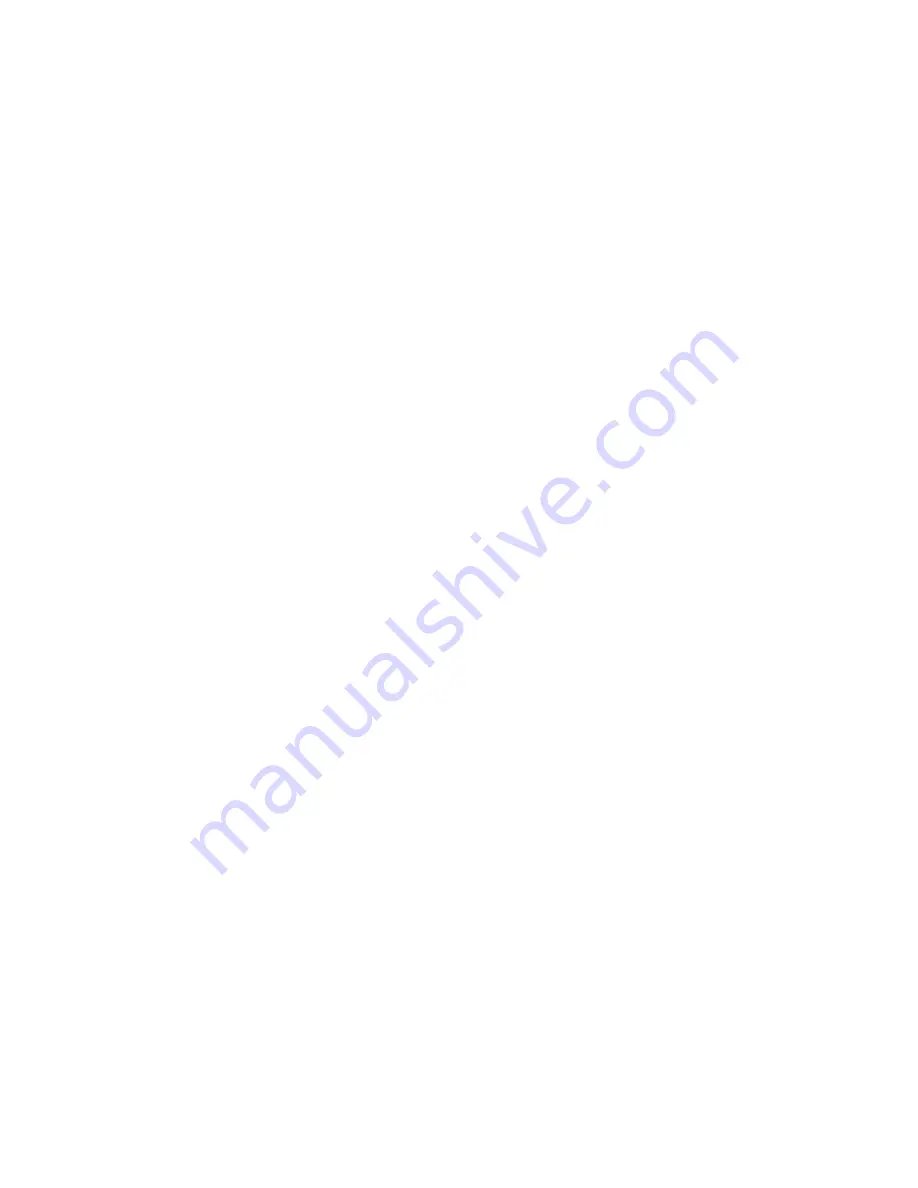
11
sequences and safety features associated with a gas ignition
control system. The system continuously performs various
diagnostic tests to verify proper appliance and control
operation. Should an unsafe condition occur, the control
will shut down the burner and display a red service light as
well as indicate the cause of the error on the display. The
operating programs for the system are stored in permanent
memory inside the microcontrollers. User-selectable operating
parameters and a history of detected faults are stored in
rewritable memory in the microcontrollers. A loss of power
does not affect either of the memories.
INPUTS TO MCB
TEMPERATURE SENSORS:
Temperature probes
(MCB - outlet and either inlet or tank are
required): The MCB accepts analog temperature inputs from
up to three sensors (inlet, outlet, and remote).
ECO input
(MCB - required): The ECo (energy cut off) is a hi-
limit switch located inside the outlet probe. It is a normally
closed switch that opens if the probe is exposed to a
temperature higher than the trip point. once tripped, the control
system needs to be manually reset.
Thermostat input
(MCB - optional): This input is set up to work with
an externally connected thermostat that provides a contact closure.
