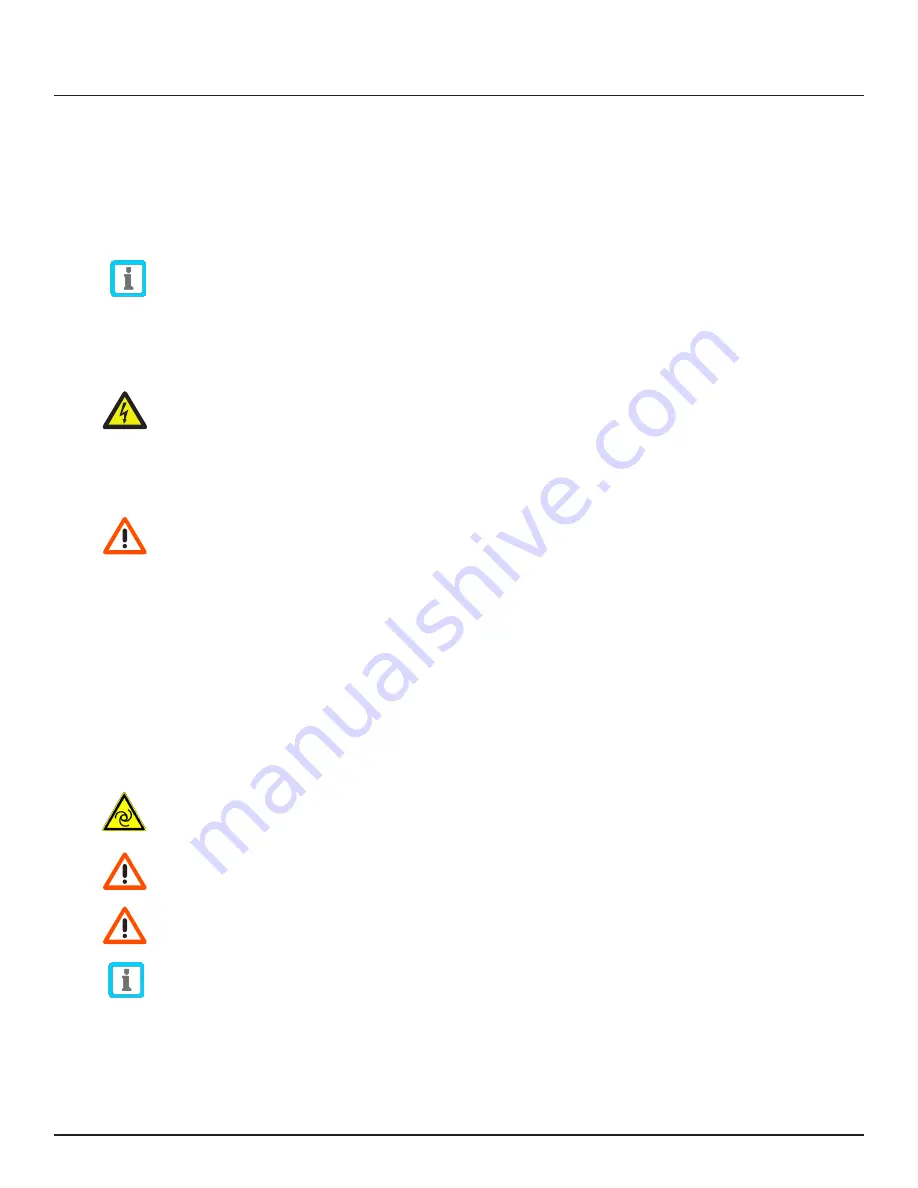
Page 9
Air Techniques, Inc.
2.3.2 Compressed air connection
The compressor stations are fitted as standard with control gear, consisting of a pressure switch, pressure gauge,
safety valve, check valve and condensate drain.
The compressed air connection takes place at the pressure switch via a 0.635 cm ID thread. A quick coupling with
hose nozzle if not included in the scope of delivery, is available as an accessory. Fasten the pressure hose at the
hose nozzle with the help of a hose clamp.
Approximately 70% of the products induced electrical energy is converted into heat and is given off
to the surrounding area.
To prevent vibration transference it is advisable to install a flexible pressure hose between the pressure switch and
user’s line. As a further accessory, a pressure reducer unit (see figure 4) can be connected.
2.3.3
Electrical installation
The connection to the mains voltage supply must only be carried out by a qualified electrician! (with
the exception of the ready to plug-in supplied stations for connection to the safety plug socket).
Observe closely the local regulations for power undertakings. The connection must only be carried out on a power
supply with correctly installed protective conductor. Equipment with safety contact plug must be connected to a
safety contact socket.
The product should only be connected to a safety plug socket, DE1 with correctly installed
protective conductor. If this is not fitted the plug has to be exchanged by a qualified electri-
cian according to the customary loading system.
If the equipment is hard wired to the power supply a switch arrangement must be arranged with at least a 3 mm wide
contact opening (e.g. heavy duty switch).
If the product is connected to the power supply with the aid of a plug, the socket must be easily accessible for safety
reasons, so that in the event of danger the equipment can be isolated from the power supply. Please make sure
that the connection cable does not run across the machine. The hot surface of the compressor station could dam-
age the insulation of the cable.
Prior to making the electrical connection, check the mains voltage and frequency. They should correspond with the
specifications on the model label.
Please observe that the relevant circuit is protected by the correct fuse.
2.3.4 Motor protection
Attention! After cooling off, products with temperature switch start again automatically!
If the motor locks for example on starting against pressure or a short circuit in the motor windings,
the current consumption can become so high that a fitted temperature switch might get damaged.
This can only be controlled in a safe way by the installation of an external overload protector.
When using outside of normal operating conditions the installation of an overcurrent switch is absolutely
essential!
Should the installation procedures be disregarded or carried out incorrectly the warrantee will be
invalidated.
Motor protection for 1-stage AC-current motors (230 V AC):
The motors are equipped with a thermal protection switch to prevent overheating of the motor windings. In the case
of too high an ambient temperature, the thermal protection switch shuts down the unit by cutting off the operating
current.
Transport, Storage, Initial Operation