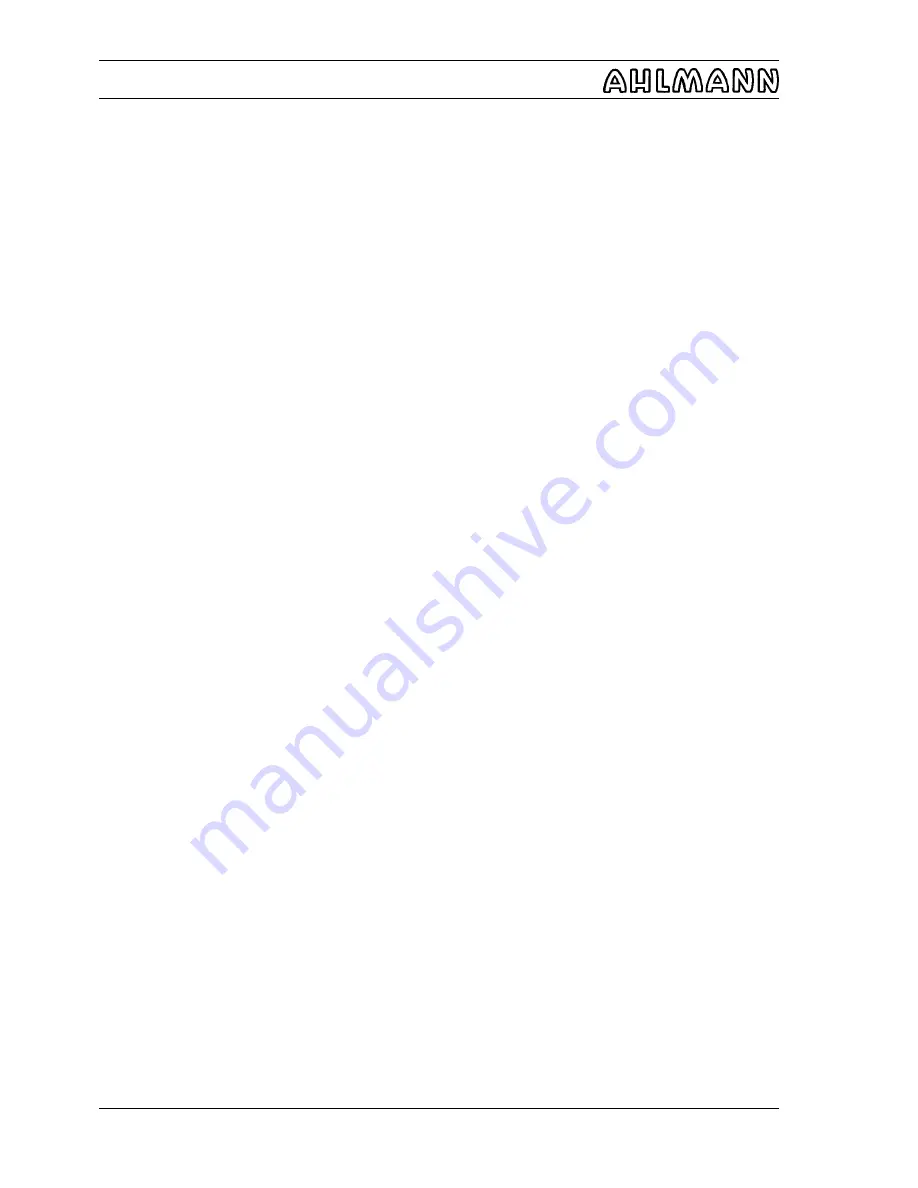
S220/S221/S230/S231/Z200
1-4
1
Safety Regulations
These persons must:
- have attained the age of 18 years,
- be physically and intellectually suitable,
- have been instructed in the operation or maintenance of
the machine and must have demonstrated their ability to
their employer,
- must be expected to carry out the work conveyed to them
in a diligent manner.
1.4.2
Electrical work on the machine may be carried
out only by a qualified electrician or persons supervised by
a qualified electrician according to the electrical regula-
tions.
1.4.3
Only qualified specialists may carry out work on
the chassis, the brake and steering system.
1.4.4
Only personnel with special experience and the
necessary know-how are permitted to carry out work on the
hydraulic system.
1.5
Safety Information for Certain
Operating Phases
1.5.1
Normal Operation
1.5.1.1
Other persons must not be transported!
1.5.1.2
Start and drive the machine from the driver’s seat
only!
1.5.1.3
Observe the control lamps according to the ope-
ration manual (machine and engine) during starting and
switching-off operation!
1.5.1.4
Before commencing work / driving, make sure
that the brakes, steering, signal beacons and lights function!
1.5.1.5
Before moving the machine, always check that
the attachments are safely stowed so that no accident
may occur!
1.5.1.6
Before commencing work, make yourself familiar
with the working environment. This means observing
obstacles on the working site, quality and resistance of the
soil, undertaking the necessary protection precautions
between the building site and public traffic.
1.5.1.7
Before starting the machine, make sure that no
person is endangered by the moving machine!
1.5.1.8
Take measures so that the machine can be
operated
only
in a safe and functional manner. The
machine may only be operated when all safety devices,
e.g. detachable safety devices and sound absorption,
exist and function.
Содержание AS 210
Страница 7: ...Safety Regulations ...
Страница 19: ...Signs ...
Страница 22: ...ProtectionAgainstTheft ...
Страница 25: ...Description ...
Страница 33: ...Operation ...
Страница 44: ...Attachments ...
Страница 53: ...Rescue Towing Lashing Lifting by Crane ...
Страница 60: ...Maintenance ...
Страница 78: ...Faults Causes and Remedies ...
Страница 81: ...Diagrams ...
Страница 98: ...Technical Data Loader ...
Страница 102: ...Technical Data Attachments ...
Страница 115: ...AdditionalOptions Modifications Notes on Inspection for Loaders ...