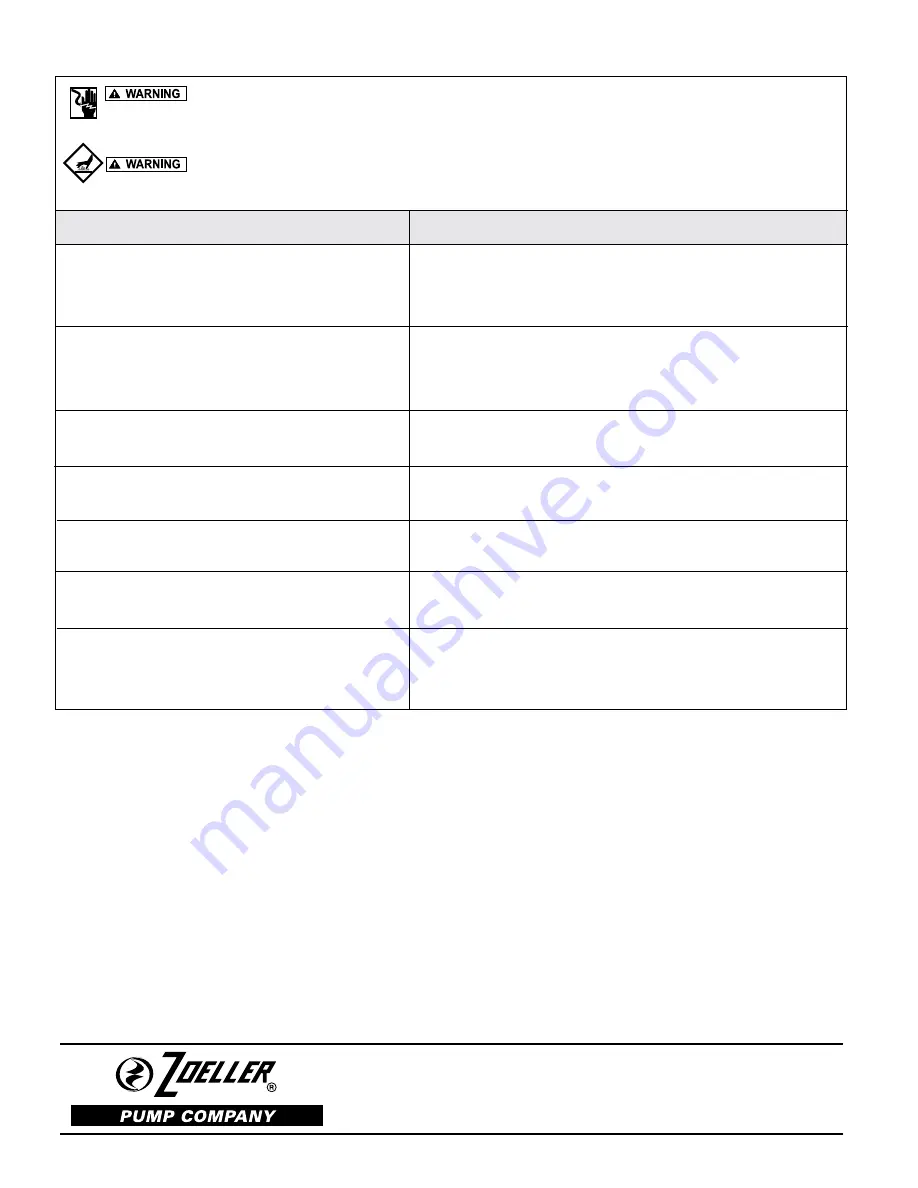
© Copyright 2014 Zoeller
®
Co. All rights reserved.
SERVICE CHECKLIST
Electrical precautions. Before servicing the pump, always shut off the main power circuit. Make sure you are wearing
insulated protective sole shoes and not standing in water. Under flooded conditions, contact your local electric company or a qualified
licensed electrician for disconnecting electrical service to the pump prior to removal.
Pumps contain oil which becomes pressurized and hot under operating conditions. Allow 2-1/2 hours after shut down
before servicing pump.
Condition
A. Pump will not start or run.
B. Motor overheats and trips on overload.
C. Pump will not shut off.
D. Pump operates but delivers little or no water.
E. Pump starts and stops too often.
F. Large red flashing light comes on at control box.
G. Grease and solids accumulate in pit around pump.
Common Causes
Blown panel or circuit breaker fuse, low voltage, thermal overload open, impeller
clogged, float switch held down or defective, incorrect wiring in control panel, water
in cap assembly.
Incorrect voltage, impeller blocked, negative head (discharge lower than intake of pump).
Pump runs continuously at low water level. Low oil level in motor shell.
Air lock, debris under float assembly, incoming sewage exceeds capacity of pump.
Intake clogged with grease or sludge, pump air locked (clear vent hole), low or
incorrect voltage, clogged discharge line, operating near shut-off head.
Check valve stuck open. Sump pit too small to handle incoming sewage. Level control
out of adjustment. Thermal overload tripping.
High water in pit. Check pump for clogging, or overload trip. See “A” and
“D” above.
Break up solids and run pump with water running into the pit. Allow level to lower
to the pump intake. Continue until solids are cleared from the pit. Do not drain
kitchen grease down the sink.
MAIL TO: P.O. BOX 16347 • Louisville, KY 40256-0347
SHIP TO: 3649 Cane Run Road • Louisville, KY 40211-1961
(502) 778-2731 • 1 (800) 928-PUMP • FAX (502) 774-3624
Your Peace of Mind is Our Top Priority
®
®
visit our web site:
www.zoeller.com