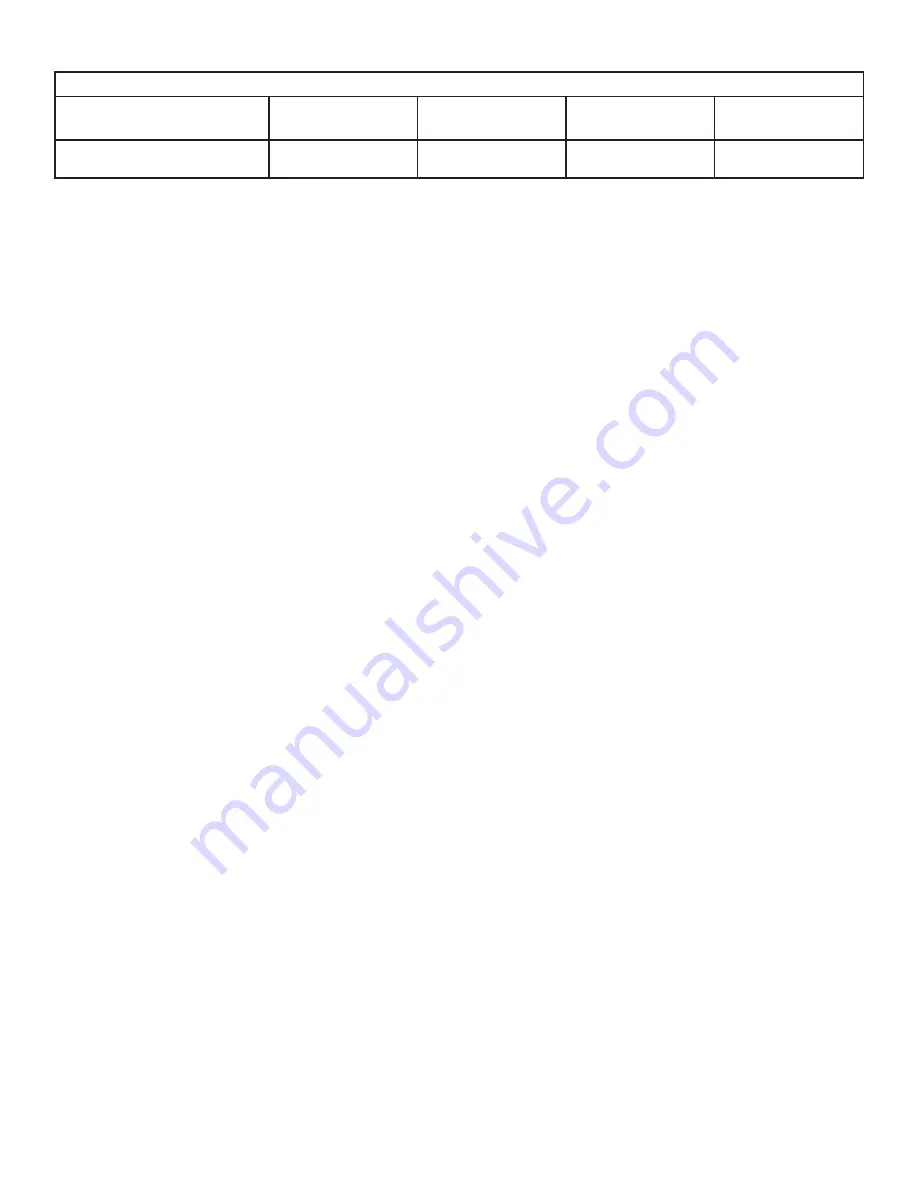
3-2
NOTE:
Have you read
“ Section 4”, PLUMBING SYSTEM CLEANUP,
for instructions on some procedures that may need to be performed fi rst?
GRAVEL AND CHEM-FREE MEDIA SCHEDULE
Unit Model Number
APIF100 Models
(APIF100, APIF100J, APIF100M,
APIF100PT, APIF100MPT, APIF100MJ)
APIF150 Models
(APIF150, APIF150J, APIF150M,
APIF150PT, APIF150MPT, APIF150MJ)
APIF200 Models
(APIF200, APIF200J, APIF200M,
APIF200PT, APIF200MPT, APIF200MJ)
APIF300 Models
(APIF300, APIF300J, APIF300M,
APIF300PT, APIF300MPT, APIF300MJ)
Filter Media
MC-10P
MC-10P
MC-050P
MC-10P (2)
MC-10P (3)
NOTE: If you ordered an “M” model Iron Reduction System, the fi lter pack media would be designated by an M at the end of the part number i.e. MC-10MP.
To load the fi lter media into the fi lter tank please use the follow steps. This is necessary to ensure that the distributor tube has not been pulled up when
the control valve was removed from the top of the fi lter tank.
