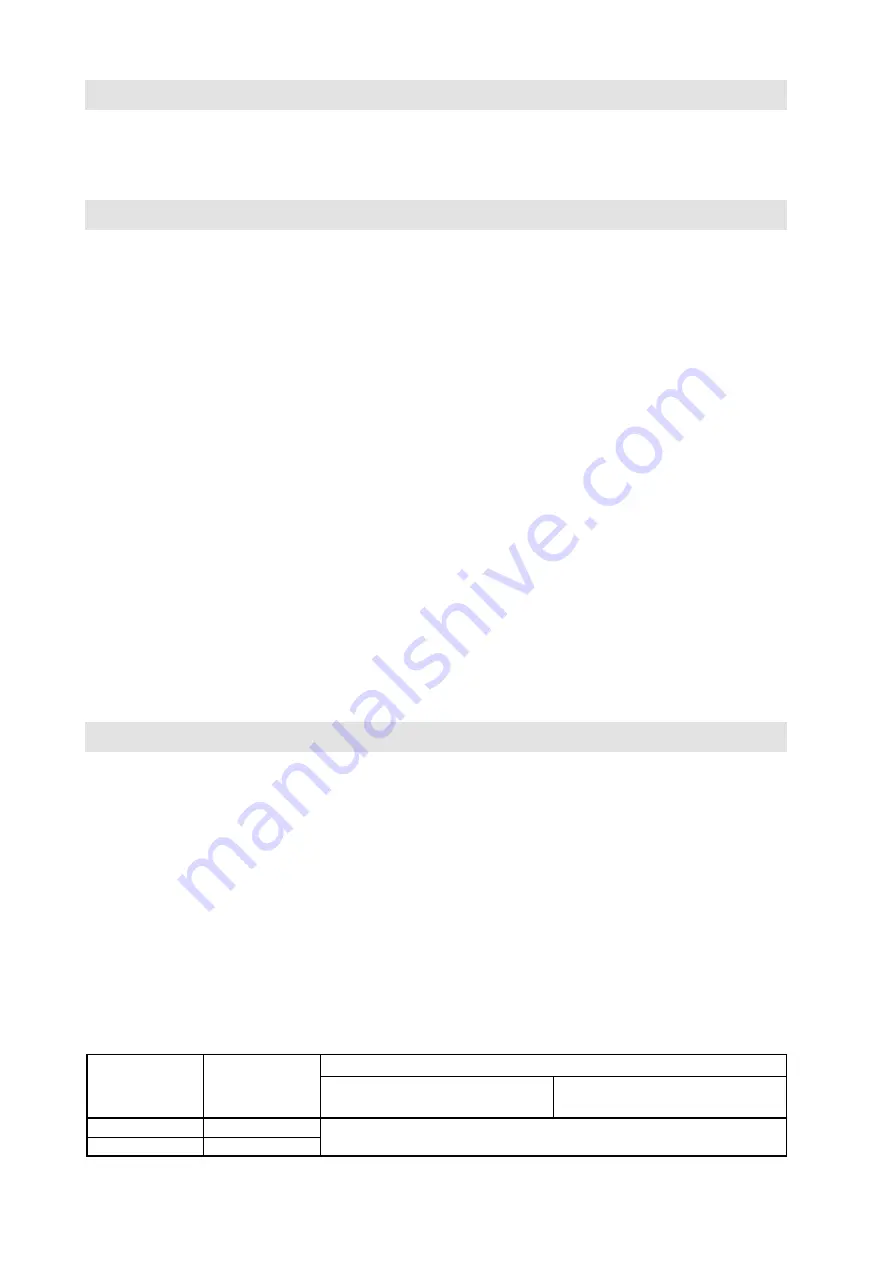
19
10. ATTACHMENT TO A VALVE
Place the actuator on the valve so that its output pull-rod can be connected to the output pull-rod of the valve.
Attach the actuator to the valve and check the attachment by rotating the handwheel. Remove the terminal box cover
and wire the actuator, according to the internal and external circuit layouts.
11. ADJUSTMENT OF THE ACTUATOR WITH A VALVE
After placing the actuator on the valve and checking its attachment, the following adjusting procedure should be used:
1) Bring the actuator into an intermediate position by the hand.
2) Connect the actuator to the AC mains and check the correct sense of output pull-rod movement. When viewing into
the control box, the output shaft should rotate clockwise while the pull-rod is moving in the CLOSE direction and
shifting out.
3) Move the actuator electrically near the CLOSE position and complete the adjusting operation by setting the actuator
precisely to the CLOSE position, employing the handwheel. In this position, set the position-limit switching unit
(CLOSE position-limit microswitch PZ)
and the potentiometer position transmitter, according to Points 3e and 3d,
respectively.
4) Bring the pull-rod of the actuator to the position in which the CLOSE signalling switch
(SZ)
should change over.
Adjustment of the CLOSE signalling switch
(SZ)
should be made, according to Point 3b.
5) Move the output pull-rod of the actuator by the required amount of working stroke and set the OPEN position-limit
switch
(PO)
and the potentiometer position transmitter, according to Point 3e and 3d, respectively. The position
adjustment of the position-limit and signalling switches as well as the position transmitter should be checked
repeatedly.
6) Bring the output pull-rod into the position in which the OPEN signalling switch
(SO)
should change over. Adjust
the OPEN signalling switch
(SO)
, according to Point 3b.
Caution!
The control box cover should be removed so that it is displaced in the direction of extended axis of the actuator output
shaft, taking care to avoid any damage to the position indicator. When mounting the valve on a pipeline, the valve
should be brought into the midway position by means of the handwheel. By starting the actuator for a short time, check
that it rotates in the correct direction. If this is not the case, the two phase conductors should be mutually interchanged
on the terminal board.
12. OPERATION AND MAINTENANCE
Depending on the operating conditions, the operation of rectilinear actuators usually involves only the transmission
of pulses, as required for the individual functions. In the event of a power supply failure, readjust the controlled device
by the handwheel. If the actuator has been connected in the circuit of automatic equipment
(which does not imply
the control mode)
, it is advisable that manual remote control units are connected in the circuit so that the actuator can
be controlled even if a failure of the automatic equipment occurs. It is the operator’s duty to ensure that the actuator is
given the specified maintenance attention and is protected against the harmful effects of ambient and climatic
conditions not included in the Clause “Operating conditions”.
The actuators are lubricated with plastic consistent lubricants.
The types of lubricant and amounts are listed in
the table.
For lubrication of drive units use plastic consistent lubricants.
Lubricants in the drive units supplied are designed to last the entire useful life of the unit.
During the time when the drive units are in use, it is not necessary to change or monitor the amount of
the lubricant.
The actuators with plastic lubricant are labelled
“Filled: solid grease”
on the power box at the side of the hand-wheel.
52 442
0,30
52 443
0,50
Type number
of drive unit
Amount of lubricant
(kg)
T1
(-25 – +70 °C)
CIATIM – 201 GOST 6267-74
CIATIM – 221 GOST 9433-80
U1
(-40 – +55 °C)
Type of lubricant for specific climatic conditions and temperature