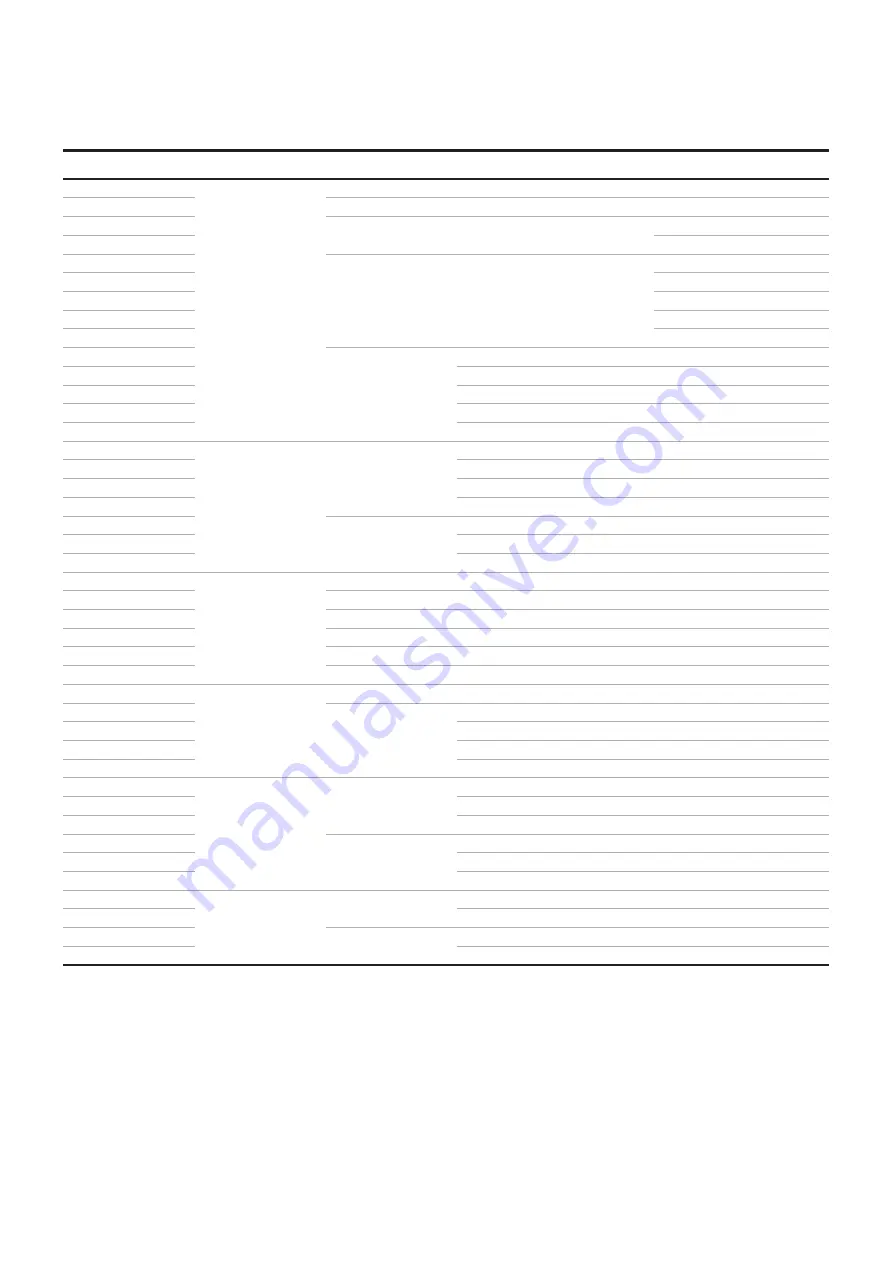
Level 1
Level 2
Level 3
Level 4
Level 5
Parameter
1
Control
Motor Control
External CT secondary
20
Control authority
Profibus option
19
Auto mode active
Soft local/ remote
19
Soft local/ remote
19
L hardwiring
R fieldbus
MD control
19
MD control
19
MD operator panel
MD in local
MD in remote
MD in auto Mode
0
MD in auto Mode
1
Grouping
Function
Direction
9
Group number
9
Start delay
9
Start delay
9
Communication
MODBUSRTU
4
Address
Parity
Redundancy
Baud rate
PROFIBUSDPV
15
Address
Mode
Block DP
Motor info
Motor type
Voltage
3
Frequency
Rated power
In
In (N2)
6
DI
Type
DI0 ~DI12 (24VDC) or
DI0-DI8 (110V or 240VAC)
Function
Contact type
Delay
21
Operation
22
DO
DO
1
Function
Delay
Principle
DO
23
Function
Delay
Principle
Maintenance
Running hour
Function
Alarm level
9
Start number
Function
Alarm Level
9
Note:
Items with marks will only display when they meet
corresponding conditions shown below.
0 9. O
P
ERATOR
P
ANE
L
MD
x
8
1
Содержание EM01
Страница 1: ... MANUAL Motor control and protection unit M10x User Guide ...
Страница 98: ......