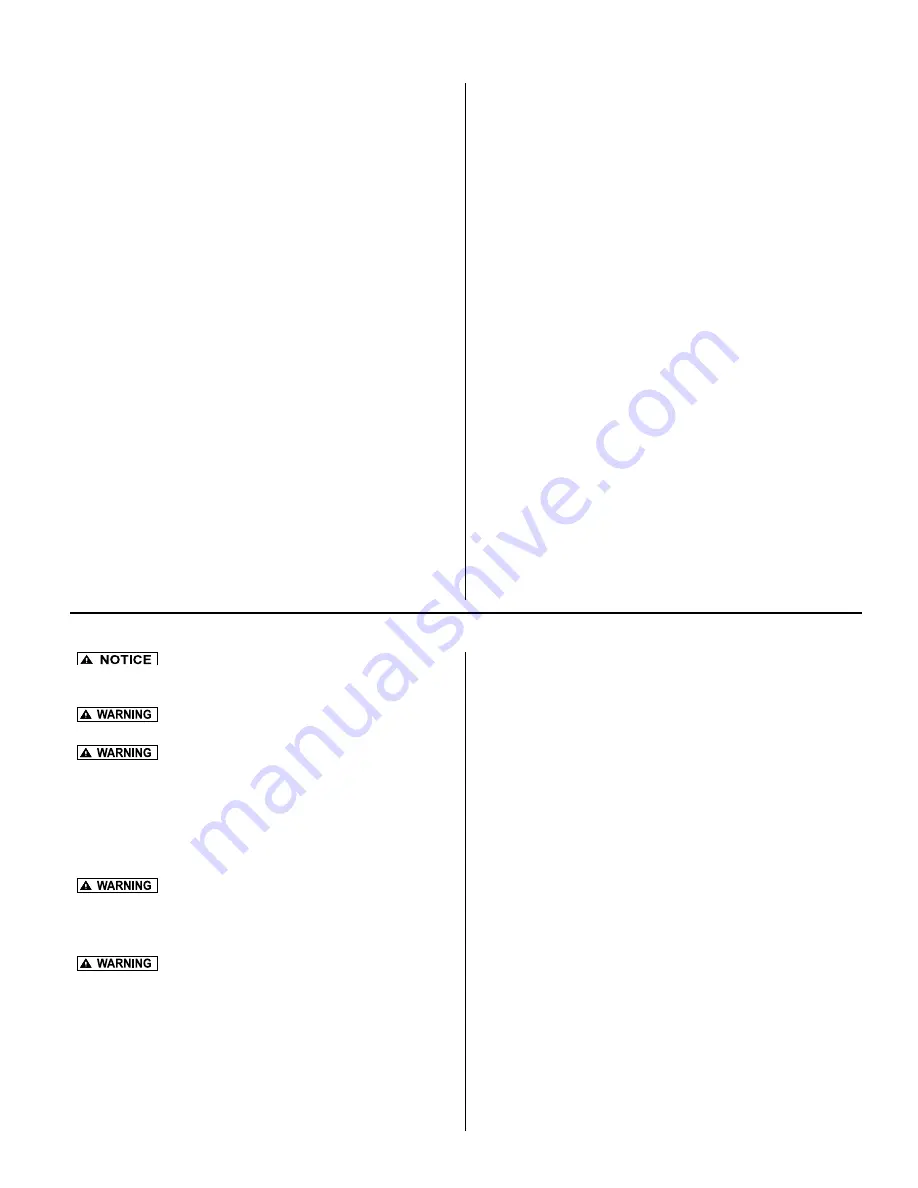
7
© Copyright 2013 Zoeller Co. All rights reserved.
OPERATION
GENERAL
Zoeller pumps are lubricated and tested at the factory prior to shipment and require
minimum pre-start-up maintenance.
Maximum liquid temperature of a continuous operating pump liquid for this model
pump must not exceed 104°F (40°C). For longest service life, all pumps should be
totally submerged on long pumping cycles.
These units are not designed to handle liquids other than sewage. If pump is used
in water contaminated with heavy, viscous, or abrasive materials, the warranty will
be voided.
NAMEPLATE DATA
The nameplate, located on the top of pump, indicates specific information about the
construction of the pump. The model number, date code, and serial number information
should be recorded on the front page in the “Owner’s Information” section of this manual.
SHORT TERM STORAGE
If pump is to be stored, the following is advised:
• Store pump inside whenever possible or cover with some type of protective covering.
• Tape or seal in plastic bag the terminal ends of wire leads.
• Spray coat unpainted surfaces with rust inhibiting oil.
• The impeller should be rotated every three months in order to keep the seals
lubricated and prevent a permanent set.
If panel is to be stored, the following is advised:
• Store the panel inside whenever possible and leave in the shipping box.
• All openings shall be sealed.
• Store in an upright position.
• Do not stack anything on top of panel.
START-UP PROCEDURE
Before placing the equipment into operation the following should be checked:
• Correct pump rotation (3 phase units only).