Step 1
a) Remove from the shipping carton the fi lter unit
b) Carefully remove the control valve from the fi lter vessel by releasing the latch on the clamping collar (see fi gure 7 on 3-13).
c) Set all items aside for future use. Ensure that the following items have been shipped entirely with the unit to allow for proper and complete installation. If any
item is missing or has been damaged in transit contact our technical department for help and replacement at 866-693-2543 (option 1) from 7:30 am to
4:30pm EST. Please be prepared to supply the model and serial number when you call should you need help.
i. Control
valve
ii.
Media tank (also a reducing bushing and fl anged adapter on APIF300)
iii. Bypass
valve
iv.
1” Male NPT Connection Kit
v.
Media (amount will vary by fi lter size)
vi. Distributor
Tube
vii.
Drain line assembly kit
viii. Parts
bag
ix. Valve
wrench
x.
Installation and Operating Instruction
xi. Loading
funnel
xii.
Tube extension device and cap
d) Remove the distributor tube in the fi lter vessel, set aside and pour the gravel into a clean pail for later use.
e)
Reinsert the distributor tube into the fi lter vessel and ensure the tube is centered in the tank; a dimple is in the center of the fi lter vessel to help in doing so.
Using the tube extension device and cap, cover the distributor tube opening to prevent fi lter media and gravel from entering the distributor tube during the
loading of the fi lter vessel.
f) Place the funnel provided, in the opening of the media tank to aid in loading the gravel and fi lter media. Pour the QC gravel into the fi lter vessel slowly. While
holding the distributor tube in place, shake the fi lter vessel from side to side gently, to aid in leveling the QC gravel. Do not allow gravel to get under the basket
of the distributor tube during the loading of gravel. If this happens, pour out the gravel and remove the distributor tube once again. Next locate the fi lter media
and slowly pour into the fi lter vessel. Again shake the fi lter vessel from side to side to aid in leveling the media. Next, using a hose or clean pail, fi ll the fi lter
vessel with water to saturate the fi lter media and expel any air that may be present, remove the extension tube, cap and funnel, and save for future servicing.
g) Using a clean dry rag, wipe the opening of the media tank to remove any dust or residue from the opening to receive the control valve. Apply silicone lubricant
to the fi lter vessel fl anged opening and control valve O-rings that seal against the fi lter vessel and pilot tube O-ring in the center of the control valve. Place
the center of the control valve over the distributor tube and push down on the control valve until it contacts the fl ange on the fi lter vessel. Using one swift
and even push downward, seat the control valve into the opening of the fi lter vessel. Do not use a rocking motion to seat the control valve as this could roll
or pinch the O-ring, causing a leak between the control valve and fi lter vessel. Place the clamp assembly around the fl ange of the fi lter vessel and the control
valve, paying particular attention to the proper orientation of the clamp. To secure the clamp in place install the latch. Refer to Figure 7 on 3-12 to determine
the proper orientation for the clamp. The latch needs to be installed with the smaller opening toward the clamp. Attach the bypass to the control valve as
shown in Figure 7 on page 3-12
.
Step 2
Shut off water at main supply. On a PRIVATE WELL SYSTEM turn off the power to the WELL PUMP and drain PRESSURE TANK. Make certain all water pressure
has been relieved from complete water system by opening nearest faucet to drain water system. SHUT OFF FUEL SUPPLY TO WATER HEATER OR BOILER.
Step 3
Cut main supply line as required to fi t Hydro-Charger in plumbing between well pump and pressure tank (Hydro-Charger may be installed in a vertical or
horizontal position). The Hydro-Charger has been supplied with both 1” threaded and 1” barbed (insert) fi ttings to allow for installation with various types of
piping materials. When using the threaded nipples, use thread tape only. When using barbed (insert) fi ttings, appropriate pipe clamps must be used. Once
installed the quick release nipples allow the Hydro-Charger to be rotated, so the air draw adjustment screw is accessible for adjustment by a small bladed
screwdriver. Allow at least 10 inches of straight run of 1” pipe on both INLET and OUTLET side of the Hydro-Charger. Refer to Figure 2 for correct assembly.
The quick release nipples also acts as a union to facilitate the Hydro-Charger removal, inspection and cleaning as needed. With an installation on PVC pipe
and copper tubing it may require the addition of a normal plumbing union to aid in removal from the plumbing due to the rigidity of that type of material. Make
certain the directional arrows on the Hydro-Charger points toward the pressure tank and the pressure control switch is located on the pressure tank side
of Hydro-Charger as in Figure 1. Rapid cycling of pump may occur if the pressure control switch is located on well side. If a check valve is located between
hydrocharger and pressure tank, it may prevent the Hydro-Charger from performing properly. Relocate to well side of Hydro-Charger.
Содержание APIF100
Страница 2: ......
Страница 22: ...3 13 Figure 10 Figure 11 Figure 8 Figure 9 ...