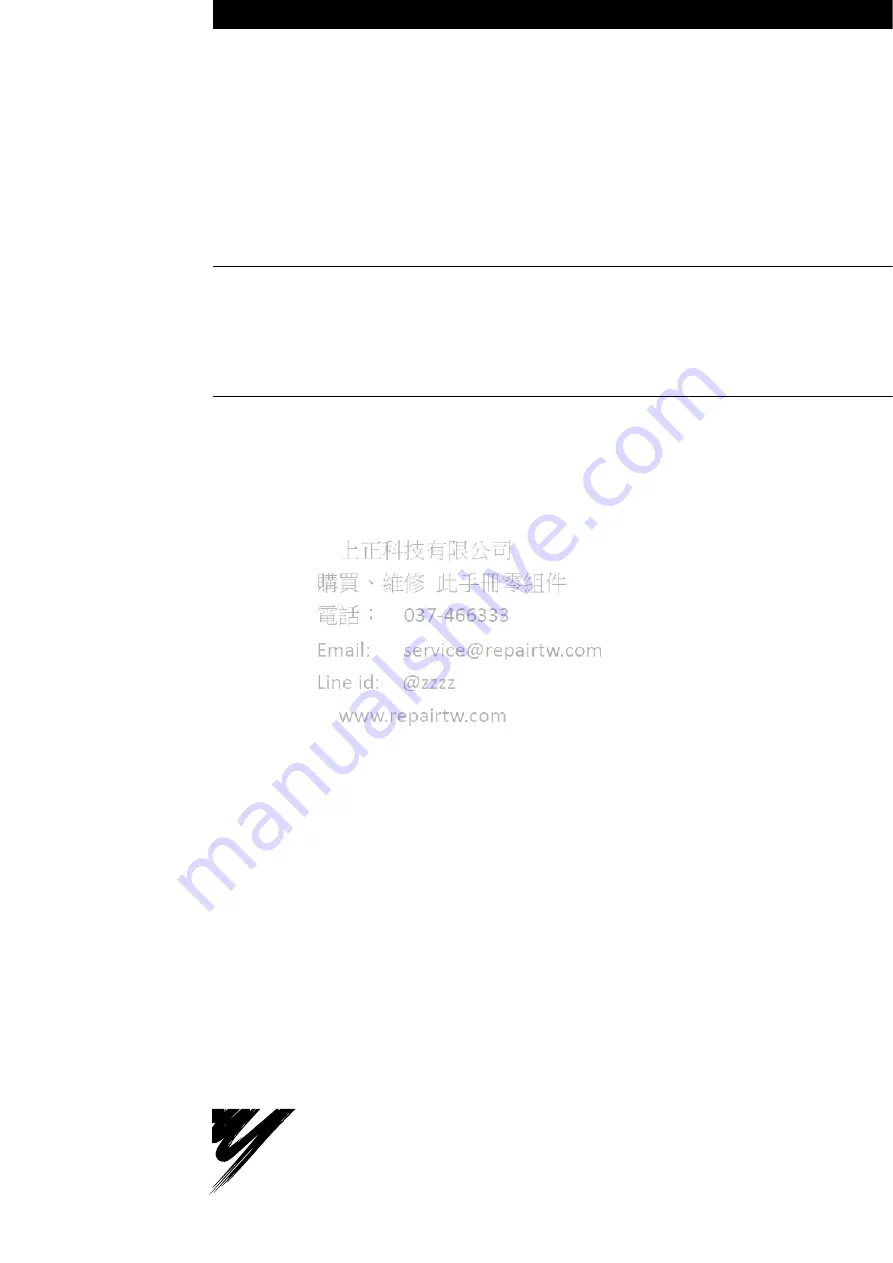
YASKAWA
形式
(Type)
:
SGDP-
□
PA
(位置制御用)
(for position control)
YASKAWA
株式会社
安川電機
資料番号
(MANUAL NO.)
TOB-S800-33.10
この取扱説明書は, 最終的に本製品をお使いになる方のお手元に確実に届けられるよう, お取り
計らい願います。
Upon receipt of the product and prior to installing the product, read these instructions
thoroughly, and retain for future reference.
取扱説明書
INSTRUCTIONS
∑-Ⅱ
PLUS SERIES AC SERVOPACK SGDP