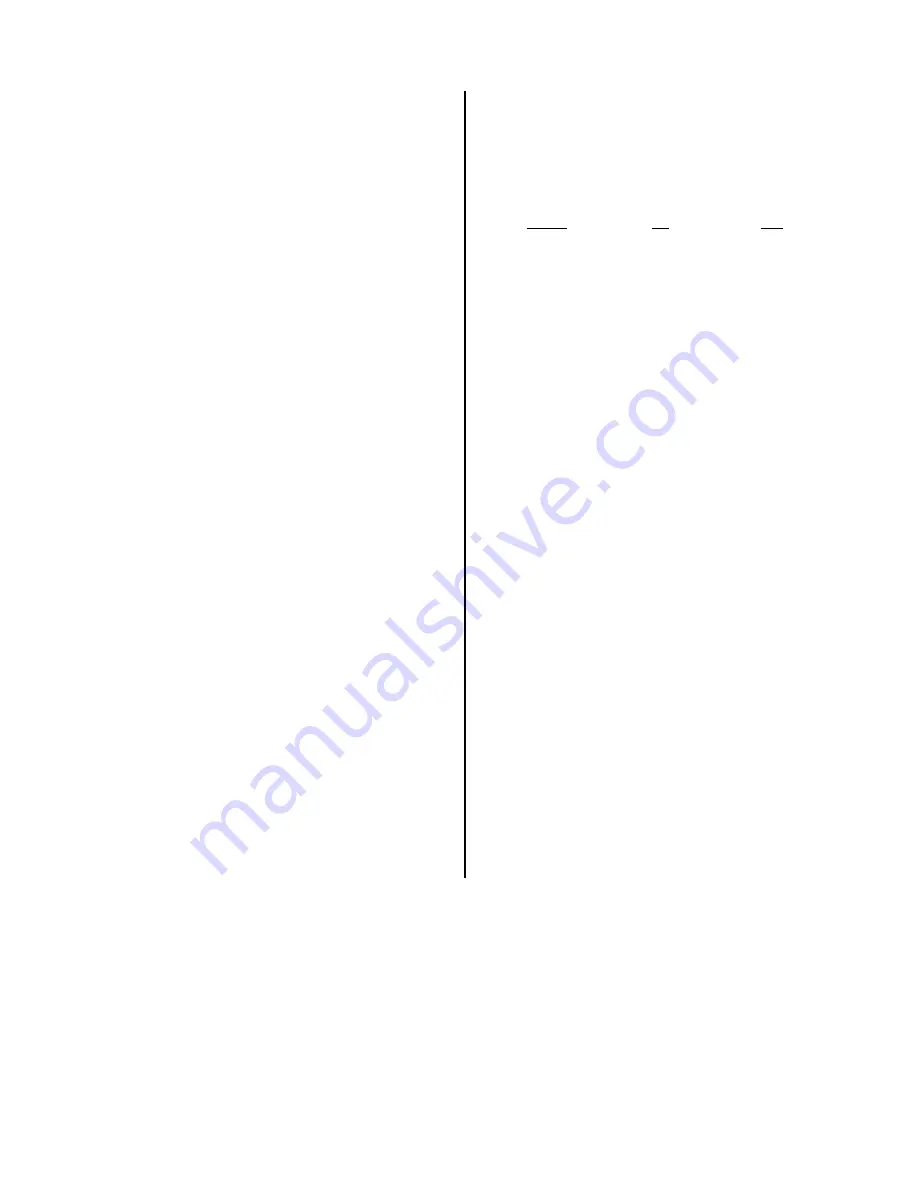
11
© Copyright 2014 Zoeller
®
Co. All rights reserved.
OPERATION
GENERAL
Zoeller pumps are lubricated and tested at the factory prior to shipment and
require minimum pre-start-up maintenance.
Maximum operating temperature of pump liquid must not exceed 104°F (40°C).
These units are not designed to handle liquids other than effluent: 160 and 180
or sanitary sewage: 280, 290 and 400. If pump is used to dewater areas with
contaminated liquids with heavy or abrasive materials, the warranty will be voided.
NAMEPLATE DATA
The nameplate, located on the side of the pump, indicates specific informa-
tion about the construction of the pump. The model number and date code
information should be recorded on the front page in the “Owner’s Information”
section of this manual.
SHORT TERM STORAGE
When not in use, the pump should be stored and the following is advised:
• Store pump inside whenever possible or cover with some type of protective covering.
• Tape or seal in plastic bag the terminal ends of wire leads.
• Spray coat unpainted surfaces with rust inhibiting oil.
• The impeller should be rotated every six months in order to keep the seals
lubricated and not develop a permanent set.
If panel is to be stored, the following is advised:
• Store the panel inside whenever possible and leave in the shipping box.
• All openings shall be sealed.
• Store in an upright position.
• Do not stack anything on top of panel.
START-UP PROCEDURE
Before placing the equipment into operation the following should be checked:
• Clean pit.
• Electrical boxes dry and securely installed.
• Floats positioned properly.
• Discharge valves open.
• 3/16” vent hole drilled in pipe between check valve and pump.
Once the above has been verified proceed with the following checks:
• Pump power cables and control floats properly installed and voltage verified.
• Conduit connections to panel are properly sealed.
• After installing the pump into the containment area, with adequate submer-
gence, open the discharge valve fully. Start the unit using manual controls.
If flow is appreciably less than rated performance, pump may be air locked.
To expel trapped air, jog the unit several times, using the manual controls.
• Have a qualified electrician take voltage and current measurements with the
pump running. Record these readings in the space provided in the “Owner’s
Information” section on page 1 of this manual for future reference.
ADJUSTMENT PROCEDURE
Pumps: No adjustments are required.
Floats: Nonautomatic - Refer to the system drawing or to the panel wiring
schematic for the desired location of each float switch setting.
Automatic - Float is factory set to provide approximate on/off levels
as follows:
SERIES
ON
OFF
X160/X190 19-1/2"
9-3/4"
X280
19-3/4"
10"
X290
19-1/2"
9-3/4"
A tighter pumping range can be set by moving the float stop closer
to the float thereby lowering the "on" point.
Valves: Discharge valves should be placed in the fully open position. Sys-
tems should not be operated for extended periods of time with the
discharge valves partially closed due to damaging the valve.
SHUTDOWN PROCEDURES
If a system is shutdown for more than six months, the following is recommended:
Pumps: If pit is to remain dry, then the pump can remain in the pit. With the
pump in the pit, it should be operated for five minutes once every
three months. If the pit is to remain wet, the pump should be removed
and stored as noted above.
Panels: The panel should have all openings sealed to prevent moisture and dust
from entering the enclosure. Prior to restarting system, the panel should
be inspected for presence of moisture and any loose connections.
Valves: Consult the valve/actuator supplier for information concerning these
systems components.