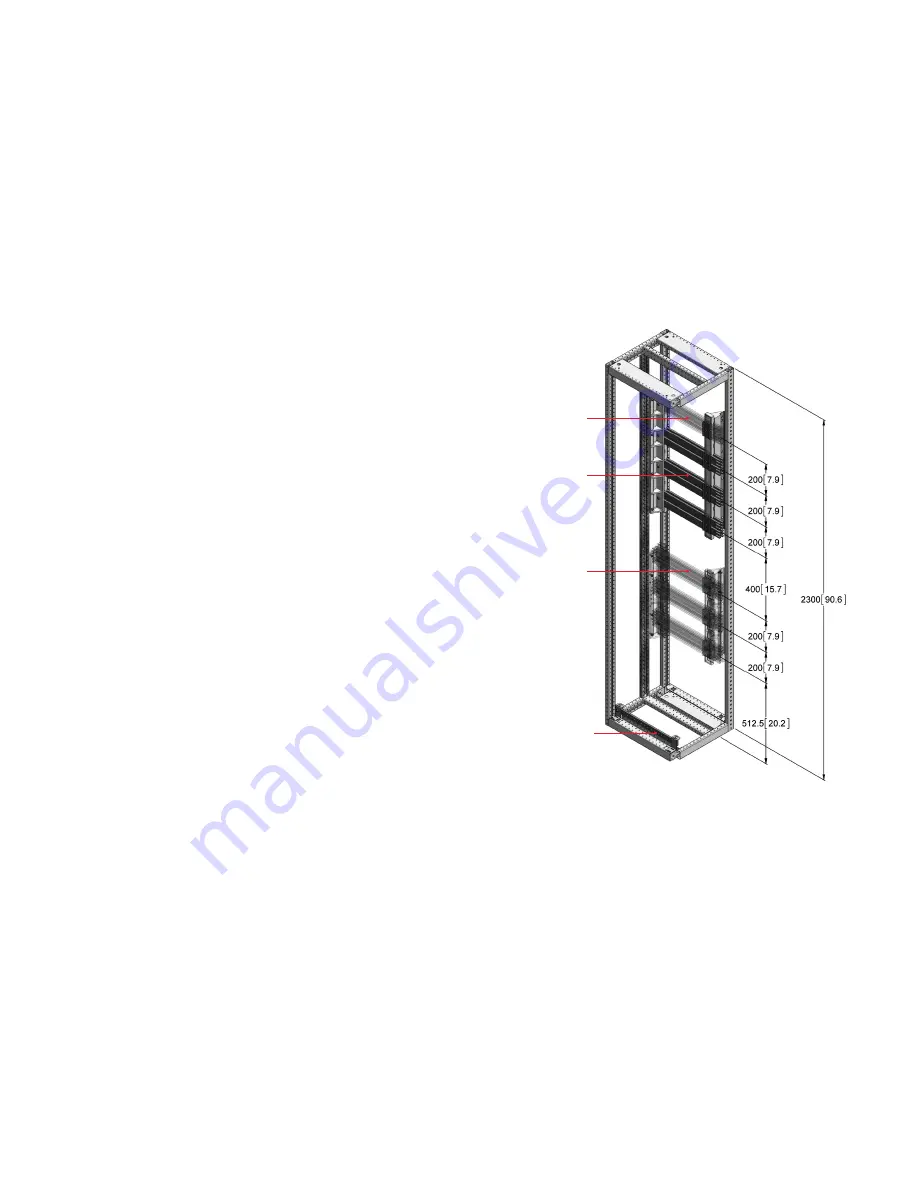
11
I N S TA L L AT I O N , O P ER AT I O N S A N D M A I N T EN A N C E M A N UA L
—
07
—
07 Horizontal bus bars
and ground bar
Bus bars systems may be configured in three or
four poles. See 1.7.2. Section - Horizontal neutral.
The horizontal bus bars are divided into lengths in
accordance with the length of the MCC section.
Sections in the same shipping split will be
connected at the factory. The shipping splits must
be connected together during installation using
the bus splice links provided on the right-hand side
of each split.
The splice link bolts must be tightened to the
specified torque. The bus splice links are accessible
through a barrier in the vertical wireway via a
removable transparent window. See Table 6.1.1.1.
Main bus splice links recommended torque
provided in this manual.
NOTE: It is necessary to routinely inspect splice link
connections. Check the torque indication via the
transparent shield inside the vertical wireway of
each section.
Main bus amperages include: 800A, 1200A, 1600A,
2000A and 2500A (non-ventilated), and, 3200A and
4000A (ventilated) configurations. Bus bracing is
available up to a maximum of 100kA@ 480V and
65kA @ 600V.
Horizontal bus is available in tin-plated copper and
silver-plated copper.
Horizontal neutral
A neutral bus is available as an option. It will be
located above “A Phase” at the top of the MCC,
rated 2,000A maximum.
Horizontal ground bar
A continuous, sectionalized, copper ground bus as
standard is provided at the bottom front or
optional at the top front of all sections, rated for
4000A. It´s available in tin-plated copper, silver-
plated copper and bare-copper finish.
The ground bus is provided with a series of regular
10 mm (0.39 in) holes for attaching ground lugs and
other conductors.
Ground the MCC ground bus using equipment
grounding conductors sized according to NEC
250-95, or by bonding to the raceway enclosing
the main supply conductors according to NEC
250-92(B).
See Fig. 7 (Horizontal bus bars and ground bar).
Main
horizontal
bus set
Second
horizontal
bus set
(when
required)
Horizontal
ground bar
Horizontal
neutral
bus
(Optional)
Содержание MNS-MCC
Страница 2: ......
Страница 50: ...50 MNS MCC LOW VOLTAGE MOTOR CONTROL CENTER ...
Страница 51: ......