If this input is closed and everything else is in the proper state, a “call
for heat” condition will be initiated. These leads should be shorted
together when a thermostat is not being used. If it is desired that the
thermostat control the temperature of the boiler, the operating setpoint
of the system should be set higher than the temperature that the
thermostat is controlling. This will allow the thermostat to control the
boiler. When the thermostat closes, a call for heat will be generated
until the thermostat determines that the required temperature has
been reached.
AIR PRESSURE SENSORS (OPEN CONDITION INDICATES FAULT):
Blocked Flue
(MCB - required): Normally closed switch that opens
if the flue becomes blocked during operation.
Blower Prover
(MCB - required): Normally open switch that closes
when the air pressure produced by the blower is above the set point.
GAS PRESSURE SENSORS (OPEN CONDITION INDICATES FAULT):
Low Gas
(MCB - required): Normally closed switch that opens when
the gas pressure falls below the trip level. This input is enabled/
disabled by a dip switch on the MCB
Hi Gas
(MCB - required): Normally closed switch that opens if the
gas pressure exceeds a set value. This input is enabled/disabled
by a dip switch on the MCB.
WATER LEVEL SENSOR (OPEN CONDITION INDICATES FAULT):
Low Water Cut Off
(MCB - optional): Normally open switch that
closes when water reaches preset level. This input is enabled/
disabled by a dip switch on the MCB.
WATER FLOW SENSOR:
Flow
(MCB - required): Normally open switch that closes when
flow exceeds a set value.
FLAME SENSOR:
Flame
(MCB - required): Returns a signal to the microprocessor
if flame is detected on the burner. If the flame rod is missing or
shorted, the flame will not be detected.
OUTPUTS FROM MCB
RELAY CONTACT OUTPUT:
Alarm
(MCB - 24vAC - optional): Provides electrical power to
operate an external alarm. This can be an audio device (i.e.,
Sonalert), a visual device (lamp), or any other device that will
operate with the voltage and current level provided.
Pump
(MCB - 120vAC - required on systems that do not have
an external pump): Provides electrical power to directly operate a
pump or the coil of an externally connected contactor.
Blower
(MCB - 120vAC - required): variable speed blowers utilize
the high blower output only.
Igniter
(MCB - 120vAC - required): Provides power to operate
the HSI igniters.
Gas Valve
(MCB - 24vAC - required): Provides power to activate
the gas valve. The gas valve cannot be activated when the ECo
contacts are open.
Low Water Cut Off
(MCB - 24vAC - optional): Directly connected to
the 24vAC line to provide power to operate an external lWCo device.
MCB AND PDB INDICATOR LAMPS AND FUSES
A green lED is mounted on the PDB to indicate when line voltage
is applied (the PDB also contains a yellow and red lED, and a test/
run jumper that are used during installation to verify proper power
connections). A red lED on the MCB is used to indicate when the
24vAC input fuse has blown.
Yellow lEDs are located near the microcontrollers on the MCB.
These lEDs are “heartbeat indicators,” and blink approximately
twice per second to indicate that the microcontrollers are running.
MCB JUMPERS
The MCB has two jumpers. JP1 on the MCB is used to terminate
the external communications line. It is normally left off and installed
when the external cable is very long.
IGNITERS
The EMC modulation system operates with Silicon Carbide Igniters.
OPERATING SEQUENCE
1. The EMC modulation controller has four modes of operation:
Initialization, Standby, Running/Modulation, and Service. The
internal MCB micros control these modes through a sequence
of steps (or States) which are further described in the “UIM
operating Procedures” section.
2. When power is applied to the system, it enters the initialization
mode and the following automatic functions are performed:
• A. O. Smith opening screen is displayed.
• The system goes through a calibration indicated by the
green running lED blinking and then staying on; next the
red service lED and yellow standby lEDs come on, next
the service and runnings lEDs blink oN and oFF.
• Stored values are recalled from memory.
• Configuration dipswitches are read.
• Pending faults are recalled
• Micros on all boards start running (indicated by a flashing
Yellow lED near each micro)
• Input sensors are read
3. After initialization is complete (approximately 10 seconds)
the system turns the green lED off and goes to the standby
mode (yellow “Standby” lED on), unless a previously stored
fault has been recalled, which will send the system into the
service model (red “Service” lED on). In standby mode the
display shows the temperature screen and in fault mode the
current error screen is displayed.
4. The system then compares the temperature read from the
controlling probe (inlet or tank) to the setpoint temperature. If
Содержание VF VB 500
Страница 3: ...3 GENERAL SAFETY...
Страница 6: ...6 CONNECTION DIAGRAM...
Страница 7: ...7...
Страница 8: ...8 Figure 1 SCHEMATIC DIAGRAM VB VW 500 750 1000 SCHEMATIC DIAGRAM...
Страница 9: ...9 LIGHTING OPERATION INSTRUCTIONS FOR MODELS VB VW 500 750 AND 1000...
Страница 20: ...20 notes...
Страница 21: ...21 notes...
Страница 22: ...22 notes...