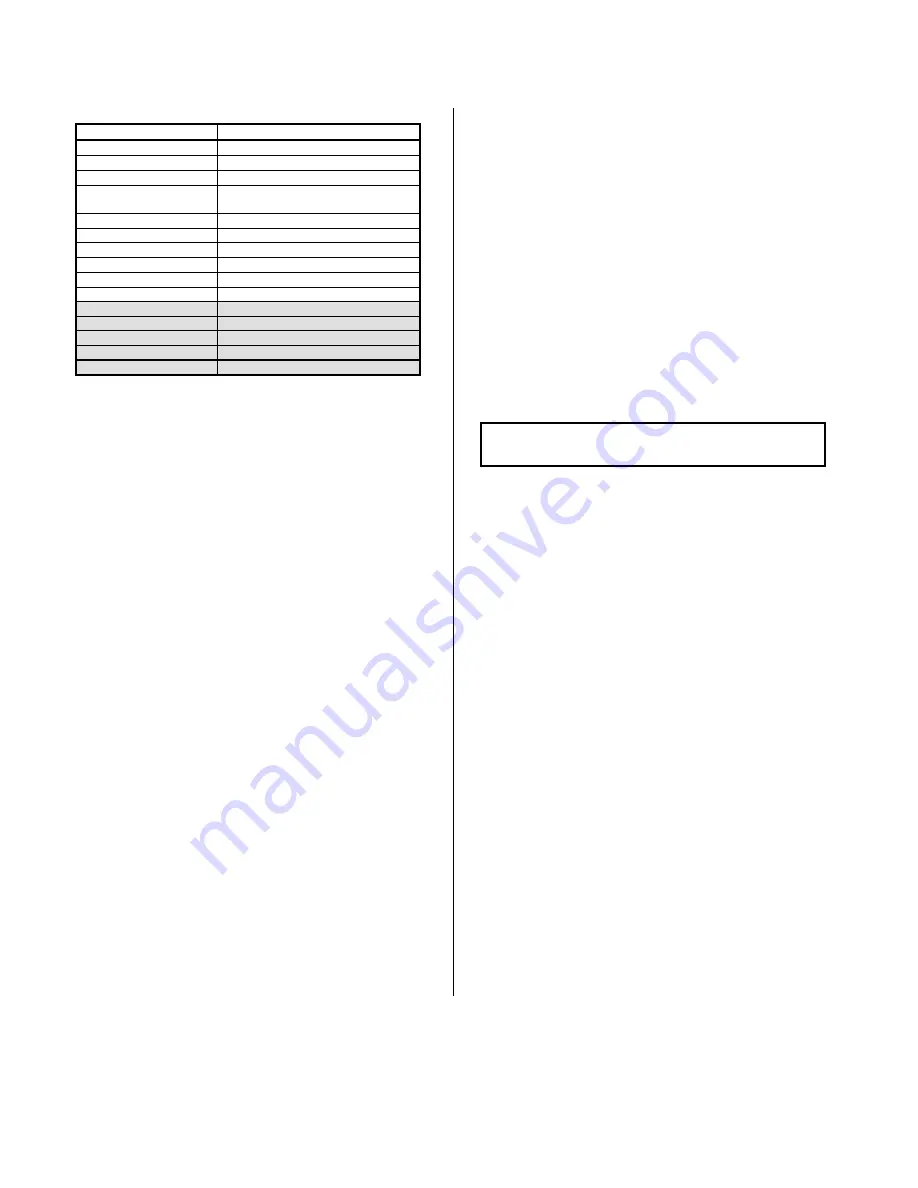
IntelliPack Series 841T Transmitter/Alarm User's Manual Frequency Input
___________________________________________________________________________________________
- 5 -
Table 2: 841T Default Factory Configuration
PARAMETER
CONFIGURATION/CALIBRATION
Input Range
Frequency 0 to 50KHz
Samples
1 (No Input Averaging)
Resistor
Pull-Up
Threshold
Bipolar 0.0V (zero crossing)
with +/-25mV Hysteresis
Event Debounce
5ms
Event Edge
Rising
Counter Termination
Auto-Reset
Output Range
0 to 10VDC (Jumper Installed)
Output Mode
Normal Acting (Ascending Signal)
Excitation Supply
8.2V (Use of excitation is optional)
Relay Mode & Setpoint
High Limit at 50KHz
Deadband
500Hz
Reset Type
Automatic Reset (Non-Latching)
Operating Mode
Failsafe
Relay Time Delay
100ms
Shaded entries apply to Model 841T-1500 units which also
include alarm functionality.
