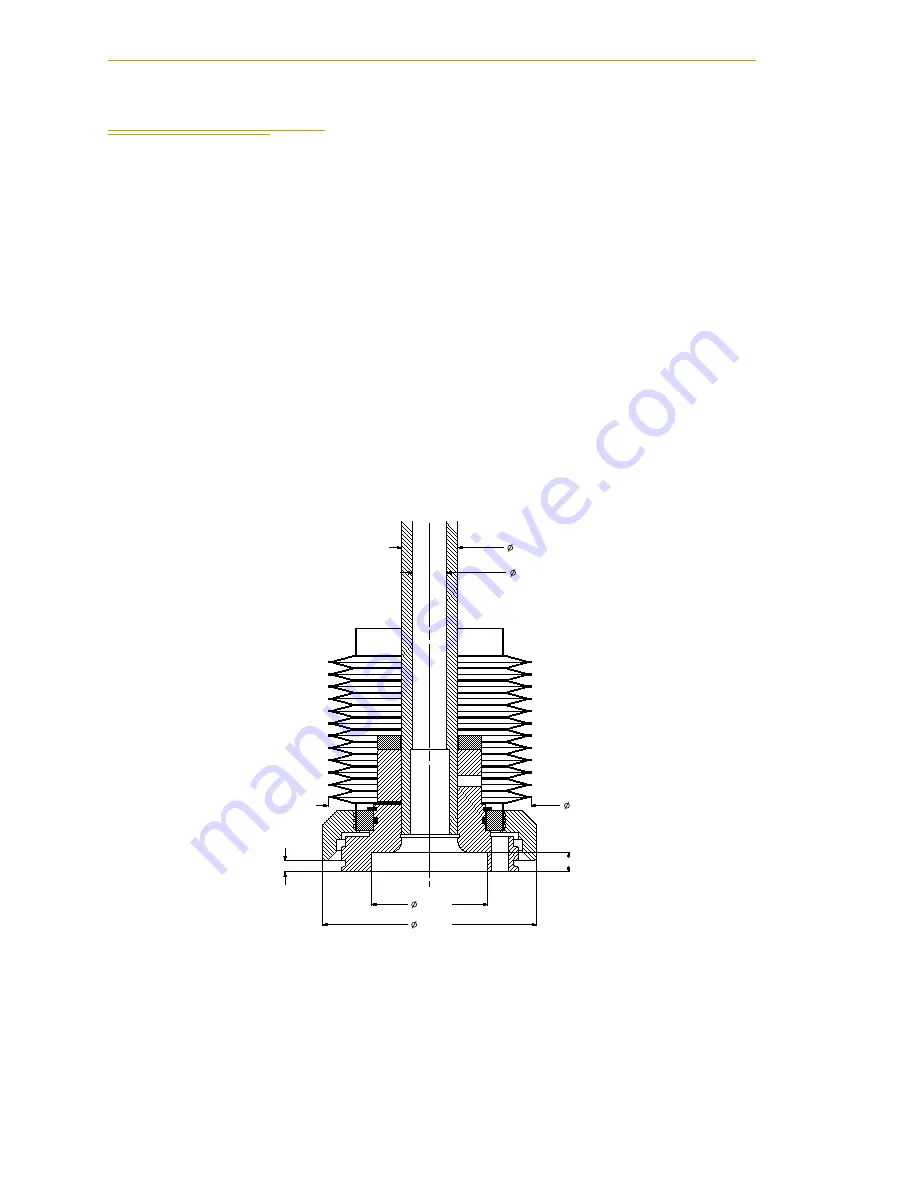
Chapter 10 - IP-65 Option
126
Adept Cobra s600/s800 Robot User’s Guide, Rev H
10.4 Customer Requirements
The IP-65 robot provides most of the hardware needed to achieve an IP-65 protection
level, but customers must provide a way of sealing the tool flange and pressurizing the
robot through the compressed air attachment fitting (located at the top of the robot).
These two requirements, sealing the tool flange and pressurizing the robot, are critical to
achieving the IP-65 level of protection.
In addition, the robot must be inspected periodically to make sure these requirements are
being met, as part of a periodic maintenance program.
Sealing the Tool Flange
The tool flange must be sealed so that the robot shell can be positively pressurized. The
positive pressure reinforces the sealing properties of the gaskets and seals provided in the
IP-65 robot.
The tool flange for the IP-65 robot has an additional protective shield on the outer edge
that is not present on the standard robot tool flange. See
for the side view
dimensions. The bottom face of the flange (mounting surface) is the same as the standard
flange, so the dimensions in
are correct.
Figure 10-10. Cobra IP-65 Tool Flange
12.0
72.2
20.0
76.2
3.8
6.8
41.15
Содержание Cobra s600
Страница 1: ...Adept Cobra s600 s800 Robot User s Guide...
Страница 2: ......
Страница 14: ......
Страница 20: ......
Страница 52: ......
Страница 68: ......
Страница 80: ......
Страница 116: ......
Страница 132: ......
Страница 146: ......
Страница 151: ......
Страница 152: ...5960 Inglewood Drive Pleasanton CA 94588 925 245 3400 P N 03017 000 Rev H...