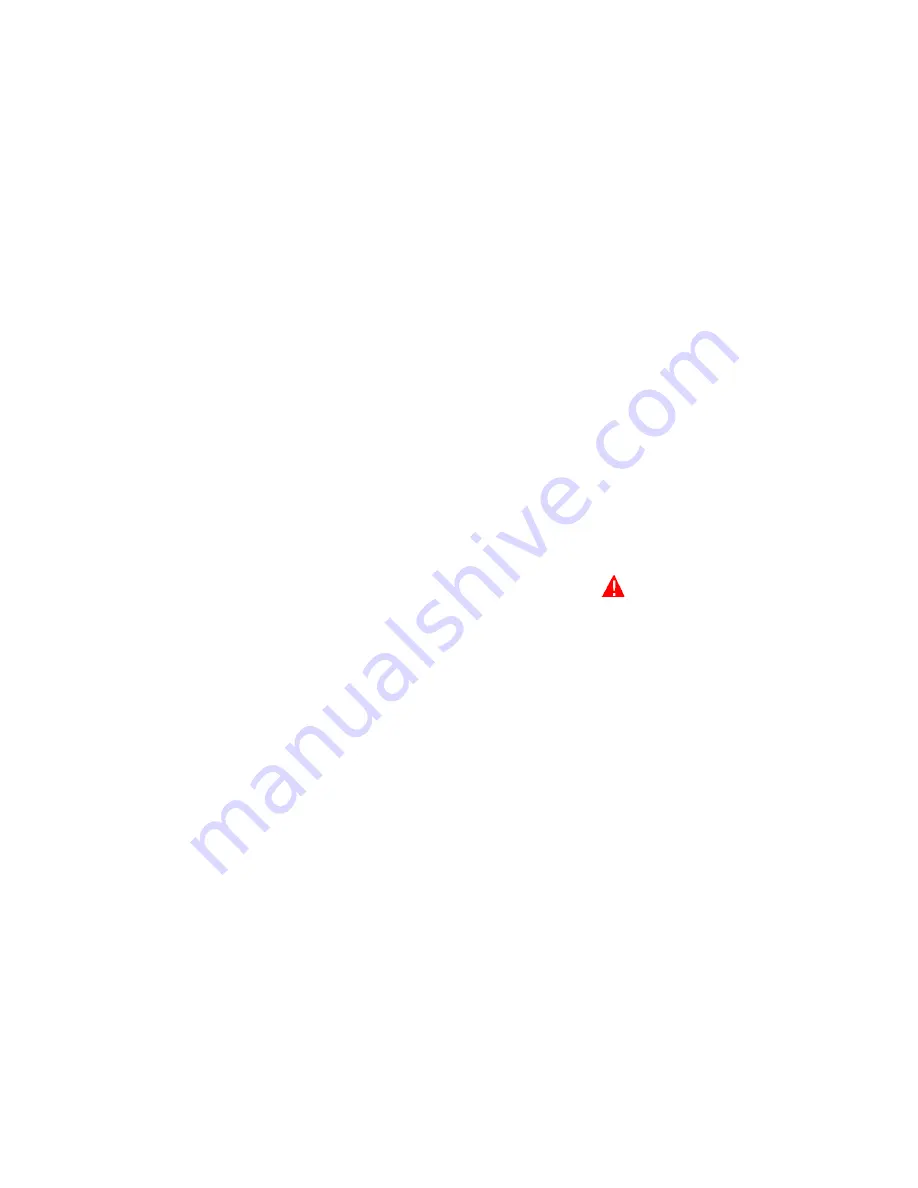
30
MOTOR WILL NOT RUN
1. Confirm 120V AC to the controller. Also, to verify correct polarity,
check for 120 V AC between hot supply and ground.
If there is no voltage, check for a loose connection where it
connects to the controller.
2. If there is 120 volts to the controller, check for loose connections
or a locked rotor. If the rotor cannot be freed the motor and
blower assembly must be replaced.
MOTOR RUNS, PREPURGE TIME ELAPSES BUT
MAIN FLAME NOT ESTABLISHED.
1. Check to see if main manual gas valve is open.
2. Check for a loose connection at the transformer, or a defective
transformer.
3. Check for a loose connection at the gas valve.
4. Check for open pressure switches or open reset button. Check
for blockage in the intake and exhaust venting or at the vent
hoods. If no blockage is found, check vinyl tubing for cuts or
crimps. If this tubing is damaged it must be replaced. If these
steps do not eliminate the problem, replace the pressure
switches.
5. Check to see if there is resistance across the igniter terminal
with an OHM meter. If there is no continuity, the igniter is broken
and should be replaced.
