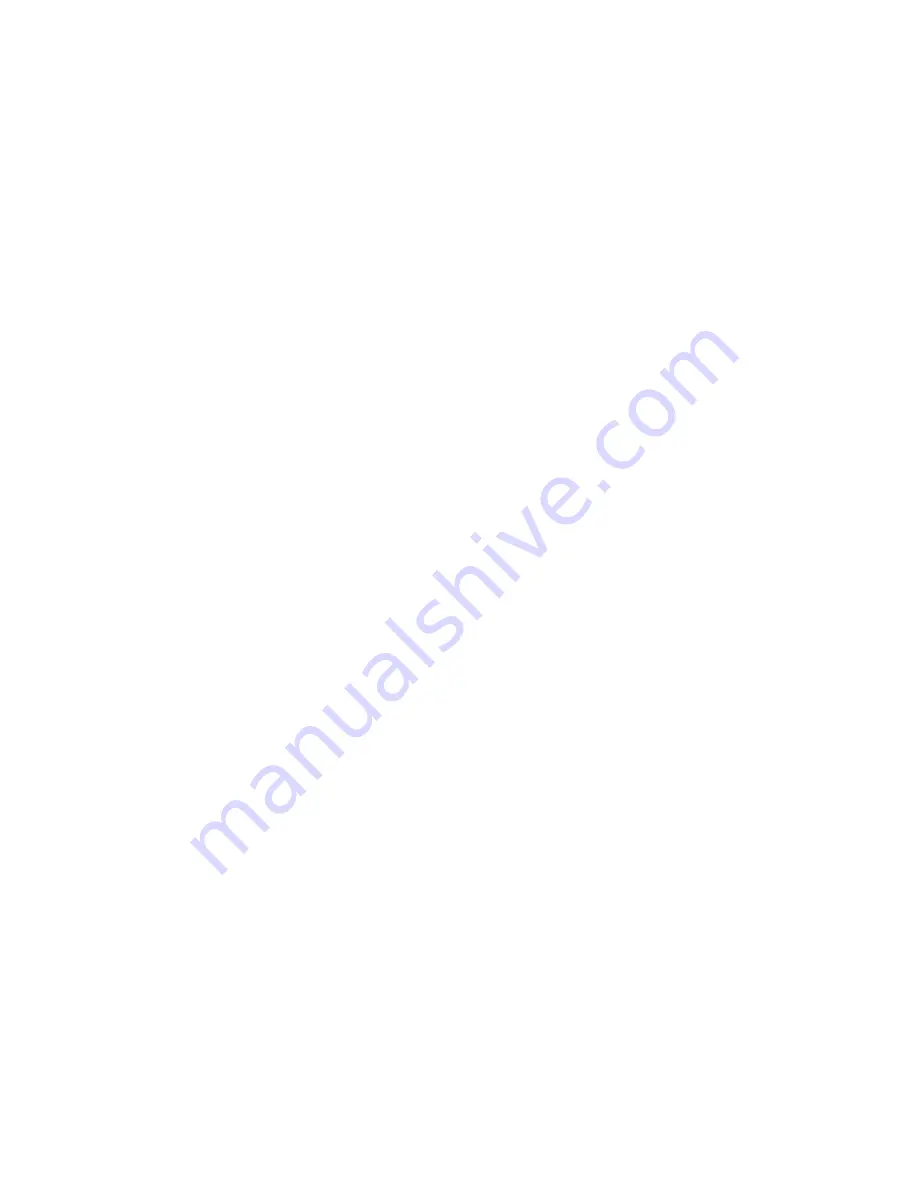
p.
41/61
EXPLANATION :
In case of changing the thermal capacity of the burner it is
required to adjust the air flow rate as well, by adjusting the position of air flow
control flap. In principal a decrease of the thermal capacity will require lower
air flow rate and vice versa. Decreasing the air flow rate is performed by
closing the air flow control flap, respectively – the increase of the air flow rate
is realized by opening that flap;
5.4.
Stopping the pellet burner of series “GP”
Stopping the operation of the burner should be performed by turning OFF the
“START” signal from the control module of the heat consumer unit.
Respectively, the starting process should be invoked by turning ON the
“START” signal of that control module. In case that the heat consumer is a hot
water boiler this “START” signal is actually the status of the operating
thermostat of the boiler. In case that the burner will not operate for a relatively
long period of time, it is recommended to shut down the central power supply of
the unit and clean the ash deposited in the combustion chamber, beneath it, as
well as other surfaces of the combustion chamber, the photosensor should be
checked/cleaned as well.
ATTENTION:
●
In case that the burner will not operate for a long period of time, then
thorough ash deposit cleaning procedure should be performed. The ash
layer acts corrosively on the carbon steel surfaces, which will lead to a
decrease of the lifetime of the burner’s main module. It is obligatory to
perform service procedures and preventive observations of the unit by
trained service personal only as well as thorough cleaning at the end of
the heating season. Completing these requirements will ensure long
exploitation duration of the burner and its high efficiency and reliability;
●
In case there is signal to stop the operation of the burner, the fuel delivery
stops, but its air fan continues to run. That’s why at stop signal the burner
continues to operate and the combustion process will continue to release
heat energy, which makes the system quite inert. This particular feature
should be concerned, especially when a local heating system is equipped
with radiators with thermostatic control valves (or any other control
elements), which stop the flow of the circulating fluid and thus the
released in the combustion process heat energy could not be transferred
(dissipated) and thus the hot water boiler could be overheated. That’s
why in case the pellet burner of series “GP” operates in a local heating
system, which have heating elements with thermostatic valves, these
valves should not should be cutting the heating fluid flow rate, but should
allow a minimal flow rate in order to allow heat dissipation in any way. It