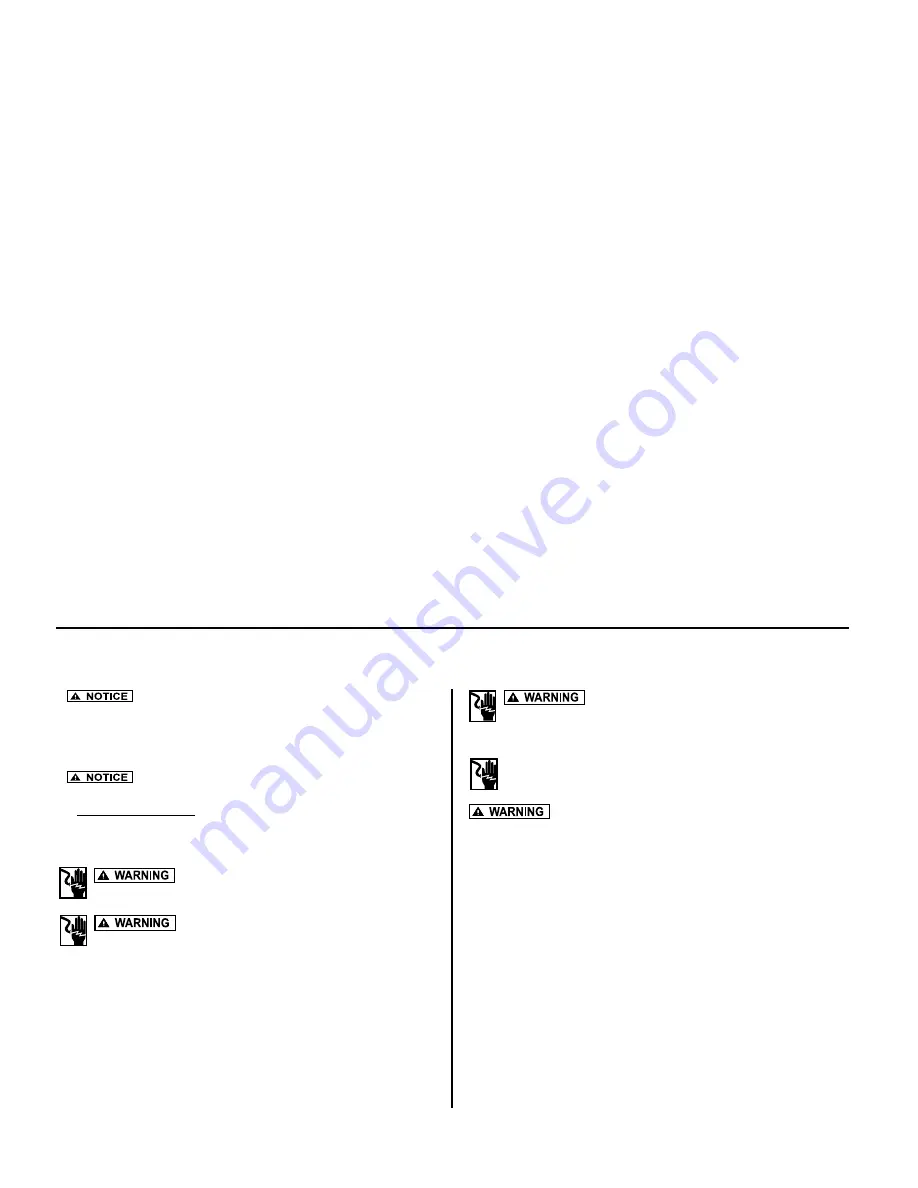
10
© Copyright 2014 Zoeller
®
Co. All rights reserved.
Repair and service must be performed by a firm approved by
Zoeller Company to repair a pump with an explosion-proof motor in accordance
to the guidelines listed in Policy # FM0212-3d. Contact the Zoeller Product
Support Department for additional information.
If the motor housing or cord cap is disassembled or
repaired by a firm NOT approved to work on explosion-proof motors,
the explosion proof rating is void, and the FM and CSA tags MUST BE
REMOVED FROM THE PUMP.