If the igniter appears to function properly, then verify that the
inlet pressure is 11.0" Natural Gas (2.74 kPa). The gas valve
supplied on this appliance is not designed to open against a
higher pressure. At this time also check that the inlet pressure
is not lower than the minimal gas supply pressure, as shown in
Table 4: that is, for Natural Gas, 6.2" (1.5 kPa) W.C. If the inlet
pressure is not within these limits then adjust the supply pressure
accordingly.
If the inlet pressure falls within the allowable limits, then verify
that the manifold pressure, when the gas is fully open, with the
heater running, is as called out in Table 4: that is, for Natural
Gas, 5.0" (1.25 kPa) W.C. If the manifold pressure is not correct
then adjust accordingly. See ADJUSTMENT PROCEDURE in
OPERATING INSTRUCTIONS selection, page 18, for the
manifold pressure adjustment procedure.
6. If the inlet and manifold pressures are within the limits specified
in step 5, then reset the appliance. Verify 24V AC at the gas
valve during the three (3) second ignition trial, after the igniter
reaches operating temperature. If 24V AC at the gas valve is
not seen during this period, the controller must be replaced.
If there is 24V AC at the gas valve during the four second ignition
trial and the manifold pressure does not increase above 0" W.C.
then verify that the manual gas control valve is in the “ON”
position (see page 20). If the valve is in the “ON” position and
the previous voltage and gas pressure conditions are met, then
the gas valve is defective and must be replaced.
Note that a positive manifold pressure reading of approximately
1.5" (.38 kPa) W.C. is normal during the prepurge portion of the
ignition cycle due to the location of the gas orifice.
MOTOR RUNS, BURNER LIGHTS MOMENTARILY,
THEN LOCKS OUT
1. Reset the appliance two more times to ensure that all of the air
has been purged from the gas line.
2. If the burner lights momentarily but does not sustain ignition,
verify that the inlet pressure is not greater than 11.0" (2.74 kPa)
W.C. or lower than the minimal gas supply pressure, as shown
in Table 4: that is, for Natural Gas, 6.2" (1.54 kPa) W.C. pressure.
Also, the manifold pressure should rise during the three (3)
second trial for ignition to the manifold pressure value for the
individual unit listed in Table 4: that is, for Natural Gas,
5.0" (1.25 kPa) W.C. If the manifold pressure is not correct then
adjust accordingly. See ADJUSTMENT PROCEDURE in
OPERATING INSTRUCTIONS section, page 18, for the manifold
pressure adjustment procedure.
3. Check for the reversed polarity in the supply wiring. This controller
is polarity sensitive. If the hot and neutral supply wires are
reversed, the controller will not sense flame. Reverse the supply
wires and try to fire the unit.
NOTE: Always turn off and disconnect main supply wiring before
servicing the unit.
4. Check connecting wire to the flame sensor. Verify that the flame
sensor has not been damaged in any way.
5. Verify that the air supply is adequate. The air inlet screen or
blower wheel may be restricted. Also, check the installation for
proper ventilation. See AIR REQUIREMENTS.
6. Check the venting system for the correct sizing, excess or
insufficient. See VENTING.
7. Check for a maximum inlet pressure of 11" Natural Gas
(2.74 kPa) W.C. and the manifold pressure as listed in Table 4:
that is, for Natural Gas, 5.0" (1.25 kPa) W.C. Please note that
the manifold pressure listed is the maximum value for the
manifold pressure. Do not set the manifold pressure higher than
the value shown for your heater in Table 4. Overfiring the heater
will result in rough ignition and/or noisy operation.
8. Confirm that the air inlet screen (see Figures 7 & 8) is free of
obstructions.
CAUTION
Do not reach into the burner housing or combustion chamber if the
heater is still hot. Allow the heater to cool and always use gloves
as the combustion chamber and the burner sleeve and housing
can become very hot after operation. Overfiring is a dangerous
condition that must be corrected immediately.
NOISY BURNER OPERATION
The exhaust of this unit produces some noise. This noise may be
objectionable if the exhaust terminal is located too close to the
opening of an occupied space. The noise may also be objectionable
if the exhaust is located in the confined space between two buildings
such as an alley or walkway. Since everyone's perception and
tolerance for background noise varies, there is no standard
recommendation. The best option when the noise is a concern is
to locate the exhaust as far away from any occupied spaces as
practical.
If noise becomes more than one can tolerate, a dampening muffler
is available through our Product Service Division. See
“REPLACEMENT PARTS” segment below.
GAS FAILS TO SHUT OFF
Check for defective gas valve or thermostat. If operation is incorrect,
replace.
REPLACEMENT PARTS
Replacement parts may be ordered through A.O. Smith dealers,
authorized servicers or distributors. Refer to the Yellow Pages for
where to call or contact the A.O. Smith Water Products Company,
5621 W. 115th Street, Alsip, IL 60803, 1-800-433-2545. When
ordering parts be sure to state the quantity, part number and
description of the items including the complete model and serial
number as it appears on the product. Refer to the parts list for
more information.