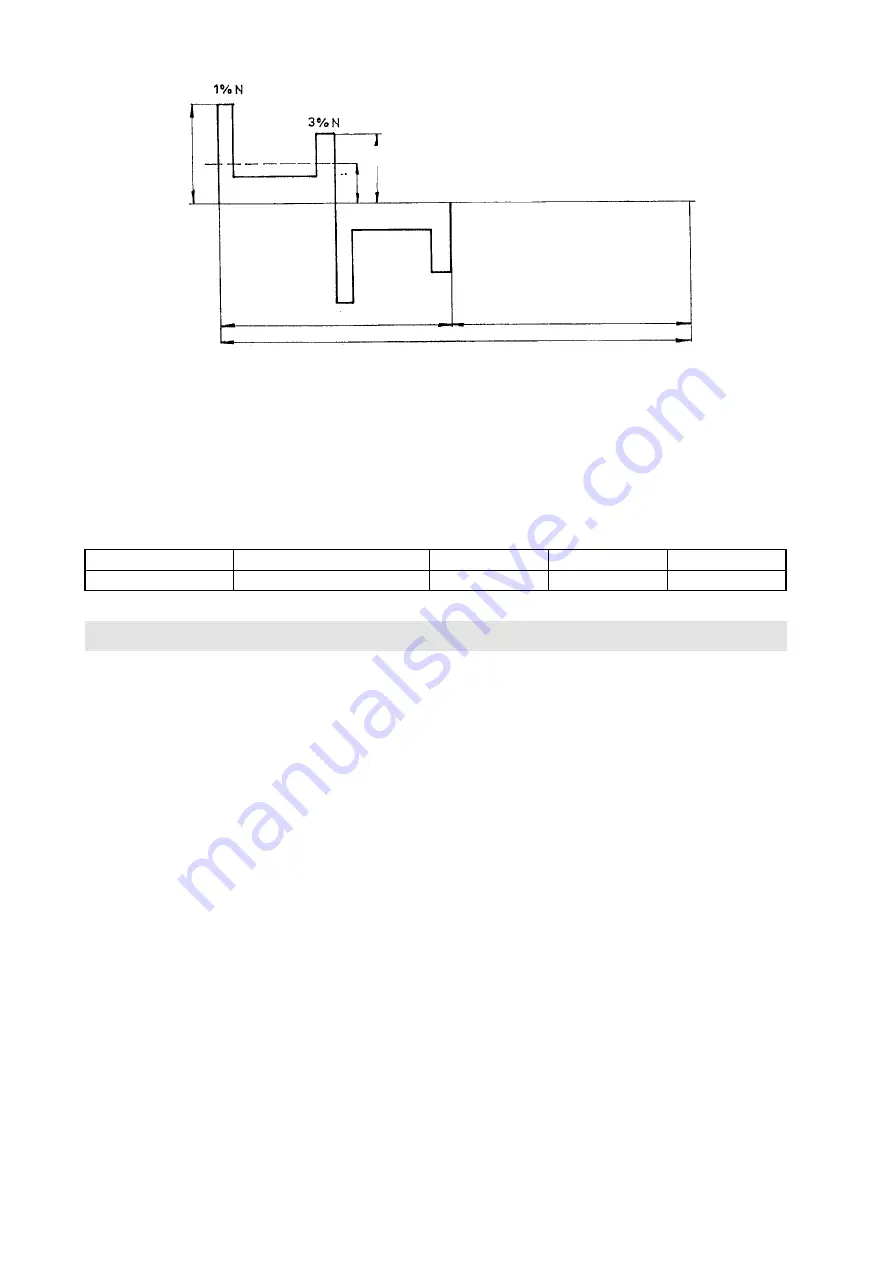
5
Service life of actuators
The actuator intended for shut-off valves must be able to perform at least 10,000 operating cycles
(C - O - C).
The actuator intended for regulating purposes must be able to perform at least 1 million cycles with operation time
(during
which the output shaft is moving)
at least 250 hours. Service life in operating hours
(h)
depends on load and number of switching.
Not always, high frequency of switching influences positively accuracy of regulation. For attaining the longest possible faultless
period and service life, frequency of switching is recommended to be set to the lowest number of switching necessary for the
given process. Orientation data of service life derived from the set regulation parameters are shown in the following table.
Service life of actuators for 1 million starts
Service life [h]
830
1 000
2 000
4 000
Number of starts [1/h]
Max. number of starts 1200
1 000
500
250
4. TECHNICAL DATA
Supply voltage
The rated supply voltage of the actuators is 3 x 230 / 400 V, 50 Hz with permissible line voltage fluctuations between
+10 % and -15 % and frequency shift within ±2 %.
Protective enclosure
Protection of the actuators
MODACT MTN (MODACT MTN Control) – IP 55
MODACT MTP (MODACT MTP Control) – IP 67
Noise
Acoustic pressure level A
max. 85 dB
(A)
Acoustic power level A
max. 95 dB
(A)
Tripping thrust
At the factory, the tripping thrust has been adjusted within the min./max. range giving in Table 1, according to the
customer’s requirements. If no tripping thrust adjustment is required the actuator is adjusted to its maximum tripping thrust.
Starting thrust
The starting thrust of the actuator is a calculated value determined by the starting torque of the electric motor and
the total gear ratio and efficiency of the actuator. After run reversation, the actuator can produce a starting thrust for the
duration of 1 to 2 revolutions of the output shaft when torque-limit switching is locked. This can take place in either end
position or in any intermediate position.
Self-locking
The actuator is self-locking provided that the load only acts in the direction against motion of the actuator output shaft.
Self-locking is ensured by a roller arrest immobilizing the electric motor rotor even in the case of manual control.
In order to observe safety regulations, the actuators cannot be used for driving transportation lifting devices with possible
transport of persons or for installations where persons can stand under the lifted load.
Course of working cycle
Fz
Starting thrust ≥ 1,3 . Fv
Fstř Average mean load thrust
Fv
Maximum mean tripping thrust
F
z
F
stř
F
v
Cycle period
Operating time N
Idling time R