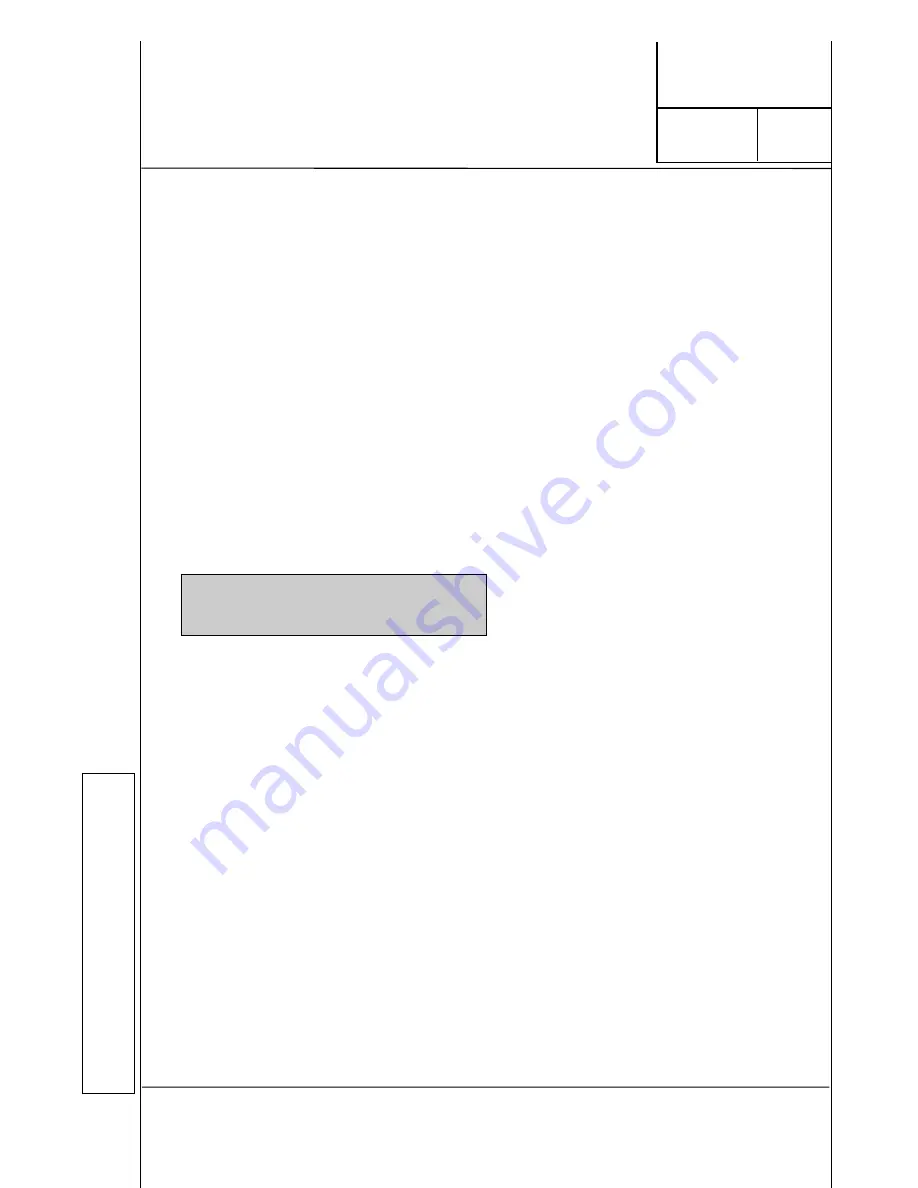
Installation, operation and maintenance instructions
High voltage flameproof motors for explosive atmosphere
AMD Rg 355-400-450-500
Rolling bearings maintenance and checking
Issued by: MOLM
Sheet No.
3AAM101040 E
Rev. B
01.2023
Page 1 of 11
We
res
er
ve
a
ll
rig
hts
in
this
doc
u
ment
an
d
in
th
e
in
format
io
n
cont
aine
d
ther
e
in.
R
epr
o
duc
tion,
us
e
of
di
sc
los
ur
e
to
thir
d
pa
rties w
itho
ut
expr
ess
auth
or
ity
is
s
trictly f
orbidd
en
.
