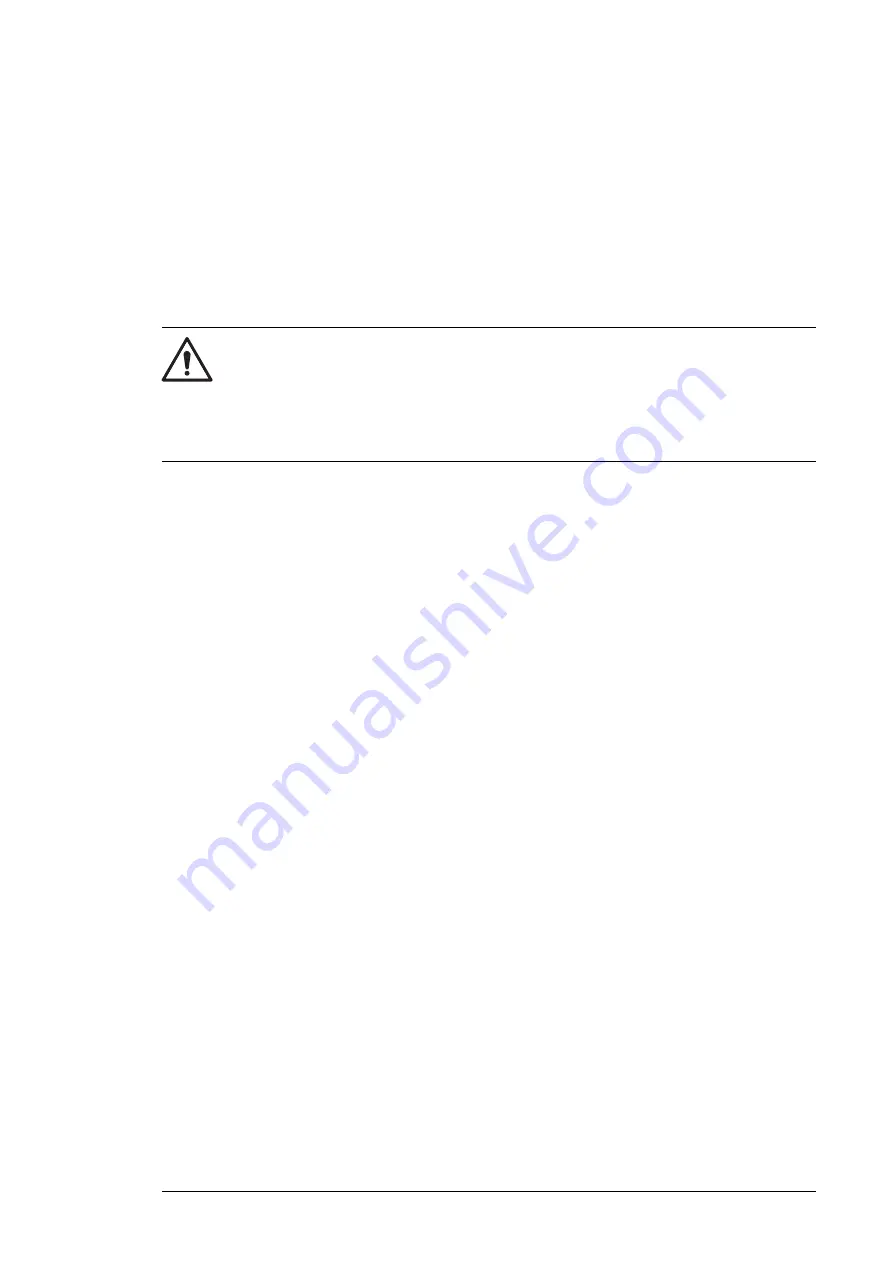
Placing the brake resistors
Install the resistors outside the drive in a place where they are able to cool effectively.
Arrange the cooling of the resistor in a way that
•
no danger of overheating is caused to the resistor or nearby materials, and
•
the temperature of the room the resistor is located in does not exceed the allowed
maximum.
Supply the resistor with cooling air or coolant according to the resistor manufacturer’s
instructions.
WARNING!
The materials near the brake resistor must be non-flammable. The surface
temperature of the resistor is high. Air flowing from the resistor is of hundreds of
degrees Celsius. If the exhaust vents are connected to a ventilation system, make
sure that the material withstands high temperatures. Protect the resistor against
contact.
■
Protecting the system in fault situations
A main contactor is not required for protecting against resistor overheating when the resistor
is dimensioned according to the instructions and the internal brake chopper is in use. The
drive will disable power flow through the input bridge if the chopper remains conductive in
a fault situation but the charging resistor may fail.
Note:
If an external brake chopper (outside the drive module) is used, ABB always requires
a main contactor.
■
Selecting the default brake system components
1.
Calculate the maximum power generated by the motor during braking.
2.
Select a suitable drive, brake chopper and brake resistor combination for the application
from the brake ratings table below. The braking power of the chopper must be greater
than or equal to the maximum power generated by the motor during the braking.
3.
Make sure that the resistor selection is correct: The energy generated by the motor
during a 400-second period must not exceed the resistor heat dissipation capacity
E
R
.
Note:
If the
E
R
value is not sufficient, it is possible to use a four-resistor assembly in
which two standard resistors are connected in parallel, two in series. The
E
R
value of
the four-resistor assembly is four times the value specified for the standard resistor.
■
Calculation example
Drive: ACS880-04F-582A-5+P943. Maximum continuous braking power (
P
brcont
) of the
internal brake chopper = 315 kW. Preselected ABB resistor = 2×SAFUR200F50. Braking
power of the motor is 300 kW. The duration of a braking cycle (T) is three minutes -> number
of braking pulses in 400 seconds = 2.2. The braking time (
t
br
) is 20 seconds.
P
br
= 300 kW <
P
brcont
= 315 kW. This is ok.
The energy generated by the motor during a 400-second period = 2.2 × 300 kW × 20 s =
13200 kJ. The brake resistor withstands an energy pulse of 10800 kJ in every 400 seconds
period. 13200 kJ > 10800 kJ. -> The resistor is too small. -> Decrease the braking power
or braking time or select a custom brake resistor as described in section
Resistor braking 187
Содержание ACS880-04FXT
Страница 1: ... ABB INDUSTRIAL DRIVES ACS880 04FXT drive module packages Hardware manual ...
Страница 2: ......
Страница 4: ......
Страница 40: ...40 ...
Страница 54: ...54 ...
Страница 82: ...82 ...
Страница 86: ...M10 86 Electrical installation ...
Страница 106: ...106 ...
Страница 114: ...FSO xx safety functions module connection X12 See the user manual of the FSO xx module 114 Control unit of the drive ...
Страница 118: ...118 ...
Страница 122: ...122 ...
Страница 132: ...132 ...
Страница 136: ...136 ...
Страница 158: ...158 ...
Страница 160: ...Standard configuration IP00 UL Type Open 160 Dimension drawings ...
Страница 161: ...Drive module with optional support brackets IP00 UL Type Open Dimension drawings 161 ...
Страница 162: ...Drive module with optional full size input and output power cable terminals and IP20 shrouds 162 Dimension drawings ...
Страница 163: ...Mounting plate opening 3AXD50000038119 Dimension drawings 163 ...
Страница 164: ...3AXD50000038119 164 Dimension drawings ...
Страница 182: ... Declaration of conformity 182 The Safe torque off function ...
Страница 183: ...The Safe torque off function 183 ...
Страница 184: ...184 ...