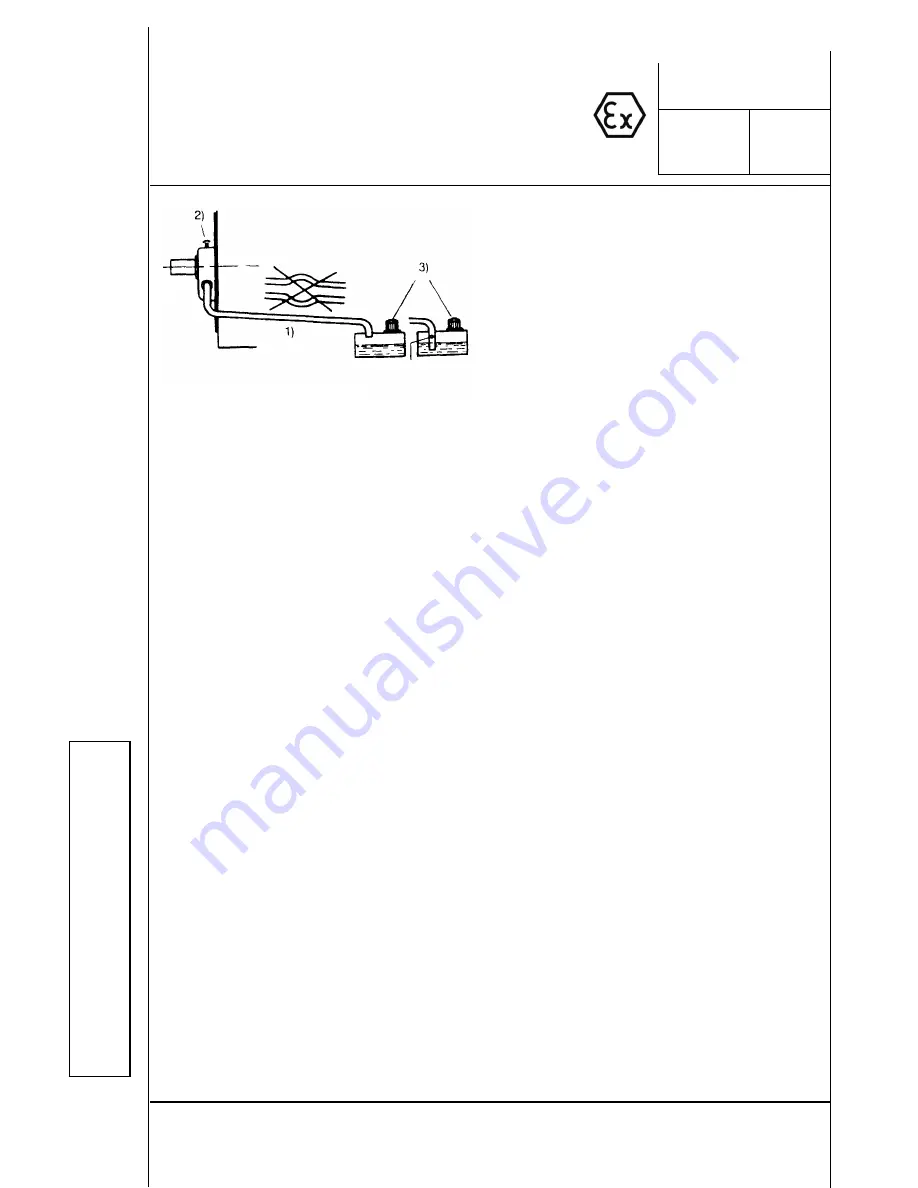
Installation, operation and maintenance instructions
High voltage flameproof motors for explosive atmosphere
AMD Rg 355-400-450-500
Preparation for commissioning – Mechanical steps
Issued by: MOLM
Sheet No.
3AAM101034 E
Rev. B
Page 2 of 2
01.2023
We
r
eserv
e
a
ll
righ
ts
i
n
this
docum
en
t
an
d
in
th
e
infor
m
atio
n
containe
d
th
er
e
in. Repr
od
ucti
on
, u
se
of
di
sc
los
ur
e
to
th
ird
part
ies
withou
t ex
pr
ess
aut
hori
ty
is
s
tr
ic
tly
for
b
id
de
n.
1) Return line
2) Vent
3) Oil vapour exhaust
In case of systems with a high oil flow (e.g. oil supply
systems), it may be economical to recondition the
lubricating oil for further use. In such cases, the oil
will require testing for physical, chemical and
mechanical properties during commissioning.
Appropriate data sheets with test instructions are
available from us on request.
SUGGESTION FOR DESIGN OF OIL SUPPLY
UNITS
The oil tank must be fitted with an oil vapour exhaust
to produce a negative pressure in the tank.
This negative pressure ensures that a back-
pressure of oil does not build up in the oil lines and
that the bearing enclosure is vented. At the same
time the oil will be “degassed” and separated from
the entrained air.
The oil tank must be fitted with a condensation
separator and, if required by low ambient
temperature, also with a heater. A suitable internal
protection against corrosion will help to avoid oil
contamination.
The oil return line must enter the oil tank above the
oil level (Var. A). Should the oil return line be
immersed, vent holes must be provided so that oil–
borne air can escape (Var. B).
The oil supply line must be located in such a way
that at no operating condition will the oil level fall
below it.
Filters must remove particles larger than 0.040 mm
and have a magnetic separator. If required for
operational reasons change-over double filters must
be fitted which can be cleaned during operation i.e.
without turning off the oil supply.
ABB cannot accept any responsibility for oil leakage
from the bearings or oil lines if the aforementioned
conditions are not fulfilled.
BEARING INSULATION.
The bearing insulation is at the customer’s request.
Machines of all sizes can be provided with insulated
bearings at both ends at the customer’s request.
Details on bearing insulation are given on a
separate sheet “Bearing insulation”, i.e. whether the
end-shield
or the
bearing shell
, one or both
bearings are insulated, and whether there is
provision for bridging the bearing insulation for test
purposes.
A
B