• Clean pit.
• Panel dry, securely installed and properly sealed.
• Floats positioned properly.
• Discharge valves open.
• 5mm (
3
/
16
”) vent hole drilled in pipe between check valve and pump.
Once the above has been verified, proceed with the following checks:
• Pump power cables properly connected to panel.
• Float cables properly connected to panel.
• Conduit connections to panel are properly sealed.
• Thermal overload adjustments made in the panel.
• After installing the pump into the containment area with adequate submergence,
open the discharge valve fully. Start the unit using manual controls. If flow is ap
-
preciably less than rated performance, pump may be air locked. To expel trapped
air, jog the unit several times, using the manual controls.
• Have a qualified electrician take voltage and current measurements on the black
wire of single phase or all three power wires of three phase with the pump running.
Record these readings in the space provided in the
“Owner’s Information”
section
on page 1 of this manual for future reference.
After the preoperational functional test has been completed, system is ready for opera-
tion. Zoeller requires the completion of a Start-up Report (ZM1074_Eb) whenever a
system is started for the first time or after a system has had a significant change take
place (i.e. pump replacement, overhaul, etc.). A copy of the Start-up Report should
remain with the system for future reference.
ADJUSTMENT PROCEDURE
Pumps: No adjustments are required other than assuring correct rotation.
Panels: The thermal overloads in the panel must be set to the F.L.A. rating on the
pump nameplate (or refer to pump data sheet).
Floats:
Refer to the system drawing for desired location of each float function.
Valves: Shut-off valves should be placed in the fully open position. Systems should
not be operated for extended periods of time with the discharge valves
partially closed due to damaging the valve.
SHUTDOWN PROCEDURES
If a system is shut down for more than six months, the following is recommended:
Pumps: If pit is to remain dry, the pump can remain in the pit. With the pump in
the pit, it should be operated for five minutes once every three months. If
the pit is to remain wet, the pump should be removed and stored as noted
above.
Panels: The panel should have all openings sealed to prevent moisture and dust from
entering the enclosure. Prior to restarting system, the panel should be inspected
for presence of moisture and any loose connections.
Valves: Consult the valve/actuator supplier for information concerning these system
components.
MAINTENANCE
PREVENTIVE MAINTENANCE
Preventive maintenance will to ensure a long service life from the product. Provided
is a suggested maintenance schedule.
Every month:
• Check for proper and unobstructed float operation.
• Listen for proper check valve operation.
• Duplex Units - Check for even operating times. Uneven times indicate a
defective unit, float switch or control.
• Inspect the panel for any presence of moisture in enclosure, loose connections, and
general component condition.
Check out location and condition of float switches.
Every year:
• In addition to the monthly checks, the basin should be inspected and cleaned. Any
defective components should be replaced. Inspect and remove any sand, debris,
or mud present in the pump basin assembly.
Every two years:
• Check insulating oil in motor and seal chambers. Inspect oil for contaminations
as follows:
• Clear oil, no burnt odor - Oil, motor and seals are in satisfactory condition.
• Dark oil, burnt odor - Pump motor has overheated. Check the motor winding
resistance to ground. Ohm readings of 1 megohm or higher is required. If lower
readings are present, return the unit to an Zoeller Authorized Service Station for
service.
• Milky, emulsified oil - Seals have failed. Unit must be returned to an authorized
service facility for service.
• Dispose of the motor insulating oil properly if replacement is required.
• Inspect power cables for damage or wear. Replace immediately if damage or wear
is detected.
• Inspect impeller for damage or wear. Replace as required by a Zoeller Authorized
Service Station.
DOUBLE SEAL PUMPS
• Double seal pumps offer extra protection from damage caused by seal failure.
• Oil in a motor housing and lower seal cavity should be checked when pump is
serviced. If oil from the motor housing contains water or other contamination,
both seals should be replaced during maintenance. Always replace with new
factory recommended oil and service parts. All repairs must be made by a
Zoeller Authorized Service Station.
Repair and service should be performed by Zoeller Company
Authorized Service Station only.
SAFETY PROCEDURES
For your protection, always disconnect pump and panel from its
power source before handling.
Never enter the basin until it has been properly vented and tested.
Any person entering a basin should be wearing a harness with safety rope extending
to the surface so that they can be pulled out in case of asphyxiation. Sewage water
gives off methane and hydrogen sulfide gases, both of which can be highly poisonous.
Installation and checking of electrical circuits and hardware should be performed by
a qualified electrician.
Pump is never to be lifted by power cord.
Unit must be flushed and disinfected, inside and out, prior to servicing.
GENERAL SYSTEM INSPECTION
Before the system is placed into operation, a system Start-up Report should be
conducted by a qualified technician.
Wiring and grounding must be in accordance with the governing
electrical code and all applicable local codes and ordinances.
LUBRICATION PROCEDURES
No lubrication is required.
If pumps are to be stored for more than six months, refer to short term storage
procedure in the Operation section.