Your application may differ from the default configuration and
will require that the transmitter be reconfigured to suit your needs.
This is accomplished with Acromag’s user-friendly Windows
95
/NT
Configuration Program and Serial Port Adapter.
Configuration is normally done prior to field installation since field
configurability via the module’s push-buttons is generally limited
to zero, full-scale, setpoint, and dropout adjustments (frequency
inputs only). See the Transmitter Configuration Manual (8500-
570) for instructions.
Jumper Installation (For Voltage Output Only)
For voltage output, a short jumper must be installed between
the output “I+” and “JMP” terminals. A jumper wire is included
with the unit and is already installed between the output “JMP”
and “I+” terminals. Verify the position of this jumper if your
application requires output voltage. Remove this jumper for
current output applications. Refer to the Electrical Connections
Drawing 4501-683.
Mounting:
Refer to Enclosure Dimensions Drawing 4501-642 for
mounting and clearance dimensions.
DIN Rail Mounting:
This module can be mounted on "T"
type DIN rails. Use suitable fastening hardware to secure the
DIN rail to the mounting surface. Units may be mounted
side-by-side on 1-inch centers for limited space applications.
"T" Rail (35mm), Type EN50022:
To attach a module to this
style of DIN rail, angle the top of the unit towards the rail and
locate the top groove of the adapter over the upper lip of the
rail. Firmly push the unit towards the rail until it snaps solidly
into place. To remove a module, first separate the input
terminal block(s) from the bottom side of the module to
create a clearance to the DIN mounting area. Next, insert a
screwdriver into the lower arm of the DIN rail connector and
use it as a lever to force the connector down until the unit
disengages from the rail.
Electrical Connections
Terminals can accommodate wire from 12-24 AWG (stranded
or solid copper). Strip back wire insulation 1/4-inch on each lead
before installing into the terminal block. Input wiring should be
shielded twisted-pair. Since common mode voltages can exist on
signal wiring, adequate wire insulation should be used and proper
wiring practices followed. It is recommended that transmitter
output and power wiring be separated from the input signal wiring
for safety, as well as for low noise pickup. Note that input, power,
output, and relay terminal blocks are a plug-in type and can be
easily removed to facilitate module removal or replacement
without removing individual wires. If your application requires
voltage output, you must install a jumper between the output
“I+”
and “JMP” terminals (jumper is installed at the factory). Remove
this jumper for current output applications. Be sure to remove
power and/or disable the load before unplugging the terminals to
uninstall the module, installing or removing jumpers, or before
attempting service. All connections must be made with power
removed.
CAUTION:
Risk of Electric Shock - More than one
disconnect switch may be required to de-energize the
equipment before servicing.
1.
Power:
Refer to Electrical Connections Drawing 4501-683.
Variation in power supply voltage within rated limits has
negligible effect on module accuracy. For supply
connections, use No. 14 AWG wires rated for at least 75
C.
The power terminal is diode-coupled for reverse polarity
protection.
2.
Frequency or Pulse Counting Inputs:
Connect input(s) per
Drawing 4501-683. Observe proper polarity (see label for
input type). Excitation is provided at the input terminals. For
TTL or low-side transistor switches, use the on board pullup
resistor. For high-side transistor switches (open drain or
collector), use the on board pull-down resistor. For dry
contact switches, use the on-board excitation supply and pull-
up or pull-down resistors, as required.
WARNING:
If input frequency exceeds the full-scale beyond
110%, sample aliasing could cause measurement error and
generate false alarms. Limit the maximum frequency to less
than 110% of full-scale to avoid these errors.
3.
Analog Output Connections
: Wire outputs as shown in
Electrical Connections Drawing 4501-683. For voltage
output, you must also install a jumper between the output “I+”
and “JMP” terminals. Remove this jumper for current output.
Note:
For sensitive applications, high frequency noise may
be reduced by placing a 0.1uF capacitor directly across the
load.
4.
Output Relay Contacts (841T-1500 Only)
: Wire relay
contacts as shown in Electrical Connections Drawing 4501-
683. See the “Alarm Relay Specifications” for power
capacity. If necessary, an interposing relay can be used to
switch higher currents as illustrated in Interposing Relay
Connection Drawing 4501-646.