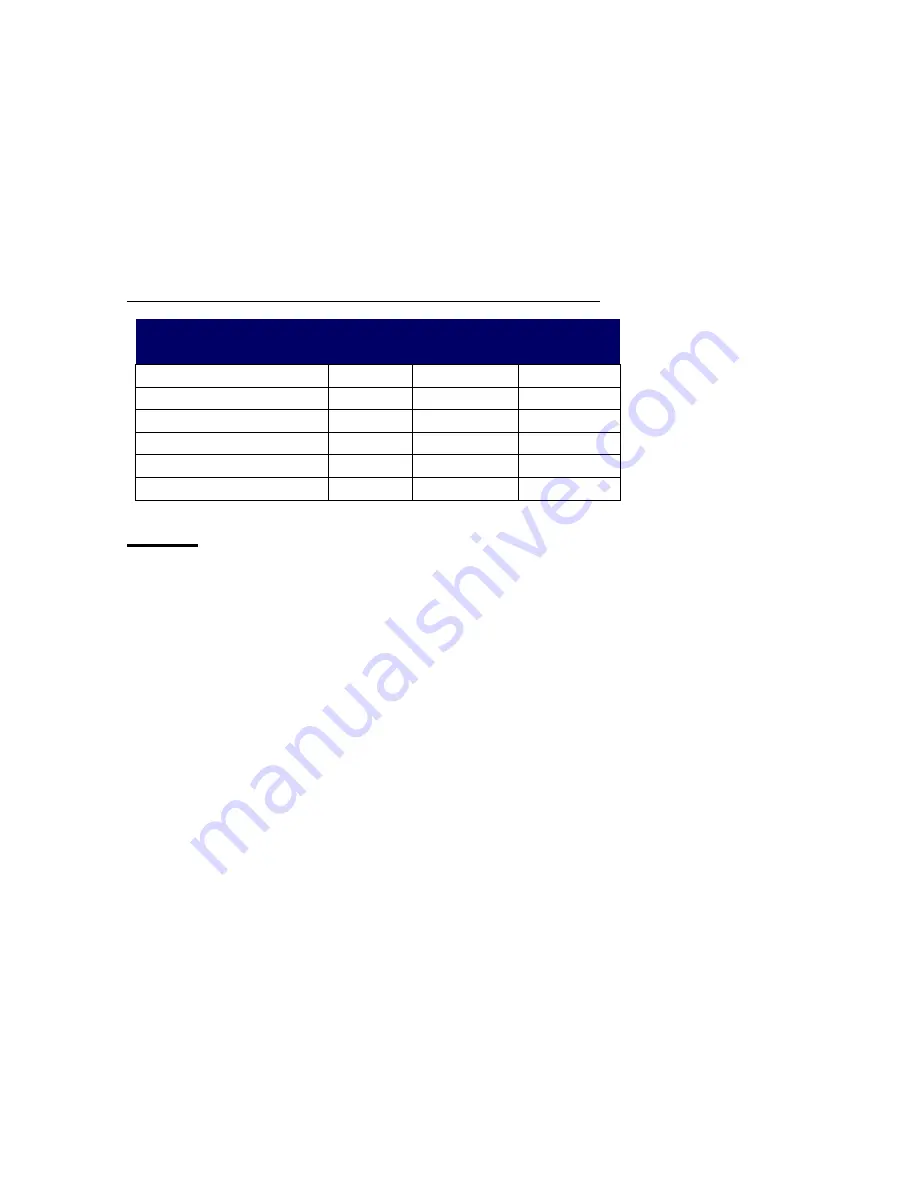
9
AGC Stopray SMART
–
Processing Guide
–
Version 4.1
–
May 2020
normally would be edge-stripped in order to avoid any contact between glass and coating. For large
sheets of glass, a sheet of paper should be placed on the center of the glass.
The glass must be completely dry. We recommend checking whether the air filters of the ventilation
units are clean.
Two or three halogen lights should be present at the exit of the washer to light the glass
correctly (vertically from top to bottom) and even detect and quickly correct any deviations from
the requirements listed above.
Summary of the quality of water used for shaping and washing the glass:
SHAPING
WASHING
Rinsing
Washing
Coolant
No
------
------
Detergent
------
No
No
Heating tank temperature
------
------
40 ± 5 °C
Water temperature
------
------
> 35 °C
pH
7 ± 1
7 ± 1
7 ± 1
Conductivity
------
< 30 µS/cm
< 100 µS/cm
Remarks:
Any small marks after washing (during handling ) can be removed by using a wet cloth (water) and
then a dry cloth. Soft circular movement must be applied.
6
Silk screen printing
6.1
Stopray SMART with silkscreen
In case of a silkscreen on the Stopray SMART, where the silkscreen is in contact with the sealant joint, the
edge-deletion of the coating is required prior to the application of the silkscreen.
For silkscreen that is in contact with the sealant joint, the compatibility of the sealant joint, structural
joints and weatherseals with the silkscreen (enamel) paint is under responsibility of the manufacturer of
the insulating glazing units, and should be assessed in cooperation with the sealant supplier.
The calculation and dimensioning of the sealant joint is under responsibility of the manufacturer of the
insulating glazing units.
AGC recommends to assess the aesthetics by means of a mock-up sample.
Additional recommendations:
Any impurities on the coated surface can be removed using a compressed dry-air jet.
AGC recommends using clear-coloured enamels that have a sufficiently high energy reflection
level. A dark-coloured enamel will have a relatively high energy absorption level and the coating
may be damaged under the enamel during the heating process.
Similarly, when the coverage percentage is very high and confined to a very small area, the
printed section of the glass may behave differently to the uncovered section in the quench.
In any case, the final result will depend on the type of furnace used, its parameters, the colour
and type of enamel used and the desired pattern. The processor will have to carry out preliminary
tests, and manufacture some mock-up samples on a case by case basis, to avoid these
problems. AGC is not liable under any circumstances for the outcome of the operation.
The presence of enamel on the coating changes the optical properties of the final glass product.