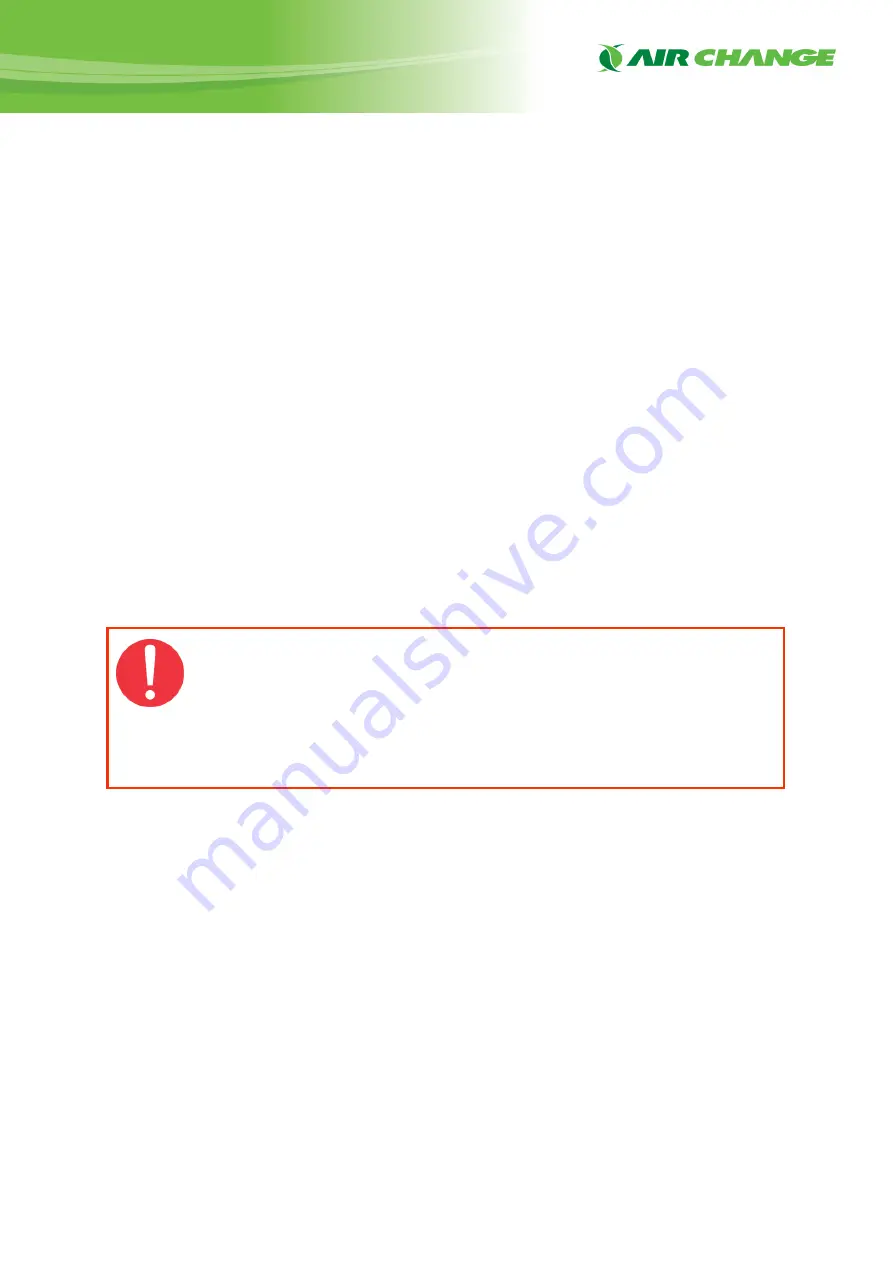
Installation and Maintenance Manual
15
Scroll Compressors
(Not applicable in PCU-D Systems only)
Air Change units employ Scroll compressors.
Scroll compressors and all electrical components are housed in their own separate compartment,
together with reversing valves, other refrigerant parts and pipe work.
Compressors are suitable for condensing temperatures of not greater than 55°C at design ambient.
Scroll compressors are of rigid design with limited number of moving parts. They provide constant
and stable compression at variable speed.
If there is a need to detect a leak in the refrigerant system, never subject the compressor to a
pressure greater than 1400 kPa.
Should a compressor fail and burn out, follow the guidelines for correct replacement and properly
clean out the system including the liquid line drier (where fitted) and fit a suction line drier to
remove contaminants from the system. The suction line drier must be checked and replaced before
returning the system to normal operating condition.
All compressors are fitted with internal line break overloads. Should there be a problem such that
the internal overloads trip, it may take several hours for them to reset (or longer on very hot days).
Accompanied with the scroll compressor are characteristic sounds that do not affect reliability or
indicate that the compressor is defective.
̵
At start up:
Under conditions of low refrigerant flows (low suction pressures) such as start-up, a
rattling sound may emanate from the compressor. This will be heard until the head pressure is
great enough to allow the thermal expansion valve to flow sufficient refrigerant and increase the
suction pressure.
̵
At shut down:
The gas within the scrolls expands and causes momentary reverse rotation,
resulting in a ‘flutter’ type noise.
̵
Refrigerant flooding:
If the compressor experiences severe liquid slugging during operation,
the compressor will make a loud rattling sound. This is normal because of the separation of the
scrolls which allow the liquid refrigerant to pass through the compressor without damage.
IMPORTANT
The compressor can only cycle a maximum of 12 times per hour. The controller will
optimize the starting time by making sure the minimum time delay between each start-
up is 5 min.
Never disconnect the compressor contractor from the controller.
Do not condemn a compressor until time has been allowed for reset of internal
line break overloads.
Cooke Industries - Phone: +64 9 579 2185 Email: [email protected] Web: www.cookeindustries.co.nz