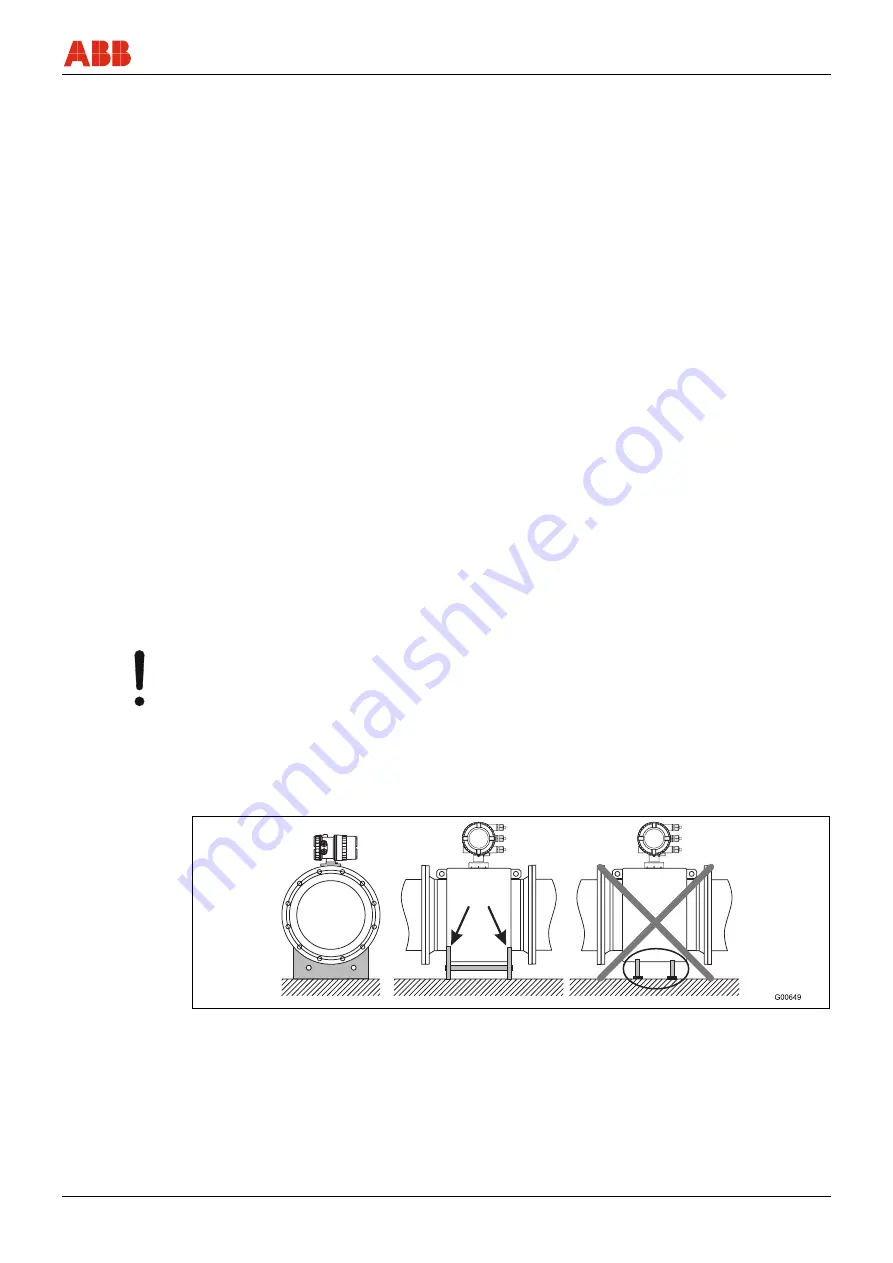
Installation
CI/FEP300/FEH300-EN
ProcessMaster / HygienicMaster
EN - 9
3 Installation
3.1
General information on installation
The following points must be observed for the installation:
• The flow direction must correspond to the identification if present.
• The maximum torque for all flange connections must be complied with.
• The devices must be installed without mechanical tension (torsion, bending).
• Install flange and wafer type units with coplanar counter flanges and use only appropriate
gaskets.
• Use only gaskets made from a compatible material for the fluid and fluid temperatures.
• Gaskets must not extend into the flow area since possible turbulence could influence the
device accuracy.
• The pipeline may not exert excessive forces or torques on the device.
• Do not remove the plugs in the cable connectors until you are ready to install the electrical
cable.
• Make sure the gaskets for the housing cover are seated properly. Carefully seal the cover.
Tighten the cover fittings.
• A separate transmitter must be installed at a largely vibration-free location.
• Do not expose the transmitter and sensor to direct sunlight. Provide appropriate sun
protection if necessary.
• When installing the transmitter in a control cabinet, make sure adequate cooling is provided.
3.1.1 Supports for meter sizes larger than DN 400
Notice - Potential damage to device!
Improper support for the device may result in deformed housing and damage to internal
magnet coils.
Place the supports at the edge of the housing (see arrows in the figure).
Devices with meter sizes larger than DN 400 must be mounted with support on a sufficiently
strong foundation.
Fig. 3: Support for meter sizes larger than DN 400
Содержание HART FEH300
Страница 2: ......
Страница 39: ...Appendix CI FEP300 FEH300 EN ProcessMaster HygienicMaster EN 37 ...
Страница 40: ...Appendix 38 EN ProcessMaster HygienicMaster CI FEP300 FEH300 EN ...
Страница 41: ......