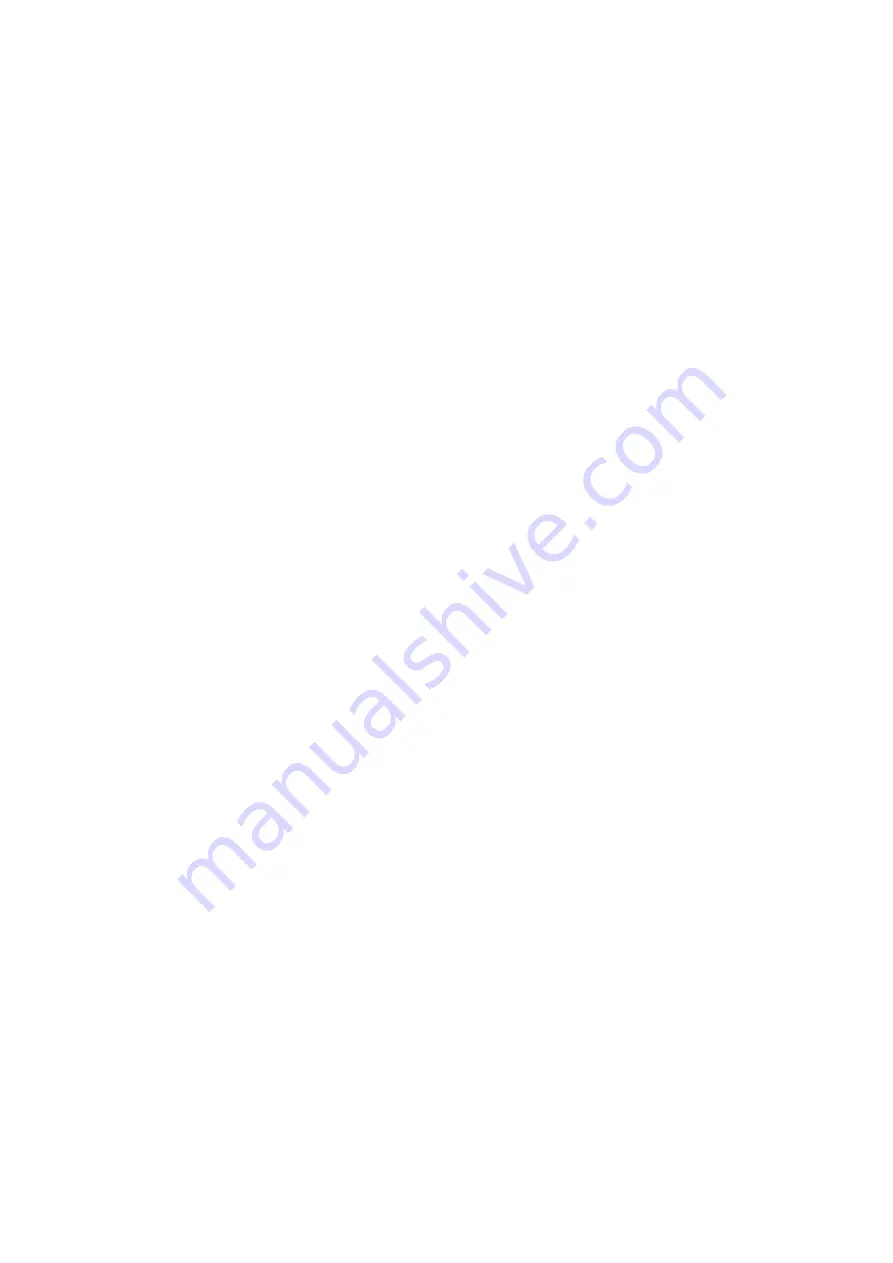
7
Maximum supply voltage ripple
5 %
Maximum transmitter power demand
560 mW
Insulation resistance
20 M
Ω
at 50 V DC
Insulation strength
50 V DC
Operational environment temperature
-25 °C to +60 °C
Operational environment temperature - extended range -25 °C to +70 °C
(additional on demand)
Dimensions
ø 40 x 25 mm
c) Type DCPT3 active current transmitter. Power supply to the current loop is not a part of the actuator. Maximum
loading resistance of the loop is 500
Ω
. For variants
MODACT MTN, MTP Control with the regulator ZP2.RE5, it is
used as a position sensor.
DCPT3 can be easily set by two push-buttons with LED diode on the transmitter body.
Technical parameters of DCPT3:
Scanning of position
contact-less magneto-resistant
Working stroke
adjustable 60° – 340°
Non-linearity
max. ±1 %
Loading resistance
0 – 500
Ω
Output signal
4 – 20 mA or 20 – 4 mA
Power supply
15 – 28 V DC, < 42 mA
Working temperature
-25 °C to +70 °C
Dimensions
ø 40 x 25 mm
For the transmitters CPT 1Az as well as DCPT3, a two-wire connection is used, i.e., the transmitter, the power
supply and the load are connected in series. The user should secure that the two-wire circuit of the current transmitter
is connected to the electric earth of the associated regulator, computer, etc. This connection should only be made
at a single point in any section of the circuit, outside the actuator.
Position indicator
The actuator is fitted with a local position indicator
.
Anti-condensation heater
The actuators are fitted with an anti-condensation heater preventing condensation of water vapour. It is connected
to the AC mains of voltage 230 V.
Local control
Local control serves for controlling the actuator from the site of its installation. It includes two change-over switches:
one with positions “Remote control - Off - Local control”, the other “Open - Stop - Close”.
The former change-over switch can be built-in as two-pole or four-pole. The change-over switches are installed
in a terminal-board box and the control elements on the lid of this terminal-board box.
Position regulator
The position regulator built-in in the actuator enables to control position of the output shaft of the actuator and thus
also the valve by the input analog signal.
The control unit is microprocessor-based programmed for regulating the actuator, ascertaining and repairing error
conditions, and for simple setting of regulation parameters.
The regulator design enables to switch off the regulator feeding. If the regulator is not under voltage it does not
regulate but, after its feeding is switched on, the regulator function is automatically restored; the parameters and
diagnostic data stored in the regulator memory are retained.
The regulator circuits compare the input signal with the feedback signal from the position transmitter of the actuator
output shaft. If there is a difference between the input and feedback signals the regulator closes one of the built-in
contactors in the actuator so that the actuator shaft is reset to the position corresponding to magnitude of the input
signal. When the feedback signal is equal to the input signal the actuator stops.
The control parameters are set by functional push-buttons on the regulator or by PC connected to the regulator via
a serial interface for the period of setting the parameters or during the communication module .
Dynamic brake
The brake is an optional accessory to the actuators
MTN, MTP Control. After opening the contactor, it induces
dynamic braking moment in the electric motor lasting for several tenths of second. It reduces dramatically the run-down
time and regulation is thus more precise. When the actuator is in a standstill no braking moment is exerted.
The actuators without regulator are fitted with autonomous brake
BAM-002. For its function, it requires
auxiliary contacts of the contactors and auxiliary contact of the over-current relay. It is dimensioned for electric
motors 3 x 230 / 400 V, output up to 550 W.