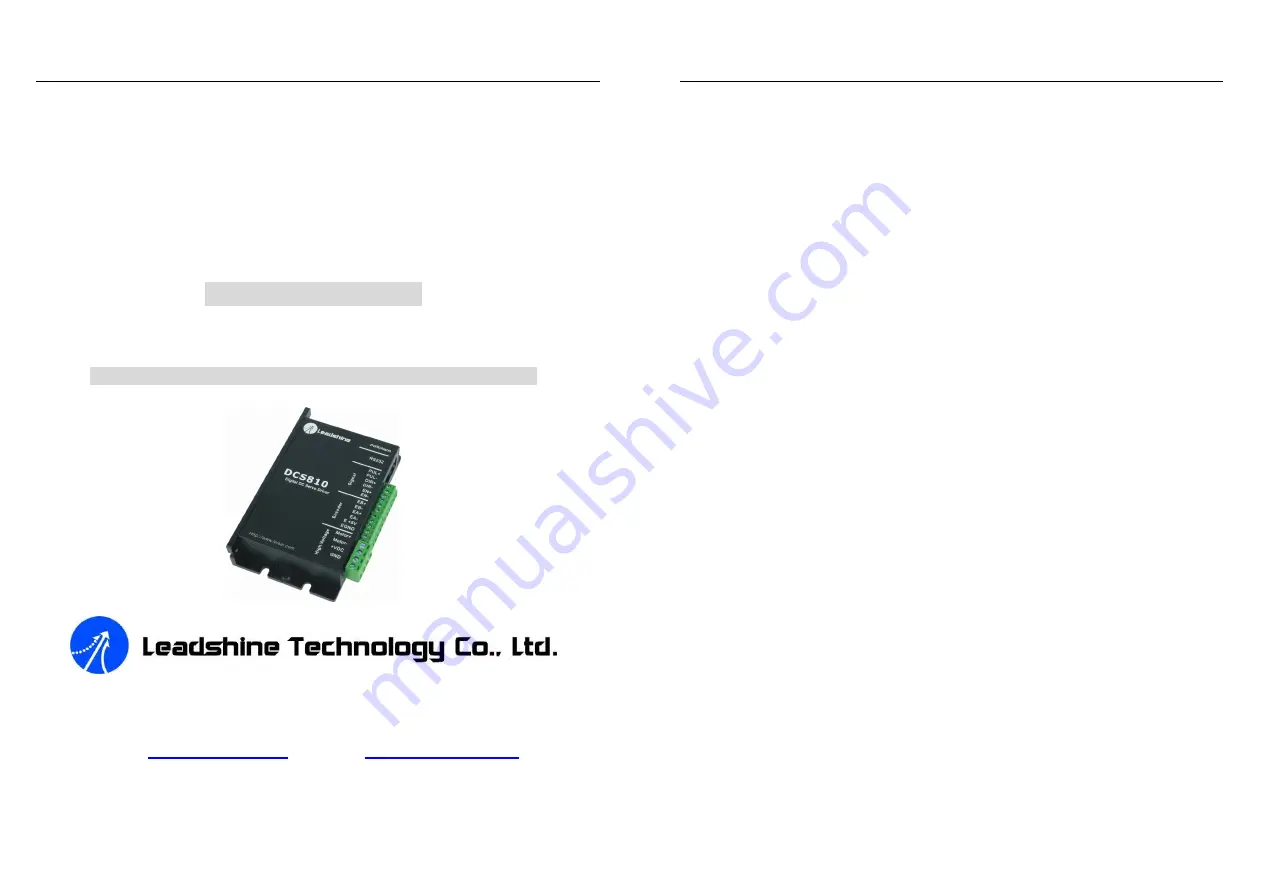
User
’
s Manual
For
DCS810V2
Digital DC Servo Driver
Revision 1.0
©
2009 All Rights Reserved
Attention: Please read this manual carefully before using the driver!
3/F, Block 2, Nanyou Tianan Industrial Park, Nanshan Dist, Shenzhen, China
Tel: (86)755-26434369 Fax: (86)755-26402718
URL:
The content in this manual has been carefully prepared and is believed to be accurate,
but no responsibility is assumed for inaccuracies.
Leadshine reserves the right to make changes without further notice to any products
herein to improve reliability, function or design. Leadshine does not assume any
liability arising out of the application or use of any product or circuit described
herein; neither does it convey any license under its patent rights of others.
Leadshine
’
s general policy does not recommend the use of its products in life
support or aircraft applications wherein a failure or malfunction of the product may
directly threaten life or injury. According to Leadshine
’
s terms and conditions of
sales, the user of Leadshine
’
s products in life support or aircraft applications
assumes all risks of such use and indemnifies Leadshine against all damages.
©
2009 by Leadshine Technology Company Limited.
All Rights Reserved