SAFETY PROCEDURES
For your protection, always disconnect pump and
panel from its power source before handling.
Never enter the basin until it has been properly vented
and tested. Any person entering a basin should be wearing a harness
with safety rope extending to the surface so that they can be pulled
out in case of asphyxiation. Sewage water gives off methane and hydrogen
sulfide gases, both of which can be highly poisonous.
Installation and checking of electrical circuits and hardware should be performed
by a qualified electrician.
Pump is never to be lifted by power cord.
GENERAL MAINTENANCE
Unit must be cleaned and disinfected, inside the
pumping chamber and all exterior surfaces, prior to servicing.
GENERAL SYSTEM INSPECTION
Before the system is placed into operation, it should be inspected by
a qualified technician.
Wiring and grounding must be in accordance with the National
Electrical Code and all applicable local codes and ordinances.
LUBRICATION PROCEDURES
No lubrication is required.
If pumps are to be stored for more than six months, refer to short term storage
procedure in the Operation section.
PREVENTIVE MAINTENANCE
Preventive maintenance is recommended to ensure a long service life from the
product. Provided is a suggested maintenance schedule.
Every six months:
• Inspect and test system for proper operation.
• Check for proper and unobstructed float operation.
• Listen for proper check valve operation.
Every 5 years or 10,000 hours of operation:
• Remove pump, inspect and service using a Zoeller rebuild kit.
• Flush and clean basin.
It is very important that these units be connected for proper rotation. Since no rotating parts are visible without removing the pump from the pit,
the rotation on 3 phase units should be checked before installation into the pit as follows:
After the proper electrical connections are made, momentarily energize the pump observing the direction of kick back due to starting torque. The rotation is
correct if the kick back is in the opposite direction of the rotation arrow. If the rotation is not correct, disconnect power and switch any two power leads. Turn
power back on and retest for proper rotation.
SENSOR WIRES (See pages 8 and 9)
The power and sensor wires are contained in the same cord. The green wire is a ground connection. All wires must terminate in the control panel.
The following should be noted:
(1) The thermal sensors are normally closed and mounted adjacent to the motor windings. If internal temperatures exceed a maximum limit, the pump will
deactivate. On 3 phase models connect the white and red wires with the black tracer to the control panel's thermal cut-out terminals. The pump is able to
restart once the motor cools down. Continued deactivation of this circuit requires the attention from maintenance personnel.
(2) The seal failure wires are connected to a 330K ohm moisture detection circuit. An indicator light will activate whenever water is present in the shaft seal
cavity or cord cap assembly. Whenever the seal leak light is activated, indicating the entry of moisture into the pump, it should be removed and serviced
in order to avoid damage to the motor. Moisture sensor circuit can be checked for continuity (complete circuit) with a (Volt-OHM-Meter). Set the VOM
to read resistance and connect the VOM leads to the moisture sensor wires. The VOM should read approximately 330k Ohms. Resistance readings
significantly lower indicates an entry of moisture into the pump. If VOM reading is open then a problem exists with moisture detection circuit.
(3) The green wire shall be connected to a ground lug in the panel. Check resistance between the green ground conductor and all other wires. This resistance
reading should indicate an open circuit. If VOM reading returns a reading other than open, then a problem exists with the sensor circuit wiring or cordage
and the pump should be taken to an approved repair station.
CONTROL PANELS
These pumps are nonautomatic and they require a control panel with intrinsically safe float and moisture sensor circuits. A motor starter circuit, control circuit,
and high-water alarm circuit within the panel are standard features. Enclosures rated for outdoor use and alternating relays are often required. The following
should be noted.
(1) The seal failure sensor and thermal sensor (3 phase only) protection require that interfacing terminals and functions be incorporated into the panel.
(2) All 3 phase pumps require overload protection in panel. Use with approved motor control that matches motor input in full load amperes with overload
element(s) selected or adjusted in accordance with control instructions.
(3) Lightning arrestors, condensation heaters and elapsed-time meters are optional features that provide added protection.
INSTRUCTIONS FOR CHECKING ROTATION OF THREE PHASE UNITS