Lubrication
Rolling
bearings
with
grease
lubrication
(horizontal and vertical machines)
Re-lubrication on the machines is foreseen in order to
ensure that new grease enters into the bearing, while
the old grease is eliminated by means of a regulator
(grease valve) the collection of an excessive quantity
of grease in the box (if present) is avoided.
All the information, including the bearing identification,
the quantity of grease, the re-lubrication frequency and
the frequency of old grease removal (when there is a
grease collection box) is indicated on the lubrication
plate attached to the machine. The machine is only to
be re-lubricated during rotation.
When the bearings are installed in the ventilation hubs
(side opposite the coupling) special grease feeding
tubes and used grease collection boxes are used.
The feeding tubes must always be filled with grease to
the maximum level to prevent condensation forming
when there is temperature fluctuation, so that no
moisture enters into the bearing and corrodes the
components in such cases it is better to use a grease
that gives good rust protection, even in extreme
environment
conditions
(low
temperatures,
temperature fluctuation, humidity).
NOTE
: Where installed, the used grease collection
box (under the outlet device) has to be emptied at
least once a year.
Use of greases
The lubrication frequency and the quantity of grease to
be injected, according to the most commonly used type
of bearings and the motor rotation speed, are given in
the tables 7-11.
In any case, check the specific motor data on the
maintenance instructions plate attached to the
machine for any special bearings or bearings that are
not indicated in the table. The values indicated refer to
normal operating conditions. If the machine is used in
dirty environments, lubrication has to be more frequent.
For temperatures higher than normal, the lubrication
frequency in relation to operating hours (indicated on
the maintenance instructions plate) has to be halved
for every 15° over the normally recommended value of
70°C.
The working temperature range for the recommended
lubrication greases is the following:
K2k or K3k lithium grease DIN 51825
Working temperature range: -20°C to +120°C.
DIN 51825 standards specify the minimum
physical/chemical properties for the lubrication
greases. All lubricant suppliers classify their products
and are able to suggest which is most appropriate. To
select the re-lubrication grease, bear in mind the
following:
For re-lubrication, only greases with the same
soap base as that already in the bearing are to be
used- Rolling bearings are filled in the factory with
a lubricating grease having a lithium soap base.
If it is necessary to use a lubrication grease with a
different soap base, first wash the bearings with
industrial benzene (SANGAJOL, VARSOL,
WHITESPIRIT) before filling with the new grease
to carry out this operation the bearings have to be
dismantled.
For re-lubrication, when possible use only grease
of the same manufacturer.
An increase in the temperature of the bearings for a
short time after re-lubrication is insignificant, since it is
caused by an excess of grease. During rotation the
grease regulator will quickly remove the excess
grease.
Automatic lubricators
Bearing regreasing intervals can be extended using
automatic lubricators. These units can be mounted
near the bearing itself and automatically provide to
grease substitution. They only need to be substituted
when empty, i.e. after emptying time. They are certified
to be used in hazardous areas (approval II 1 GD Ex ia
II C T6 T85 °C e I M 1 Ex ia I) with ambient
temperatures between -20 and +60 °C (-5 +140 °F).
Automatic lubricators for rolling bearings have to be
mounted on the machine and activated at machine
start up following these instructions:
1. Completely fill up grease feeding line to
bearing (with the same grease contained in
the unit or with a compatible one);
2. Mark installation date on unit envelope;
3. Remove the end cap of the lubricator;
4. Activate the lubricator rotating lubricator time
setting on the number corresponding to
dispense time (see lubrication plate)
5. Clean the area around lubricating point
6. Attach the new unit hand tight
7. Is recommended to check the general
condition of the bearing and correct lubricator
operation every quarter of the dispense time.
The lubricator has a delay time before starting to
dispense grease to the bearing. The delay vary
according to time setting and to ambient temperature:
at normal ambient temperatures grease dispensing
starts within a week from activation while at -20 °C (-5
°F) dispensing starts within 2 weeks. During activation
period, bearing lubrication is insured by the lubricant
contained in bearing housing.
Also grease flow rate is influenced by ambient
temperature. With temperatures below -10 °C (+14 °F)
emptying time will be approximately twice than setted
time; with temperatures above +40 °C (+104 °C)
emptying time is approximately half then setted time.
So, if ambient temperature is out from the range -10
+40 °C (+14 +104 °F) is necessary to correct lubricator