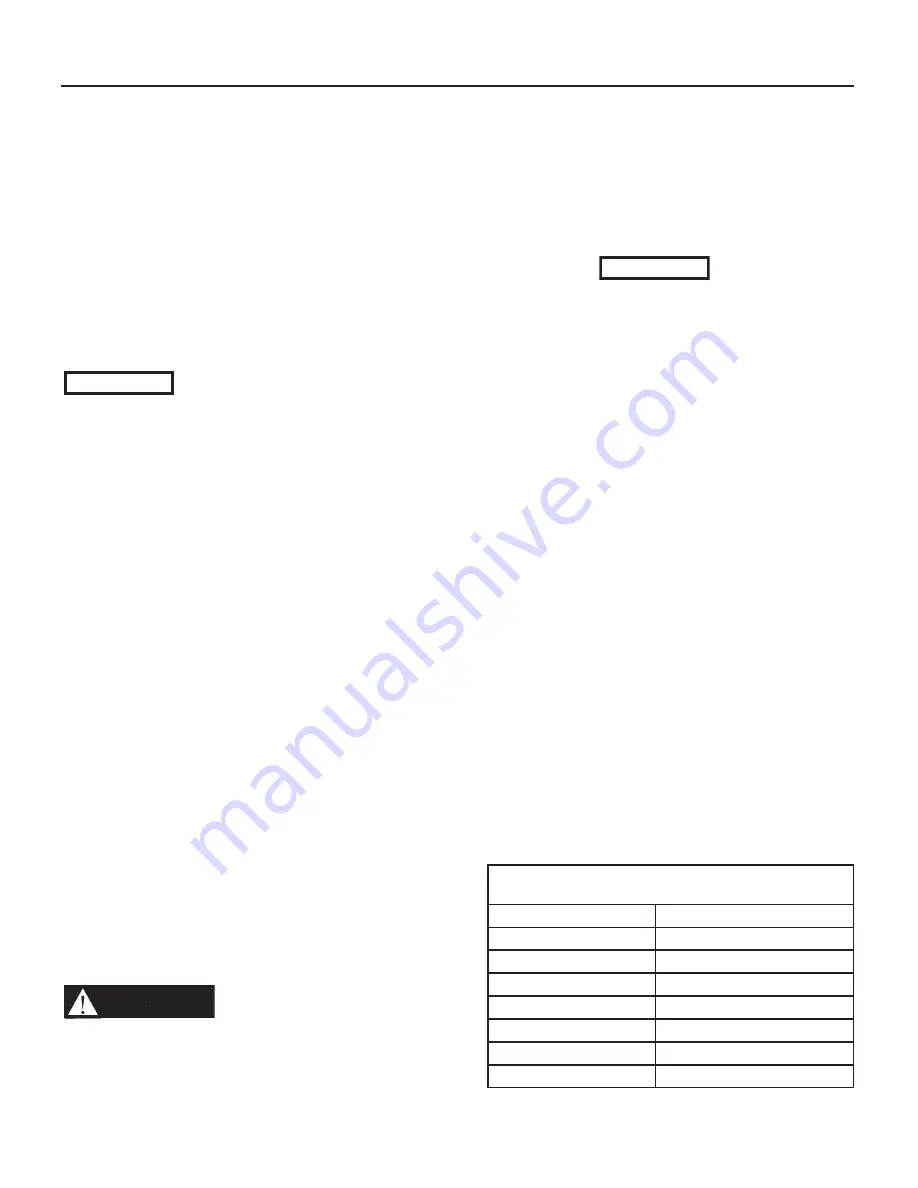
38
8.2.3 - Expansion Tank
If a water heater is installed in a
closed water supply system, such
as one having a backflow preventer
in the cold water supply line, means
shall be provided to control thermal
expansion. Contact the water supplier
or local plumbing inspector on how to
control this situation.
Install an expansion tank. Ensure
the expansion tank is properly sized
for the water volume (See Section
18, header “Content of water”) and
the system volume, temperature and
pressure.
CAUTION!!!
Undersized
expansion tanks will cause
system water to be lost
through the relief valve
The expansion tank must be located
as shown in Figure 8-5 or as per
recognized design methods. Refer
to the expansion tank manufacturer
instructions for additional installation
details.
8.2.4 - Circulator pump
This water heater must be fitted with a
circulator pump for domestic potable
hot water. To size and install the pump
follow section 8.4.
8.2.5 - Sizing water
system
Size the piping and system
components required in the water
system, using recognized design
methods.
8.2.6 - Anti-legionella
This water heater is not protected
against the proliferation of the
Legionella bacteria. If you don’t
install any Anti-legionella external
system, you have to keep the water
temperature, at least at 140°F (60°C).
This temperature will prevent the
proliferation of the legionella bacteria.
WARNING!!!
Your domestic
hot water system must be
protected against legionella
bacteria. Failure to comply with
this provision can result in
severe personal injury or death.
8.4 - How to install
the circulator pump
This water heater must be fitted with a
circulator pump for domestic potable
hot water. Size the pump follow figure
8-3 in function of the model and in
function of the water hardness.
CAUTION!!!
undersize the
circulator pump could damage
the water heater due to scale
formation and corrosion.
To electrically connect the pump
(Local pump) follow Figure 10-2.
A field supplied pump relay must be
installed if the pump current draw is
greater than 3 amps.
If the pump have an interax of 6” 1/2,
you can install it between flanges “C”
and “D” of Figure 8-4. If the pump
have an interax of 8” 1/2, replace
pipe “D” with the factory supplied pipe
“F” and apply seal adapter “G” with
gasket “H” (both factory supplied) as
shown in figure 8-4.
For the electrical connection, proceed
as follows (refer to Figure 10-2):
1. remove the heater casing following
the instructions given in section 17.2
and open the junction box cover;
2. use a three conductor cable with
a minimum cross section of #18
AWG between the water heater
and the pump;
3. connect the cable leads to the
“113”, “114” and “Ground”
terminals as shown in Figure 10-
2.
4. connect the other side of the
cable to the pump as shown in
the instruction supplied with the
pump.
8 - INSTALLATION - Water connections
8.3 - Scalding
This water heater can deliver scalding
temperature water at any faucet in the
system.
Be careful whenever using hot water
to avoid scalding injury.
Certain appliances such as
dishwashers and washing machines
may require increased temperature
water.
By setting the water temperature
control on this water heater to obtain
the increased temperature water
required by these appliances, you
may create the potential for scald
injury.
To protect against injury, you should
install a mixing valve in the water
system.
This valve will reduce point of
discharge temperature by mixing cold
and hot water in branch supply lines.
Such valves are available from the
local plumbing supplier.
Figure 8-2 details the relationship
of water temperature and time with
regard to scald injury and may be
used as a guide in determining the
safest water temperature for your
applications.
APPROXIMATE TIME / TEMPERATURE
RELATIONSHIPS IN SCALDS
120°F (49°C)
More than 5 minutes
125°F (51°C)
1,5 to 2 minutes
130°F (54°C)
About 30 seconds
135°F (57°C)
About 10 seconds
140°F (60°C)
Less than 5 seconds
145°F (63°C)
Less than 3 seconds
150°F (65°C)
About 1,5 seconds
155°F (68°C)
About 1 second
Figure 8-2 Time / temperature scalds
Содержание Esteem 399
Страница 3: ...3 SAFETY INSTRUCTIONS ...
Страница 5: ...5 SAFETY INSTRUCTIONS ...
Страница 112: ...112 17 MAINTENANCE ...
Страница 116: ...116 19 SPARE PARTS Spare parts ...
Страница 135: ......