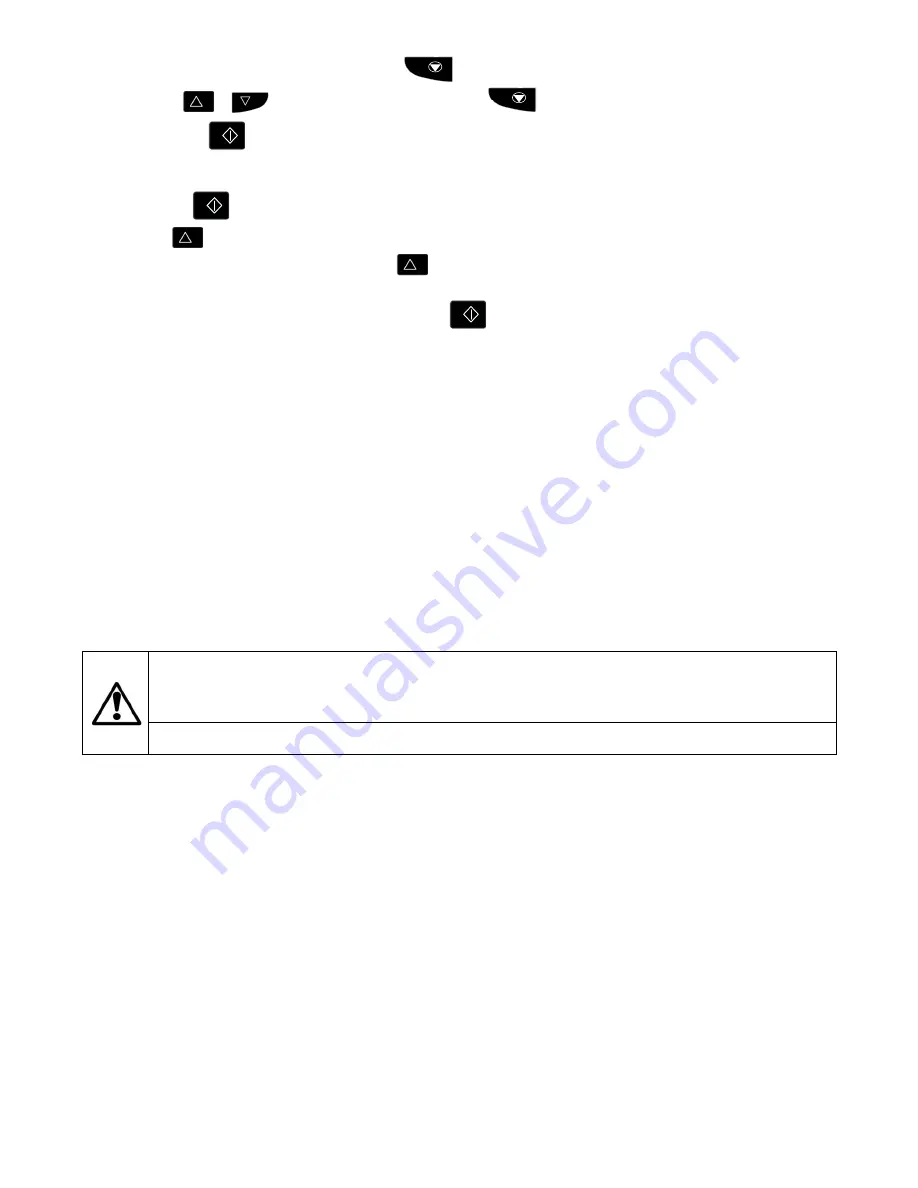
32
To preset a target speed prior to enable, press the
key whilst the drive is stopped. The display will show the target speed,
use the
&
keys to adjust as required then press the
key to return the display to
.
Pressing the
key will start the drive accelerating to the target speed.
To allow the ACS255 to be controlled from the keypad in a forward and reverse direction, set parameter 1103 =2:
Operation is the same as when parameter 1103=1 for start, stop and changing speed.
Press the
key. The display changes to
.
.
Press
to increase speed
The drive will run forward, increasing speed until
is released. Acceleration is limited by the setting in parameter 2202. The
maximum speed is the speed set in parameter 2008.
To reverse the direction of rotation of the motor, press the
key again.
7.3.
Sensorless Vector Speed Control Mode
ACS255 can be programmed by the user to operate in Sensorless Vector mode, which provides enhanced low speed torque, optimum motor
speed regulation regardless of load and accurate control of the motor torque. In most applications, the default Voltage Vector control mode will
provide adequate performance, however if Sensorless Vector operation is required, use the following procedure.
Enter the motor nameplate details into the relevant parameters as follows
o
9905 MOTOR RATED VOLTAGE
o
9906 MOTOR RATED CURRENT
o
9907 MOTOR RATED FREQUENCY
o
(Optional) 9908 MOTOR RATED SPEED (Rpm)
o
9915 Motor Power Factor Cos Ø
Select Sensorless Vector control mode by setting parameter 9903 MOTOR CONTROL MODE = 0
Ensure that the motor is correctly connected to the drive
Carry out a motor data Autotune by setting parameter 9910 MOTOR PARAMETER AUTO-TUNE ENABLE = 1
The Autotune will begin immediately when parameter 9910 MOTOR PARAMETER AUTO-TUNE ENABLE = 1 is set regardless of
the status of the drive enable signal. Whilst the autotune procedure does not drive or spin the motor, the motor shaft may still
turn slightly. It is not normally necessary to uncouple the load from the motor; however the user should ensure that no risk
arises from the possible movement of the motor shaft.
It is essential that the correct motor data is entered into the relevant drive parameters. Incorrect parameter settings can result
in poor or even dangerous performance.